Auditing an Office Park for Site, Architecture, and Energy Improvements
Searching for Greener Solutions in Existing Buildings
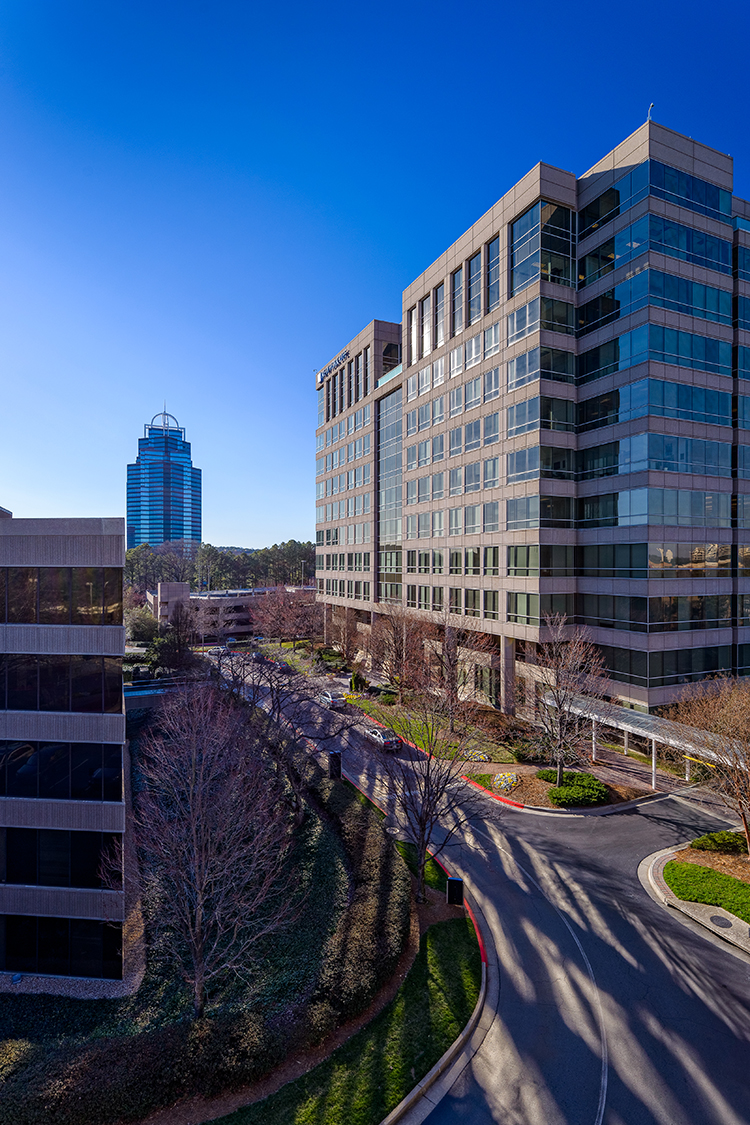
Image courtesy of Atlanta Property Group
According to the think tank Architecture 2030, approximately two-thirds of the global building area that exists today will still exist in 2040, and, without widespread decarbonization of existing buildings, meeting the Paris Agreement’s target of limiting warming to 1.5°C will be challenging.
Existing buildings retrofitted appropriately also inherently have the advantage of avoiding carbon emissions related to new construction. The exodus of occupants from nonresidential buildings when the COVID-19 pandemic hit in early 2020 is causing us to radically rethink the role of existing buildings in a post-pandemic world with a changing climate.
Atlanta Property Group (APG) doubled down on carbon reduction efforts in its 639,000 sf Palisades Office Park campus in Atlanta to help retain existing tenants and attract new clients with Environmental, Social, and Governance (ESG) priorities.
With the help of Lord Aeck Sargent and TLC Engineering Solutions, what started as an energy audit to quantify and improve operational energy and carbon emissions grew into a more holistic effort to encompass site and architectural features of the office park.
The baseline audit, which involved site walkthroughs and APG staff interviews, revealed that the project already had laudable goals and initiatives for the four buildings on campus:
- The campus was all electric, with no combustion for space or water heating end uses.
- A high Energy Star score of 83-93 between the four buildings, based on ongoing operational efficiency.
- Low Energy Use Intensity (EUI) of 43-46 kBtu/ft²/year.
- An existing LEED Gold certification under the O&M category.
- Onsite renewable energy production on its way to reaching 1 MW solar, meeting up to 17% of the campus’ energy needs.
- Proactive building maintenance and upkeep.
We were able to quantify the campus’ carbon emissions avoidance because of building reuse and sequestration opportunities from its site landscape. The avoided embodied carbon emissions from reusing the Palisades Office Park buildings, of 23,746,040 kgCO2e, are equivalent to the greenhouse gas emissions from driving an average car nearly 60 million miles, or the annual electricity use of over 4,000 homes, or the annual carbon sequestration of nearly 30,000 acres of U.S. forest.
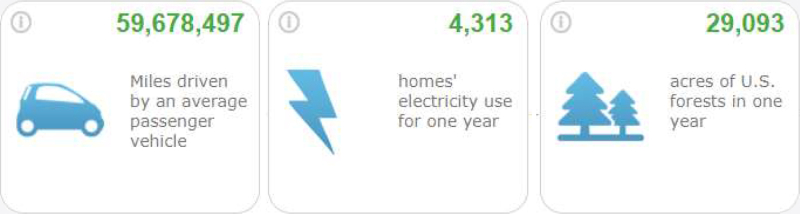
The proposed site improvements would have a net impact of sequestering an additional 1,390,949 kgCO2e over a 50-year lifespan and would be climate positive 11 years after completion. This is achieved through a robust landscape that sequesters carbon through series of natural systems. The proposed site improvements of adding densely planted trees, adding living walls or green roofs, replacing turfgrass with native vegetation, and replacing non-native plants will create the natural systems needed to remove carbon from the atmosphere. This new landscape also has other significant benefits including creating habitat for native animals and insects as well as improving biodiversity and creating a more livable environment.
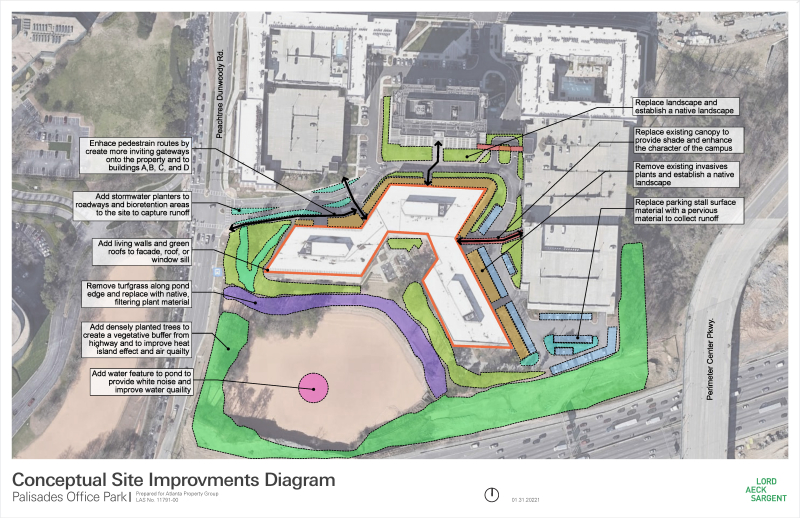
Architectural and other site improvement recommendations included lighting pollution reduction, tenant programs, improved canopies, enhanced circulation spaces, repainted facades, applied film on glazing to improve bird friendliness, softened façade, highlighted entrances, as well as more prominent plaque placements for LEED and Energy Star achievements.
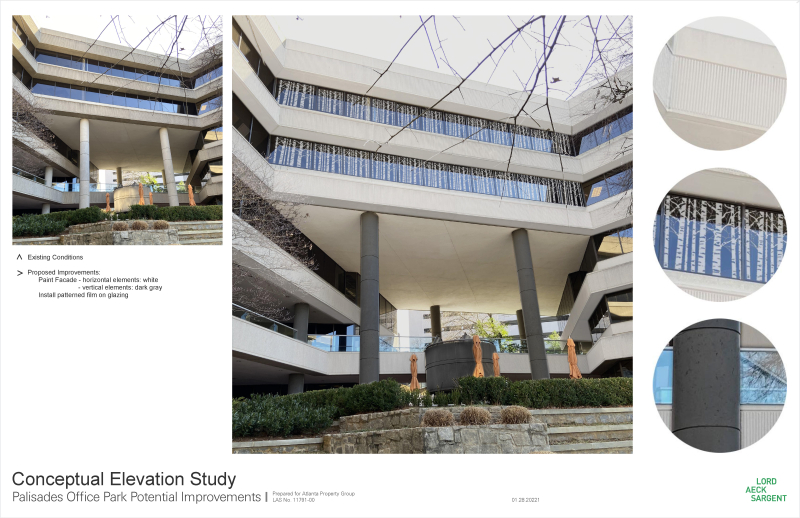
As a part of an ASHRAE level 2 energy audit, a calibrated energy model was developed to define an accurate baseline and apply energy efficiency measures (EEMs) on top of the baseline to explore their energy reduction and cost effectiveness potential. The range of measures considered was based on APG’s preliminary vetting. Such EEMs include HVAC controls upgrades, large fans in AHUs replaced by fan walls, lighting upgrades, new wind turbines, etc.
