A Living Building Project Journey, Part-15
Construction Updates from the Site 1
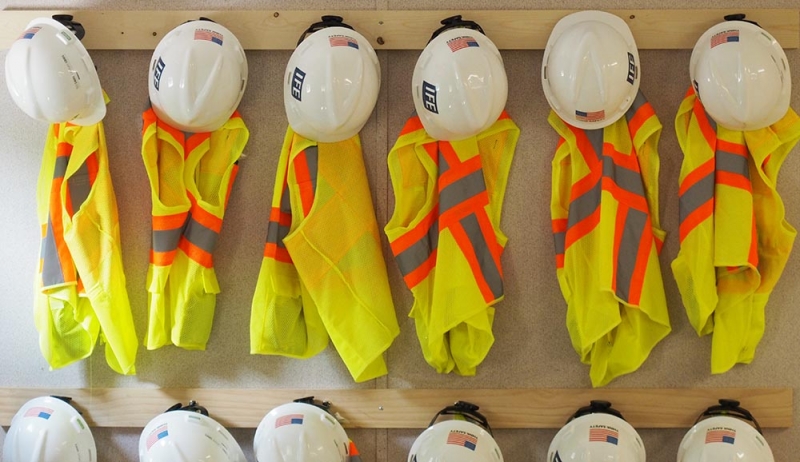
Live Camera
Since active construction began in March 2018, a publicly-accessible live camera has taken a picture of the Kendeda Building for Innovative Sustainable Design construction site every few minutes, accessible at https://app.oxblue.com/open/skanska/livingbldggatech
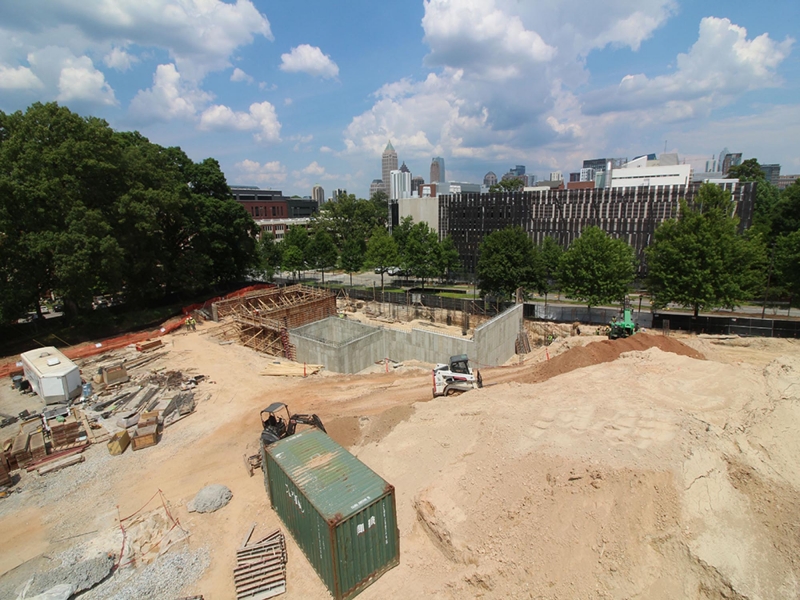
Figure 1. An image of the site from the camera at 3:05 pm on May 10, 2018.
Users can follow the progress using features such as a visual timeline, splitting or overlaying images from different dates and times, etc. The camera has a built-in weather sensor to track temperature, cloud cover, heat index, visibility, pressure, wind speed, dew point, and relative humidity. Weather data measured so far is available for download in a spreadsheet format; this can be useful for researchers because the microclimate of a specific location sometimes varies from common sources of weather data, such as airports.
Net Positive Waste
The Net Positive Waste Imperative under the Materials Petal of the Living Building Challenge (LBC) provides guidance to the project team on reducing or eliminating the production of waste during design, construction, operation, and end-of-life phases of the project. There are two components to this Imperative:
- Use of at least one salvaged material per 5382 ft² of the project (seven on this project)
- Creation and execution of a ‘Material Conservation Management Plan’ that explains how the project optimizes materials during all the phases mentioned above.
The project team developed a Material Conservation Management Plan during the design phases that is now being implemented for the construction portion.