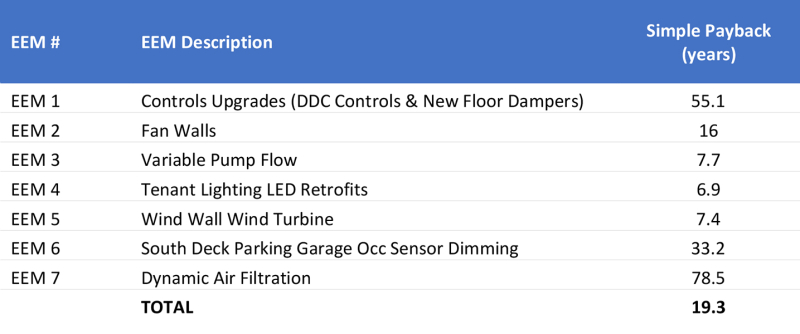
As of early 2022, APG is in the process of implementing cost effective and strategic measures to enhance the quality of Palisades Office Park’s indoor and outdoor environment while lowering its operational carbon footprint.
Comments
Sustainability in Multifamily Housing: Energy and Carbon
Solutions to Energy and Carbon Management Through a Construction Boom
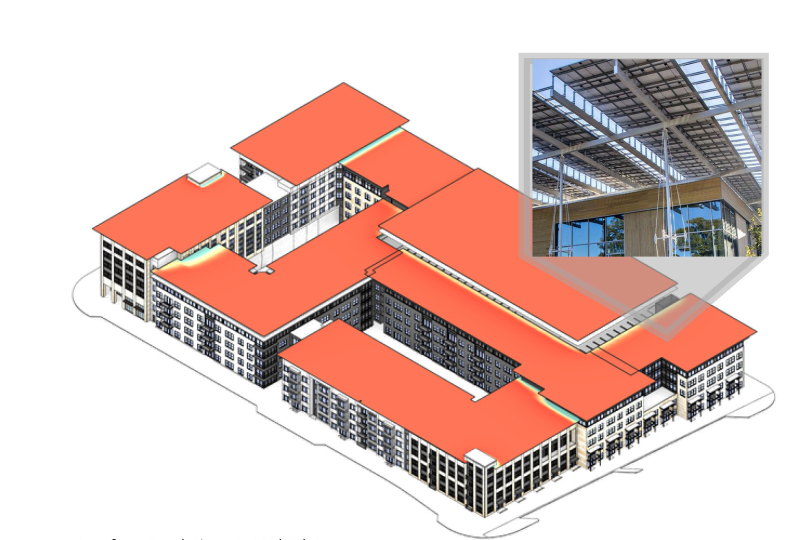
Image courtesy of Integral Consulting Engineering and Lord Aeck Sargent
According to reporting in mid-2021, new-home construction has lagged historic trend for more than two decades, and it is estimated that supply is now behind demand by 6.8 million units. This supply shortfall has only been exacerbated by the recent COVID-19 pandemic.
Solutions bridging this gap cannot ignore two essential ingredients: affordability and sustainability. While all types of housing are important, we see greater uptake of multifamily in urban areas due to scarcity of land and people’s need to live and work closer to basic services. Similarly, while there are several facets to sustainability in housing, the magnitude of construction expected in the next 40 years makes related embodied and operational carbon emissions vital to architecture’s role in fighting climate change. For these reasons, this post will focus on multifamily housing, specifically on energy and carbon.
Some challenges and solutions inherent to multifamily project energy analysis, design, construction, and operations:
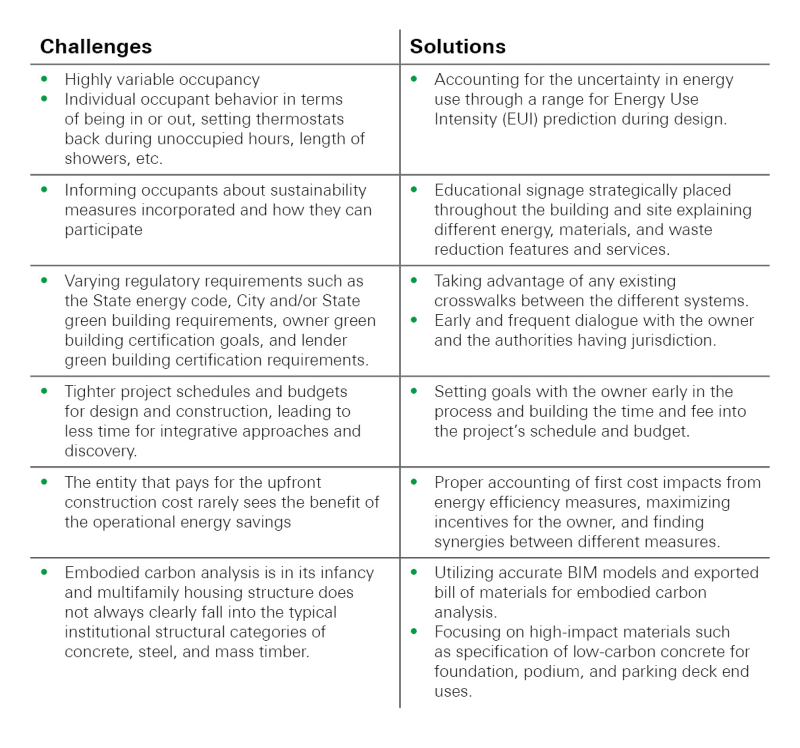
On a recent project, we are benchmarking embodied carbon impacts and identifying strategies to minimize embodied carbon intensity of the project. Concrete, gypsum and plaster, and fenestration have emerged as the highest impact areas.
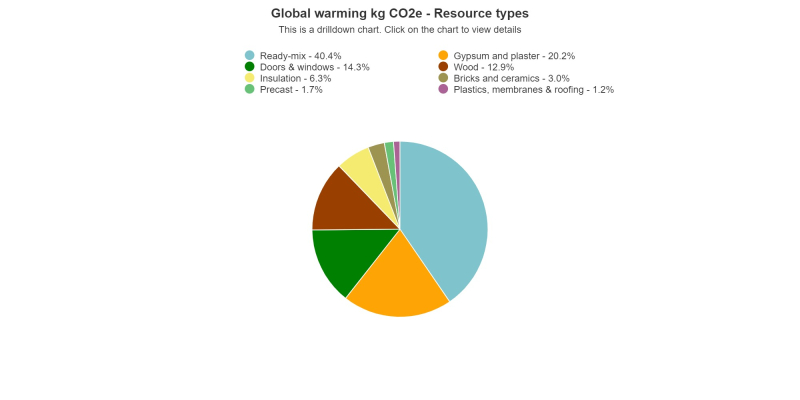
We are working closely with the structural engineer to incorporate low-carbon concrete specifications that offset high-embodied-carbon Portland cement with lower-embodied-carbon Supplementary Cementitious Materials (SCMs) and utilizing carbon sequestration technologies available in the market for concrete.
Early analysis of different design options and their impact on operational energy use/EUI and onsite solar potential have helped the owner with picking from a menu of options. Zero energy or not, we are beginning to eliminate combustion and make projects all electric, so they are ready for a future emissions-free grid.
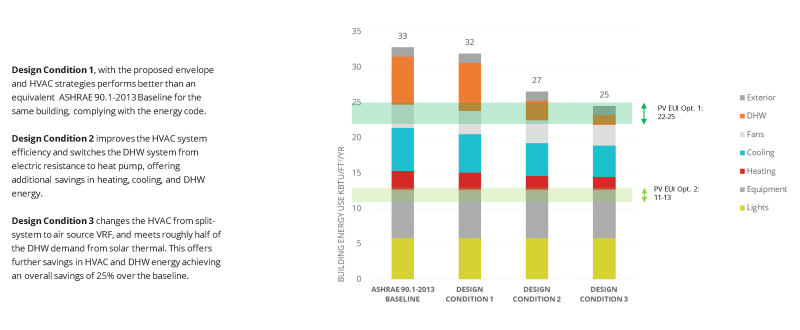
Image courtesy of Integral Consulting Engineering
We have relied on and continue to rely on New Building Institute’s Multifamily Guide for energy efficiency measures and are reviewing the recently published ASHRAE Advanced Energy Design Guide for Zero Energy Multifamily Buildings for use on future projects.
Comments
A Living Building Project Journey, Part-18
Lessons Learned from the Female Project Team Leaders
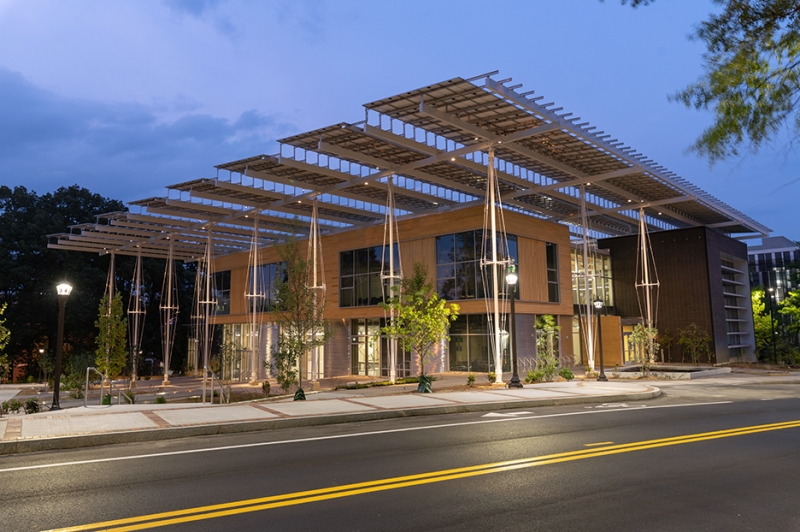
There is no shortage of coverage on the lack of gender diversity and representation in the Architecture Engineering and Construction (AEC) industry.
At LAS we recognize that there is a critical need for diversity, collaboration, and inclusion to address the historic under-representation of women, minorities, and marginalized voices in these fields. We are proud of the diversity present not only within our firm, but also in the composition of the project team of the Kendeda Building for Innovative Sustainable Design at Georgia Tech.
As the Kendeda Building approaches its grand opening, we reflect on the process to this end. The Kendeda Building is the first of its kind at Georgia Tech; it will be the largest Living Building in the Southeast; and it is has been a challenging, yet rewarding experience for the many people that make up the project team.
Given the diverse set of skills and disciplines brought together for this project, we thought it worthwhile to survey team members to see if we could learn lessons that would help guide future work and celebrate their accomplishments.
We sent an informal survey to the female leaders of the Kendeda Building project team that asked them to reflect on their experiences during the project. Clear themes on replicability, collaboration, and personal growth emerged. Here is a select representation of what they had to say.
Lessons for Replicability
“A few of the lessons I’ve learned so far from the project are as follows: 1) Energy efficient HVAC design is not difficult but needs to be very intentional, 2) although radiant floors have a relatively high first cost, they provide heating and cooling efficiently and provide it where it’s needed instead of served from the ceiling, and 3) both the general public and those involved directly in the project are interested, enthusiastic, and encouraged when they know that a net zero building design is possible and is being built right here in Atlanta.”
Beth Ann Hanson
Newcomb & Boyd
”Early consideration of acoustical finishes needs to be coordinated for LBC projects. The sustainable requirements limit some material choices. Thanks in part to the visibility this project brought to the acoustics manufacturing community, there are now more acoustical treatment options that meet the sustainable requirements. While no acoustical criteria are established for LBC projects at this time, there are other sustainable criteria that can be applied based on the type of building function.”
Jessica Clements
Newcomb & Boyd
“If education and outreach is a core tenet of a green building project, it should be written into the contracts of the design and construction teams whenever possible. Shared goals for education/outreach should be discussed and revisited throughout the project. Also recognizing that audiences and messages may change throughout the project, how do we tap into these focuses and not try to do everything all the time (in terms of outreach)? I think we've done a fantastic job spreading the word, but with such a large group coming at the outreach component from many angles, I certainly have some ideas for collaborations like this in the future.”
Drew Cutright
Georgia Tech
“Projects of this nature have a tendency to take on a life of their own – there are so many great stories to tell. That being said, it is very important to help ensure accuracy and consistency in messaging about the project. We are fortunate to have many stakeholders in this project with whom we partner to amplify our messages.”
Rachael Pocklington
Georgia Tech
It takes a village
“It still takes a village to create a Living Building! This team has been such an amazing example of the collaboration, brainpower, and passion necessary to meet the Living Building Challenge.”
Stacy Smedley
Skanska
“In order to address the most catastrophic impacts of climate change, all parties involved in shaping the built environment need to share the same vision, goals, and outcomes for a project. When that happens, great things can be achieved.”
Margaret Sprug
The Miller Hull Partnership
“Integrated design teamwork, starting from day 1 of the project, is critical for the success of any project, particularly for a Living Building. This process ensures that all voices are heard and considered throughout the process, and that the team is closely coordinated. Most importantly, this process allows for creative problem solving across disciplines.”
Emily McCoy
Andropogon (formerly)
“The success of the this project will be due to the hard work on an enormously large group of people, this project has highlighted the importance of casting a wide net as it relates to staff, student, and faculty engagement.”
Sarah Neville
Georgia Tech
“The success of a project takes into consideration the passions and hopes of the entire team.”
Tracy Fern
Lord Aeck Sargent
Personal Growth
“While I frequently think about how my personal habits impact the environment, this project has allowed me to see how my workplace habits have an impact as well. It has been a rewarding challenge to think through what resources are actually necessary for me to do my job.”
Jennifer Leavey
Georgia Tech
“It was inspiring to work on a Living Building located in a campus setting. As the team thought about how to integrate our building into the campus systems, it became easy to envision how the Living Building principles could be applied to other future and existing buildings on the Georgia Tech campus. It helped me realize the bigger potential of campuses to holistically adopt innovative and sustainable designs. A single building could be the spark that creates larger change!”
Karina Hershberg
PAE Consulting Engineers
“This project taught me a lot about communication and collaboration. Developing a solution that met the project goals and satisfied the safety intent took cooperation with the Fire Marshal, Tech campus, architects, and mechanical engineers.”
Usha Tyson
Jensen Hughes
Innovation
“Living Buildings are great incubators for advancing equity as a key piece of the sustainable built environment. We can try out new policies, procedures, systems, and approaches, linking research, education, and action, and hopefully impact broader equity work on campus moving forward.”
Jennifer Hirsch
Georgia Tech
“The most important lessons we have yet to test from the building: how are knowledge and sustainable behaviors by the campus community influenced by a building like this? How does that knowledge and experience shape behavior on the rest of campus and as a part of one’s being? OCS will be using the building as a model to understand how to educate the campus community about sustainable principles and leveraging those lessons to apply to Georgia Tech’s policies, plans, processes, and standards to amplify implementation and impact.”
Anne Rogers
Georgia Tech
Funded through a private grant from The Kendeda Fund, The Kendeda Building for Innovative Sustainable Design at Georgia Tech is expected to become a Living Building Challenge 3.1 certified facility – the built environment's most rigorous and ambitious performance standard. The project’s design and build partners include architects Lord Aeck Sargent in collaboration with The Miller Hull Partnership, construction manager Skanska and design team consultants: Newcomb & Boyd, PAE Consulting Engineers, Uzun + Case, Biohabitats, Andropogon, and Long Engineering.
Comments
Test post
This is just a test
Lorem ipsum dolor sit amet, consectetur adipisicing elit. Voluptatem facilis aliquid fuga sequi culpa, omnis voluptatibus quod quos nemo aspernatur.
Lorem ipsum dolor sit amet, consectetur adipisicing elit. Voluptatem facilis aliquid fuga sequi culpa, omnis voluptatibus quod quos nemo aspernatur.
Lorem ipsum dolor sit amet, consectetur adipisicing elit. Voluptatem facilis aliquid fuga sequi culpa, omnis voluptatibus quod quos nemo aspernatur.