With respect to the waste reduction or elimination efforts, the segregated material types, and their percentages by weight, being diverted from landfill during construction can be summarized as:
- Metal – 99%
- Paper and Cardboard – 99%
- Soil and biomass – 100%
- Rigid foam, carpet, and insulation – 95%
- All others (combined weight average) – 90%
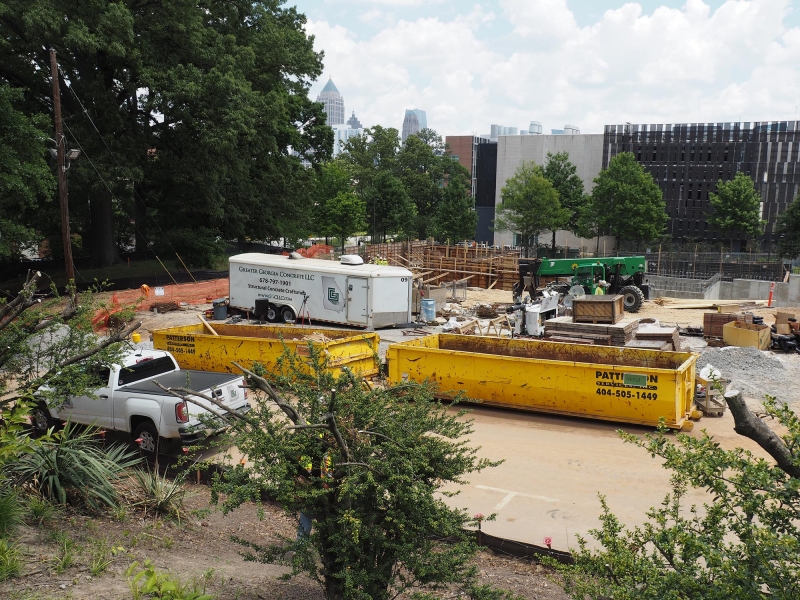
Figure 2. Construction waste dumpsters on site for wood (left) and metal (right). The third dumpster for collecting plastic bottles, paper and cardboard is outside the view of this photograph to the right.
Approximately 443 tons of asphalt has been recycled to date. All salvageable material is either being incorporated into the project in a new manner or being donated to the local Lifecycle Building Center for their retail salvage operation.
Additionally, the Skanska team is compiling a list of expected waste streams from each trade involved in the construction project and is working to identify key materials that will need to be 100 percent recycled to achieve the 90 percent recycle figure for the “All Others” target. The 90 percent goal is complicated by the fact that there are two local co-mingling options that will report a recycling rate of approximately 70 percent at a portfolio level without providing a breakdown specific to our project. One of the key identified materials across multiple future trades are plastics. The next recycling container will be all plastics, and the team has identified a general plastics recycling center to receive those materials.
There is also a small amount of compost scraps from lunch and things like coffee grounds. The Skanska team visited Georgia Tech’s West Campus Village Dining Commons, which has agreed to allow the small amount of scraps from the project to be deposited in their existing compost bins.
Material Vetting for Red List Ingredients During Construction
Compliance with the Materials Red List requirements (vetting and advocacy pertaining to the 22 red-listed materials/chemicals) has carried over from the design phases into the construction phase. We discussed the project team’s efforts to design around these Red Listed chemicals in our blog post from November 2016.
During construction, the Construction Management team is checking all materials supplied to the site for the following three questions:
- Has this material/product been fully vetted for Red List compliance?
- Has this material/product been submitted and approved for specification compliance? (the specifications provide guidance on a recommended process to address substitution requests from subcontractors, etc.)
- Have we confirmed that this material/product does not contain any other items required for installation that were not previously identified or reviewed for Red List compliance?
The answer would have to be ‘yes’ or ‘n/a’ for all three questions for the material or product to pass this filter. Though we try to identify all materials in advance, the team is finding materials and addressing them to the Red List concerns. In two instances relevant to the third question above, an unforeseen component required further vetting:
- We established a Red List compliance for a water stop (that goes between foundation footings and walls or between floor slabs and walls), but overlooked the company’s primer, which is applied prior to the water stop. We set the material aside in storage and began to quickly address the process of reviewing the product. After a full day of team effort, we had the due diligence we needed to submit a compliance effort for the primer. Because ingredient disclosure in the Safety Data Sheets amounted to less than 100%, we requested a letter from the supplier attesting that the product does not include materials on the Red List and stating the percentage of any proprietary ingredient being withheld.
- Similarly, in reviewing the underground chilled water pipe, we uncovered a mastic coating that is a common product associated with the pipe insulation. This product had little or no disclosure and the due diligence effort of requesting information from the manufacturer and reviewing it could have become an extended one. Fortunately, our project system does not require this mastic, so we eliminated the mastic from the piping installation.