Comments
Renewables Rising
Reflecting on Our History of Designing On-Site Renewable Energy Production
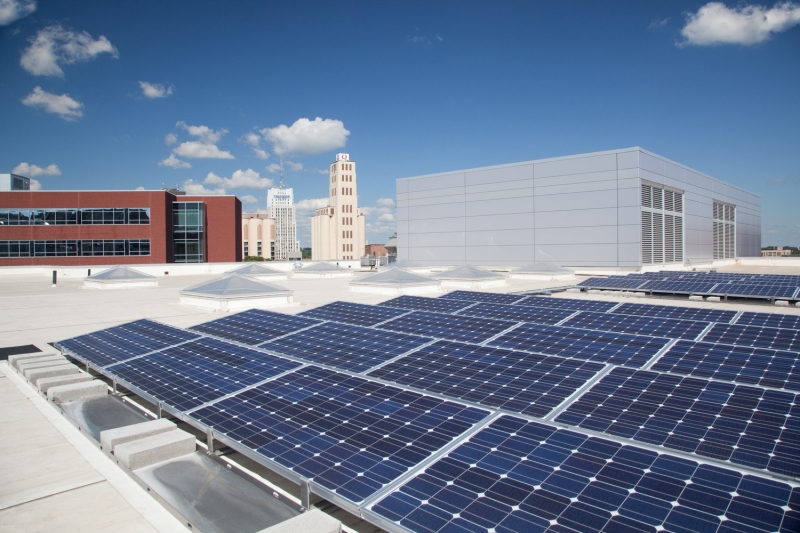
Renewable electricity production exceeded electricity produced in coal-fired power plants for the first time in U.S. history last month, with the Energy Information Administration estimating renewables outperformed coal by 16%. Unlike the grid-based fossil fuel electricity paradigm—where power is produced ‘somewhere else,’ as much of two-thirds of it is wasted, and buildings simply connect to the grid—architects and designers have a significant role to play in the nation’s transition to a distributed, efficient, clean energy future where buildings power themselves.
While market forces are beginning to favor renewable energy ahead of the more traditional and polluting sources like coal, as evidenced by last month’s milestone, the transition isn’t yet happening quickly enough to prevent the most damaging effects of anthropogenic climate change. In February 2019, NASA announced that the five warmest years in recorded history have been the last five years.
States and municipalities are taking policy leadership, with the Sierra Club reporting that as of this month, five states and 121 cities have already established 100% renewable portfolio standards.
With buildings responsible for the majority of electricity consumption in the US, the A/E industry also has a responsibility accelerate the transition to renewably-powered buildings. We can do this by designing energy efficient buildings incorporating onsite renewable energy production and storage, which will reduce overall emissions, including waste and transmission losses, while improving the resilience of our built environment.
Ed Mazria issued the call for action in 2003, with his provocative Metropolis Magazine article titled, “Architects Pollute,” and his 2030 Challenge proposed a path toward a renewable-powered built environment by the year 2030. Programs like renewable portfolio standards and the 2030 challenge, coupled with increasingly stringent energy codes, improvements in energy efficient technologies, and the steadily decreasing cost of renewable energy and energy storage are all making it easier to do the right thing.
As designers of the built environment, we take our environmental responsibility seriously. As our nation reaches these milestone events – events both positive, such as renewables out-producing coal for the first time ever, and negative, such as record high temperatures and accelerating extinctions – we’re redoubling our commitment and reflecting on our history of environmentally-responsible building designs incorporating on-site renewable energy production.
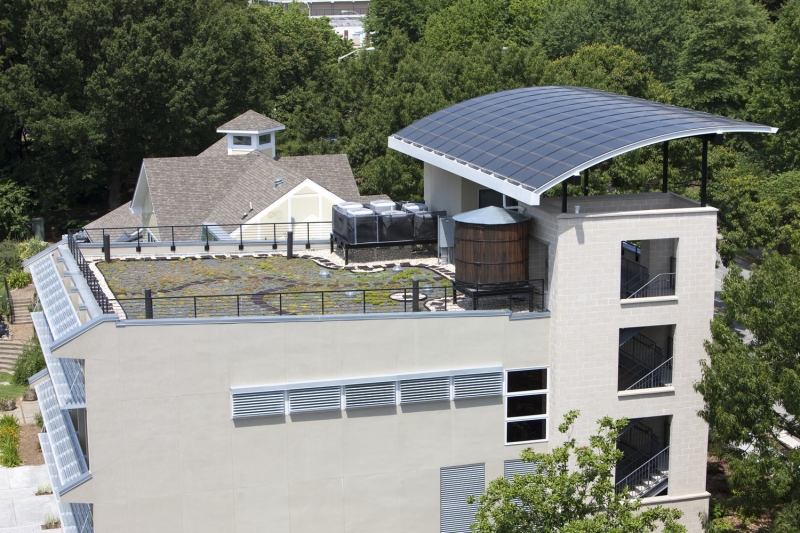
© Jonathan Hillyer
Southface Eco Office: Our first project to incorporate renewable energy featured an elevated photovoltaic array canopy that also harvests rainwater. The project is LEED Platinum certified.
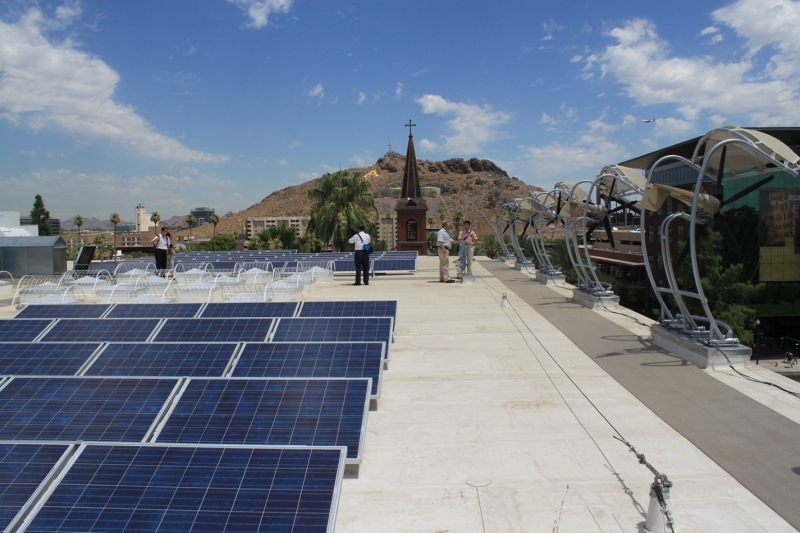
© Lord Aeck Sargent
Arizona State University’s Global Institute of Sustainability: A ‘recycled building’ featuring a hybrid renewable energy system with roof-mounted photovoltaic panels and parapet-mounted wind turbines. The project is LEED Gold certified.
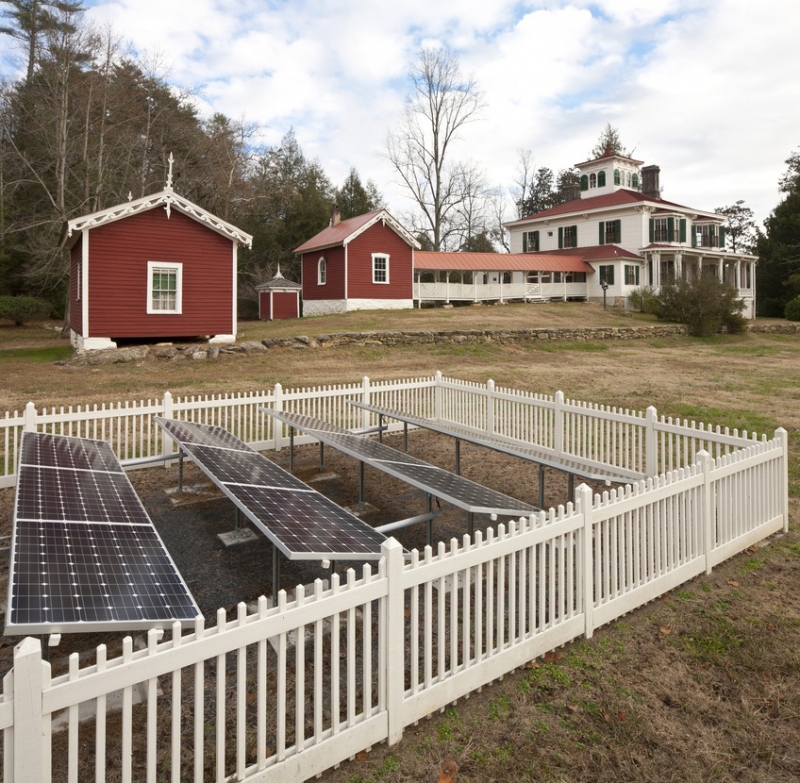
© Jonathan Hillyer
Hardman Farm: A historic preservation project for the State of Georgia restored the building’s passive cooling strategies and replaced a former vegetable garden with a new ‘solar garden’ of photovoltaic panels. The project is LEED Gold certified.
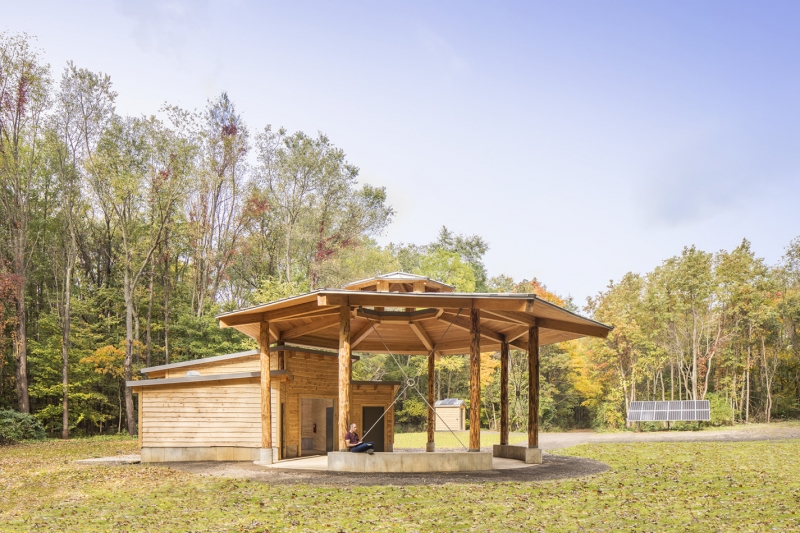
© Jonathan Hillyer
Kalamazoo College's Batts Pavilion: A fully off-grid ecological education pavilion on a formerly degraded site in the College’s Lillian Anderson Arboretum. The Net Zero project uses solar panels to fulfill its limited energy needs.
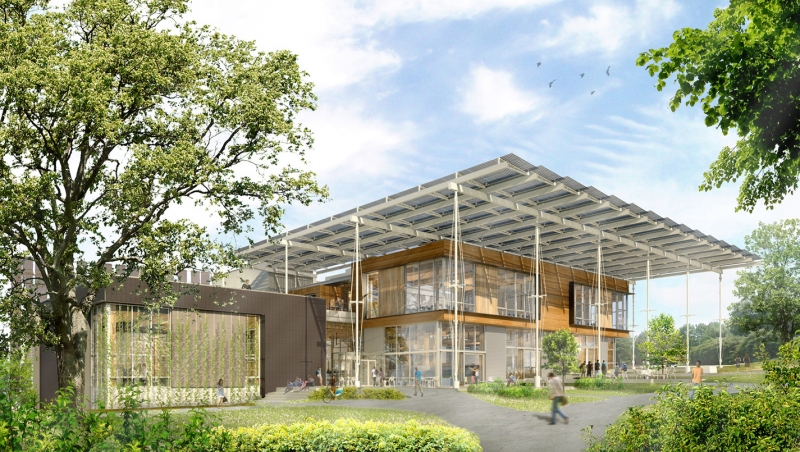
Lord Aeck Sargent in Collaboration with The Miller Hull Partnership
Georgia Institute of Technology’s Kendeda Building for Innovative Sustainable Design: When the Kendeda Building opens this fall at Georgia Tech it will not only meet the programmatic needs of the university, but will also be a net exporter of renewable energy, producing more energy than it needs to operate with its roof-mounted solar array. The project is targeting Living Building Challenge and LEED Platinum certification.
Comments
A Living Building Project Journey, Part-17
The Photovoltaic System Design
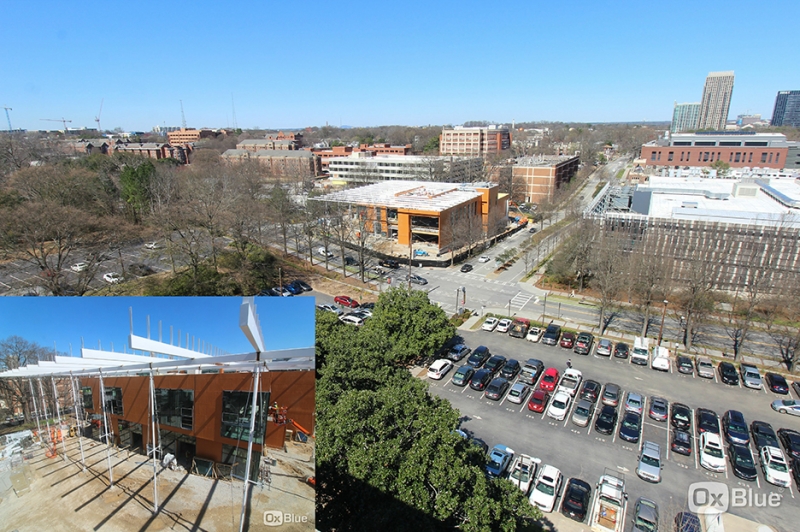
Figure 1. Construction snapshot on March 5, 2019
The Kendeda Building for Innovative Sustainable Design, currently under construction, is close to installing its photovoltaic (PV) system, which includes solar panels and the balance of system components. During operation, this renewable energy system will exceed all the annual energy needs of the building (predicted to be 34 kBtu/sf/year or a total of 328 MWh in the first year. In fact, simulations of the building’s normal usage indicate a substantial estimated net positive margin of more than 25 percent, which amounts to over 100 MWh in the first year. The system should produce 25 percent more energy than the building’s needs.
Let’s take a look at the different components of this system.
Structure Supporting PV
Matt Kantner of Katerra, who was a member of Uzun + Case’s team when he worked on the structural design of the project, explained the team’s structural strategy. As you can see in the image above, the design uses steel columns to support a tubular, horizontal array of steel beams. Steel was selected because of its high strength-to-weight ratio, dimensional stability, and weather resistance.
The tubular array design, which uses closed shapes, minimizes the use of material when serving long unbraced spans when compared to open I-shape beams. Additionally, the array deliberately follows the spacing of the building’s timber structure so as to deliver weight loads from the solar panels straight down to the mass timber columns below.
Long overhangs that expand the array size and shade the façade on south and west necessitated tall columns from the ground. Spars, the lateral pieces at the columns’ mid-span shown below, decrease the unbraced height of the column. These spars are pre-compressed by tension rods running from the top of a column to its bottom. Like the tubular array, the column design not only decreases material use but also adds visual interest, providing a visual ‘forces diagram’ for structural engineering students.
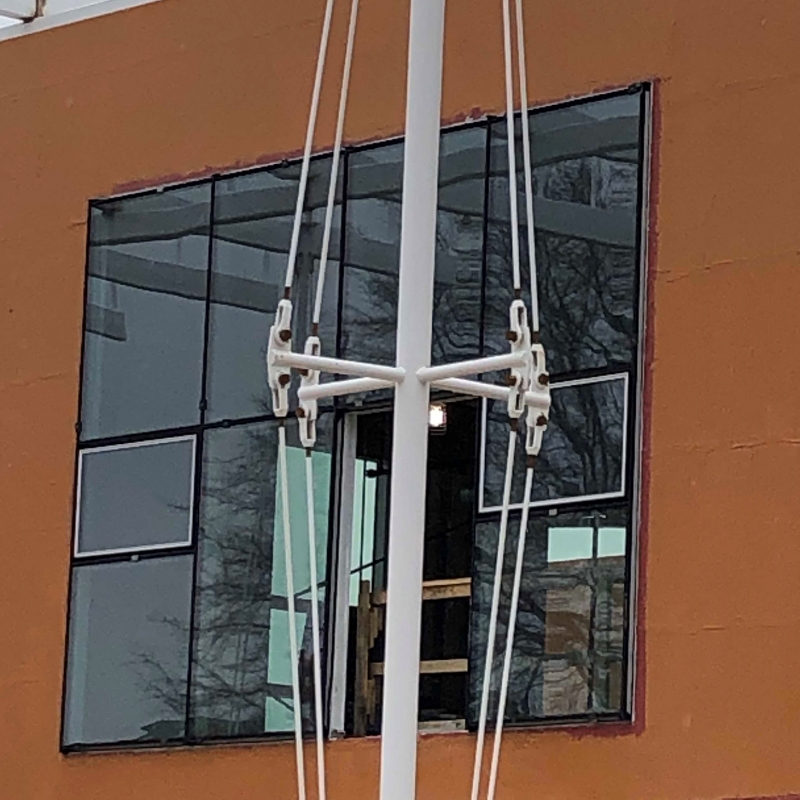
Figure 2. Column detail showing spars and tension rods
Solar Panels
The PV array comprises 913 solar modules a total capacity of 330 kW, occupying about 15,860 square feet of area forming a floating canopy above the building. The panels will tilt from the horizontal plane by 5 degrees to face south. This slight adjustment will increase solar exposure and improve drainage. These modules represent state-of-the-art monocrystalline technology, which offer a 22 percent efficiency rate – most solar panels have an efficiency rate of 15 to 18 percent – but offer a considerably reduced efficiency loss due to the advanced N-type substrate material used in their construction. As a result, The Kendeda Building’s PV modules should be capable of providing for building’s energy needs for over two decades.