Erosion and Sediment Control
Erosion and Sediment Control is not an LBC requirement but is a local regulation and an environmentally responsible construction practice. This project uses several best management practices (BMPs) to help reduce erosion of the site’s topsoil and sedimentation of streams and buffers from site runoff.
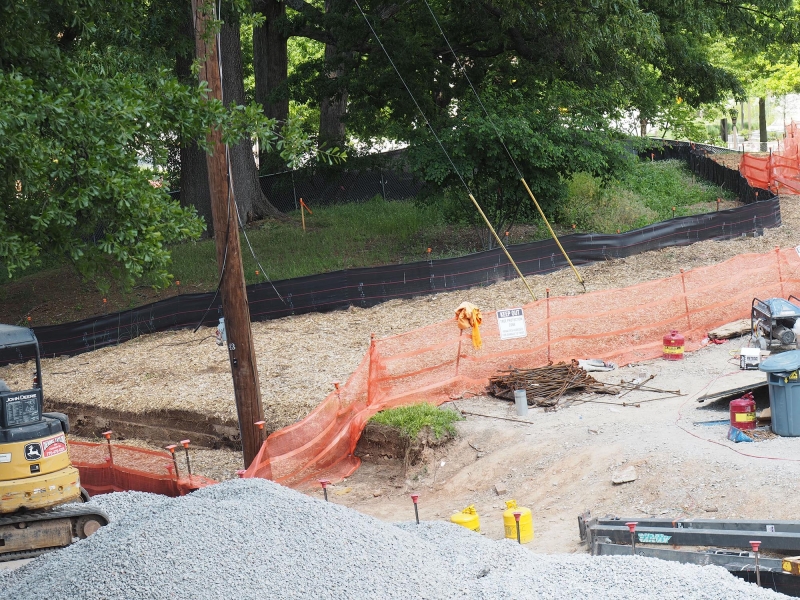
Figure 3. The black silt fence to the back of the picture is supported by metal stakes. In front of the fence is mulch generated from magnolia trees that were removed from the site prior to the beginning of construction.
FSC Wood on The Site
All non-salvaged wood used on the project is subject to Forest Stewardship Council (FSC) certification requirements, per the Responsible Industry imperative of LBC’s Material Petal.
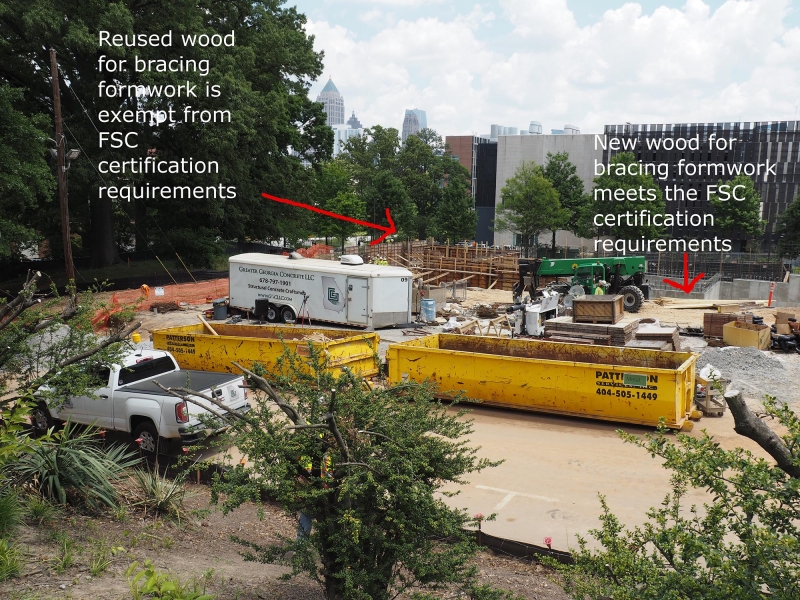
Figure 4. Salvaged wood vs. FSC wood on site
Funded through a private grant from The Kendeda Fund, The Kendeda Building for Innovative Sustainable Design at Georgia Tech is expected to become a Living Building Challenge 3.1 certified facility – the built environment's most rigorous and ambitious performance standard. The project’s design and build partners include architects Lord Aeck Sargent in collaboration with The Miller Hull Partnership, construction manager Skanska and design team consultants: Newcomb & Boyd, PAE Consulting Engineers, Uzun + Case, Biohabitats, Andropogon and Long Engineering.
Want to learn more? The team is leading site tours on Thursdays at 3 pm. Sign up here.
No comments yet