Balance of System
PV modules make up an integral part of a system. But, just as an electric car consists of more than its electric motor, a PV system is composed of inverters, conductors, conduit, disconnects, panelboards, and meters. Advanced string inverters segment the PV array into 10 sections and work together to convert the direct current (DC) power into grid-ready alternating current (AC) power. The components work together to create a system that complies with the National Electrical Code and ensures safe and efficient operation.
The PV system will connect to the campus grid and will feed any surplus energy back into the grid for use by other buildings on campus. The state of Georgia allows but does not require true net metering by utility companies – through which electricity is bought and sold back at a set rate. So in this case, electrical energy not used by The Kendeda Building will be consumed by other campus buildings instead of being pushed to the larger electrical grid that connects to metro Atlanta.
Energy storage is becoming an increasingly important concern as the percentage of decentralized renewable energy generation increases on the electric grid, and an energy storage system (ESS) is also featured in The Kendeda Building. A moderate-sized ESS will provide power for some lighting and control systems throughout the building in the case of interruptions in grid power, allowing the building to still function in a limited capacity and enhancing passive survivability.
The PV system’s initial cost (the cost of purchasing and installing the system), not including the ESS, is estimated at $2.50/watt, which represents a slight premium because of the selection of a high efficiency module.
Design for Today; Design for Tomorrow
A key imperative for a Living Building Challenge-certified building is to be net positive by more than 5 percent. For The Kendeda Building, simulations predict a yearly consumption of 328 megawatt hour AC [MWh(ac)] per year. PV yield analysis simulation comes in close to 450 MWh(ac) for the first year. Simulations by Sol Haroon, formerly of Georgia Tech’s High Performance Building Lab show that consumption will increase each year due to the building’s aging, while the energy produced will decrease each year due to the PV’s aging. However, the yield surplus created by the system design in year one ensures that the system will still perform at net positive even after 20 years of accumulation in energy consumption.
As the Niels Bohr quote so aptly explains, “Prediction is very difficult, especially if it’s about the future.” Simulation work coupled with risk analysis aims to capture the certainty of the net positive behavior year after year. Such an analysis paints a positive, indeed net positive, picture.
Funded through a private grant from The Kendeda Fund, The Kendeda Building for Innovative Sustainable Design at Georgia Tech is expected to become a Living Building Challenge 3.1 certified facility – the built environment's most rigorous and ambitious performance standard. The project’s design and build partners include architects Lord Aeck Sargent in collaboration with The Miller Hull Partnership, construction manager Skanska and design team consultants: Newcomb & Boyd, PAE Consulting Engineers, Uzun + Case, Biohabitats, Andropogon and Long Engineering.
Want to learn more? The team is leading site tours on Thursdays at 3 pm. Sign up here.
Comments
Exploring the notion of regenerative design - II
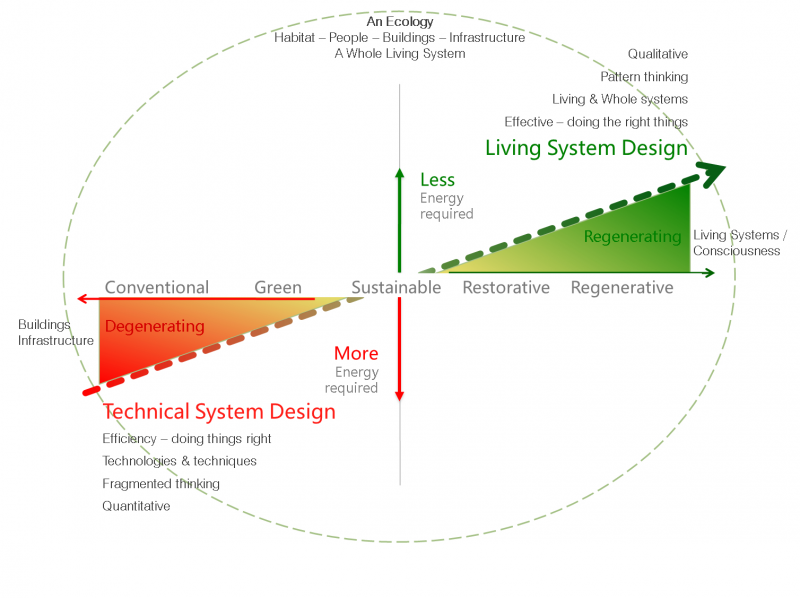
Image courtesy of Regenesis Group
In the first post on this topic last month, we tried to define ‘regenerative design’ in simple terms and identified its link to culture and psychology. The emphasis was on developing the required ‘state of mind’ first.
The Regenerative Design Summit, organized by U.S. Green Building Council (USGBC) Georgia with the support of The Kendeda Fund, was convened on October 12 at the Atlanta Botanical Garden’s Day Hall. The daylong summit started with an opening plenary, followed by in-depth panel discussions on various aspects of regenerative design, and ended with an interactive process workshop.
Here are some excerpts from the proceedings to give you a flavor for the day’s activities:
Plenary Session by Bill Reed: Working with potential (evolutionary health of nested living systems) is preferable to working with problems. In other words, harmonize, not compromise. Focusing on problems leads to a fragmented approach whereas focusing on potential has the ability to dissolve problems. Enlarging the scope of seemingly unsolvable problems often shifts the perspective to potential.
Resource Stewardship Panel Discussion: Georgia Tech and The Kendeda Building for Innovative Sustainable Design are making great strides in developing campus-wide sustainability metrics and a net positive approach to energy and water, respectively. Embodied carbon is a harder sell than operational carbon because it is harder to see and to assign monetary value. Whole Building Lifecycle Assessment (LCA) can help to identify a project’s high impact areas. Carbon has time value, and with the pressing need to address climate change, early savings should gain higher priority over long-term savings. Embodied emissions from building materials and construction processes fall in the early savings category whereas operational emissions fall in the long-term savings category.
Biomimicry, Biophilia, and Ecotone Panel Discussion: It is possible to have it all and, at the same time, halve it all by using nature’s efficiency as an inspiration. Nature also has a calming and uplifting effect that puts one in the present moment. Types of diversity to consider are bio, material, and experiential. When you are dealing with a project with too much focus on monetary costs, take the client for a walk in the woods to shift perspective.
Quantification and Metrics Panel Discussion: When it comes to building materials, from a manufacturer’s perspective, action on climate change (carbon footprint) can be the post-sustainability frontier. Energy poverty and energy burden are real problems; there are people who have to skip meals or miss refilling prescriptions in order to pay their utility bills. A strategic combination of energy efficiency and renewable energy has the potential to ease energy burden for the vulnerable.
Interactive Process Workshop: How does a project in Atlanta add value to the larger “whole” (community, city, ecoregion, life-shed, etc.) it resides in and how does the larger whole inform the development of the project? How does one define the bounds of the larger whole? The development of a purpose statement for a project can lead to surprising insights for its approach to regenerative design. Action is informed by strategy, which is, in turn, informed by beliefs and principles.
For me, one of the most interesting aspects was the incorporation of live audience polling to measure how the summit influenced the participants’ outlooks and perceptions. Precisely to this end, the audience poll included two questions:
- Rank perceived barriers to regenerative design (before the summit started)
- Things I will do right away to affect change (at the end of the summit)
Responses by audience were quite revealing, even when the options to rank or prioritize were embedded into the poll questions. Here are the findings.
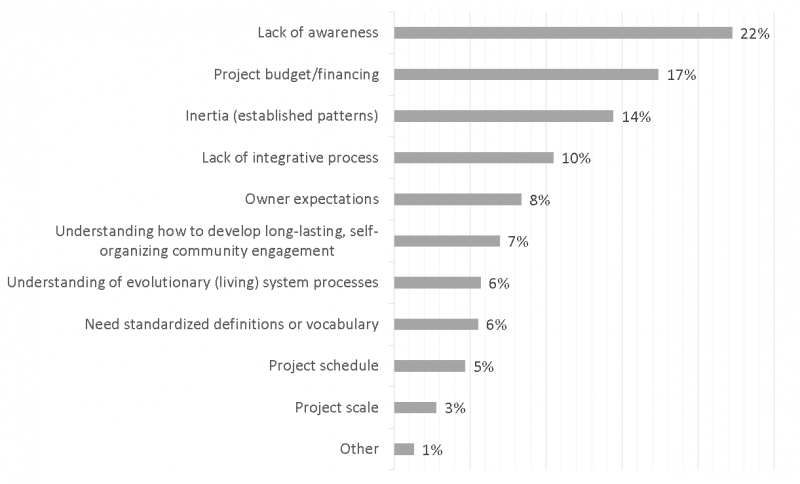
Figure 1. 38 respondents ranked perceived barriers to regenerative design (before summit). Data for the graphic is courtesy of USGBC GA.
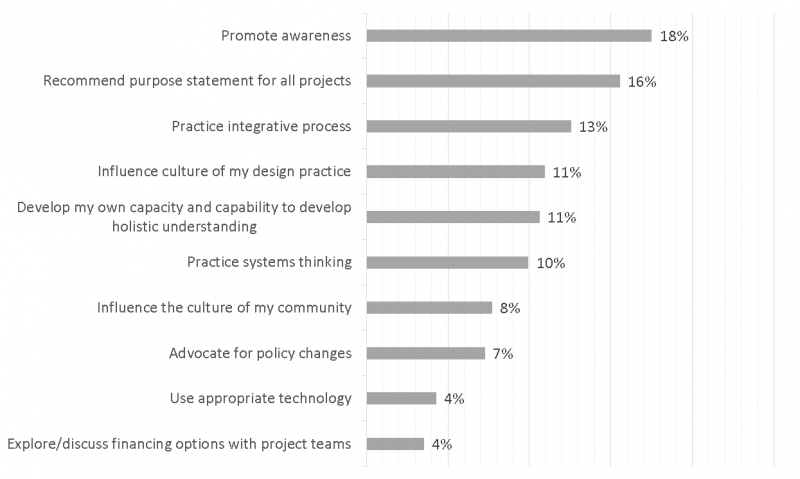
Figure 2. 31 respondents identified things they would do right away to affect change (after summit). Data for the graphic is courtesy of USGBC GA.
Lord Aeck Sargent appreciates the opportunity to be a part of the volunteer committee that helped USGBC GA organize the summit and gather participant feedback.
Comments
Exploring the notion of regenerative design
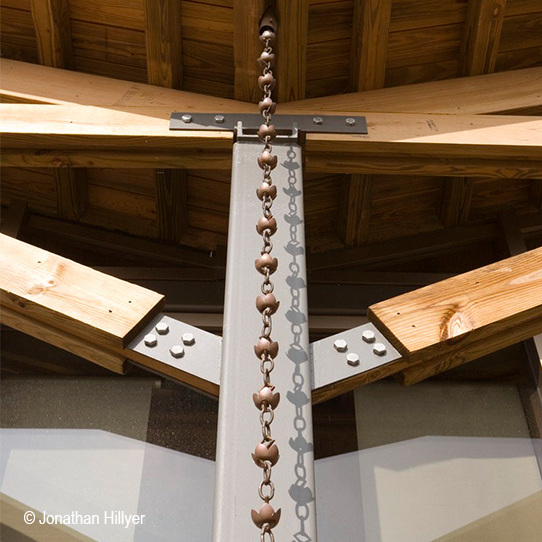
“What you’re doing is not important, what is important is the state of mind in which you are doing it.” – Constantin Brâncuși as quoted by Marina Abramović in a Guardian article on creativity.
It is easy to read descriptions of regenerative design and wonder if they could have been expressed in simpler, less confusing terms. The answer may very well be ‘no’ but the idea is definitely worth exploring.
Above all other possibilities, regenerative design asks of us to first develop a new state of mind; a state of mind that is not afraid to base strategies and action on a set of principles; a state of mind that seeks to explore the system or the context along with the element; a state of mind that highly values process as a means to an outcome; a state of mind that seeks to add value to the evolutionary health of the places we inhabit.
One thing that is easy to grasp is that regenerative design places life – human and other forms – at the center and seeks to promote it. Life thrives in the context of nested and complex ‘living systems’ whose interactions may not be easy to capture via graphics or metrics.
As an architecture professional, I have often wondered how it is possible for architects dealing with things at the building scale to practice regenerative design. According to Bill Reed, an architect with Regenesis Group, a building is an acupuncture point to influence the larger community and the ecological context around it. And in turn, the healthy nature of the larger community and ecosystem can inform the nature, processes and form of the project. In Reed’s vision, ecological design culminates in regenerative living systems, transcending fragmented and energy intensive approaches.
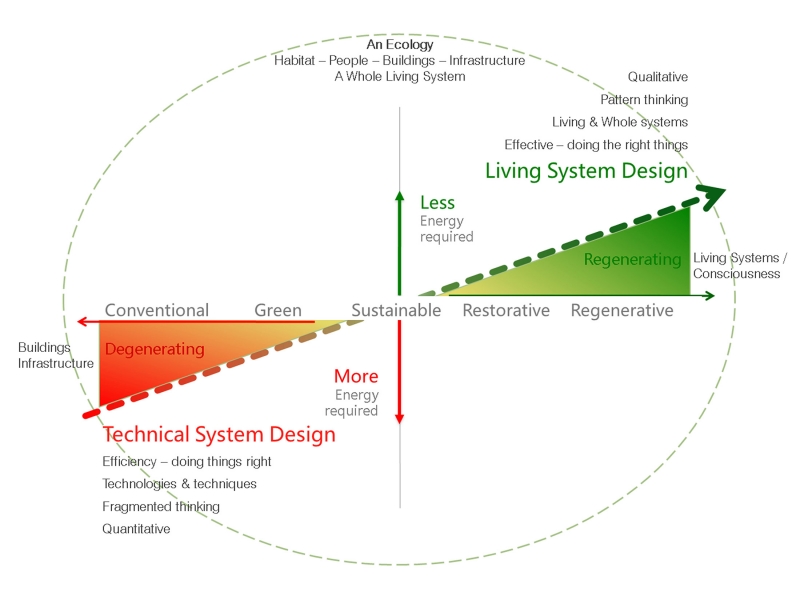
Figure 1. “Trajectory of Ecological Design” by Regenesis Group
Reed also believes that an integrative process, one that expands the scope of design and builds capacity among all stakeholders, is key to realizing the potential of regenerative design. This thinking is based on an understanding that the barriers to practicing regenerative design are primarily cultural and psychological, not technological.
Reed offers a simple framework for project teams to explore ‘purpose’ on their project. Define:
- Function: What will be transformed in the course of this project?
- Being: What new capability in ourselves, our team, and the larger life-shed will be developed?
- Will: What is the deep source of our motivation – the purpose of the purpose?
Lord Aeck Sargent, through a recent in-house design forum effort, has articulated seven ‘core values’ that inform the firm’s approach to design:
- Imaginative
- Context-driven
- Mindful
- Regenerative
- Enduring
- Poetic
- Holistic
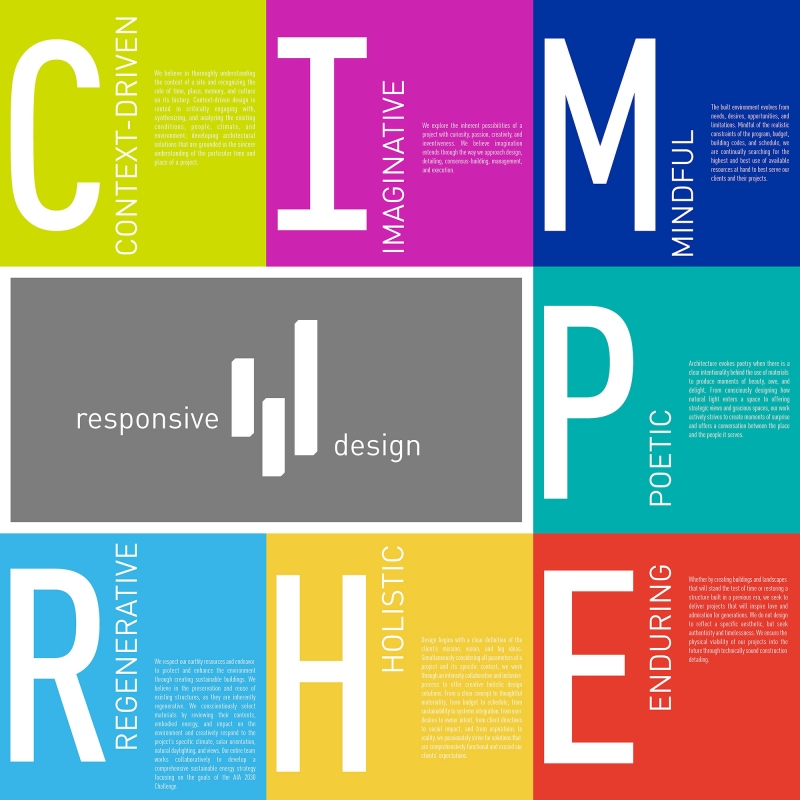
Figure 2. Lord Aeck Sargent's design core values
As we strive to put these core values to work on all projects, we are having to scale the same cultural and psychological barriers and ask questions similar to those that Reed puts forth in his framework for exploring purpose.
We have made considerable progress, thanks to the ongoing work on the Kendeda Building for Innovative Sustainable Design and the recent design forum and sustainability strategic planning efforts.
If you are in or around the Atlanta region and interested in learning more about Regenerative Design, there are two events coming up that might be of interest to you:
- USGBC GA’s Regenerative Design Summit on October 12, 2018
- ILFI’s Net Positive Atlanta: Subtropical Solutions on October 18, 2018
At the Regenerative Design Summit, Joshua Gassman of Lord Aeck Sargent will moderate a panel discussion, which will focus on the topics Biomimicry, Biophilic Design and Ecotone and feature specialists Jeannette Yen (Georgia Tech), Sonja Bochart (Shepley Bulfinch) and Jose Alminana (Andropogon) respectively.
At the Net Positive Atlanta event, Joshua will co-present a session titled, ‘Humid Climate Zero Energy: Keeping it Cool.’
We hope to see you at these events.
Comments
A Living Building Project Journey, Part-16
Construction Updates from the Site 2: Salvaged Materials
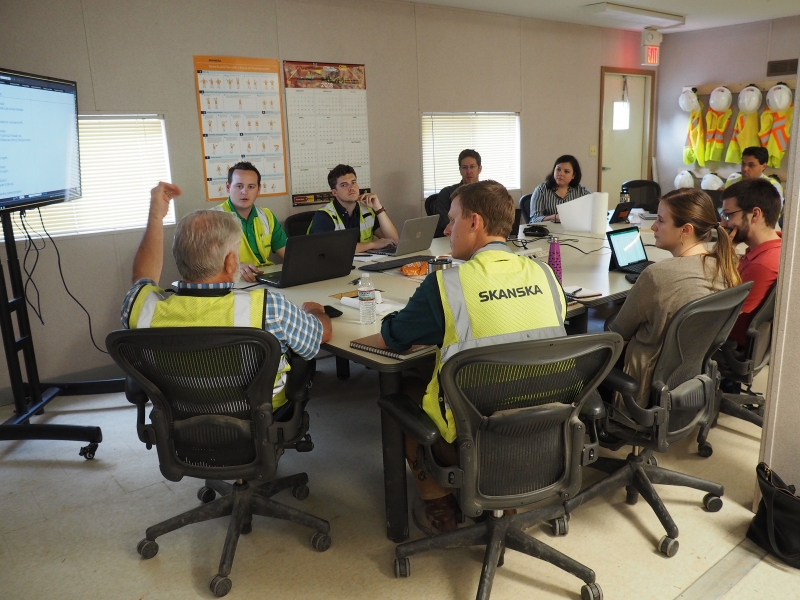
Using salvaged materials on a project requires careful planning and coordination in terms of designing around, identifying, procuring and storing such materials. Because this is not an industry standard practice yet, it can seem daunting to project teams already pressed for time and budget. When successfully executed, material reuse can demonstrate benefits in terms of waste diversion, embodied carbon and the actual cost of construction materials and products.
As one of the most rigorous proven performance frameworks for buildings, the Living Building Challenge has many standards to be followed. One of these is the Net Positive Waste Imperative of the Living Building Challenge (LBC), which stipulates that ‘all projects must feature at least one salvaged material per 5,380 square feet of gross building area or be an adaptive reuse of an existing structure.’
For new construction, such as The Kendeda Building for Innovative Sustainable Design at Georgia Tech, this means that the project must use at least seven different salvaged materials. The project is currently on track to meet and exceed this requirement and is incorporating some innovative strategies. In this post, we share examples of salvaged materials being used in the project; where they were acquired; and how they are being employed.
The Kendeda Building for Innovative Sustainable Design will use the following salvaged materials:
- Nail-laminated decks
- Slate tile
- Granite curbs
- Joists
- Storm felled oak
Nail-Laminated Decks
The roof and floor decks of the project will contain nail-laminated panels that are a combination of 2x6s and 2x4s. The 2x6s are structural while the 2x4s are spacers. All the 2x6s are new and come with Forest Stewardship Council (FSC) chain of custody documentation, which shows the path taken by products from the forest to the point of the product’s sale with an FSC claim and/or it is finished and FSC labeled, from a mill in Alabama.
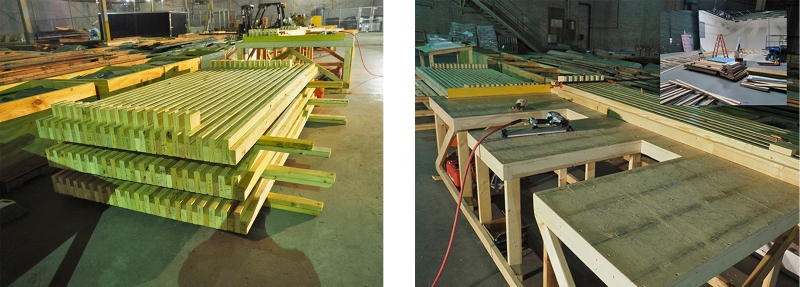
Figure 1. (left) Nail-laminated roof and floor decks are custom-manufactured at the storage warehouse. Decks are sized based on the span. The most typical size of a single deck is 6’x10’-6”. Figure 2. (right) Workstation where the nail-laminated decks are being assembled. Inset shows the movie set source of the material.
Approximately 25% of the 2x4s are salvaged wood from dismantled movie sets and are exempt from FSC certification requirements. The construction manager, Skanska, is self-performing the assembly of these nail-laminated decks in a warehouse near the project site. For more detail on this aspect, read The Kendeda Fund Living Building Chronicle’s post from December 2017.
Slate Tile
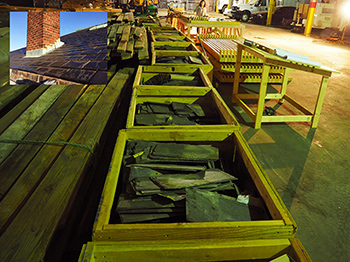
The roof of the Alumni Association building at Georgia Tech was replaced after more than 70 years of use. The slate tiles are still in good shape. At the time of demolition, bins were made to fit the lifts used by the construction crew to access the roof. Having bins close at hand made saving the tiles easier for the crew. The Skanska team will cut the slate to size and use it to tile the walls in the bathrooms and shower rooms.
Granite Curbs
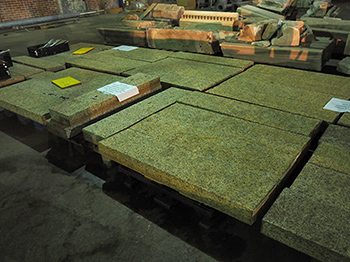
The Georgia Archives Building was recently razed through a controlled implosion to make way for the new Georgia State Supreme Court. The demolition schedule allowed an opportunity to salvage and collect materials. These Stone Mountain granite curbs have found a home and will be used as the curb that surrounds the constructed wetland – a part of the treatment system for the greywater.
Joists
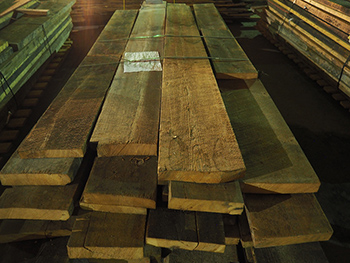
Tech Tower on the Georgia Tech campus, which began construction in 1887, is one of two original buildings that made up the then Georgia School of Technology. In 2016, it went through a full interior renovation that included removing the exterior metal fire stairs to be replaced with an interior fire stair. As part of this process, four floors with original heart pine joists were removed and saved. They will be used as the stair treads at The Kendeda Building.
Storm-Felled Oak
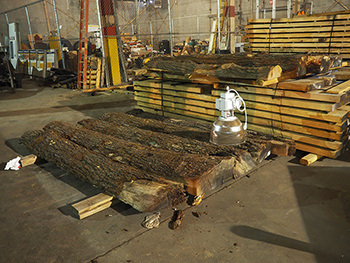
Georgia Tech implemented a storm-fallen tree recovery plan to collect trees. The team reviewed the inventory and milled white oak, black oak and water oak for The Kendeda Building. The wood, which has been air-dryed for one year, will be kiln-dryed and processed for use as live-edge slab counter tops and benches.
Lunch Tables
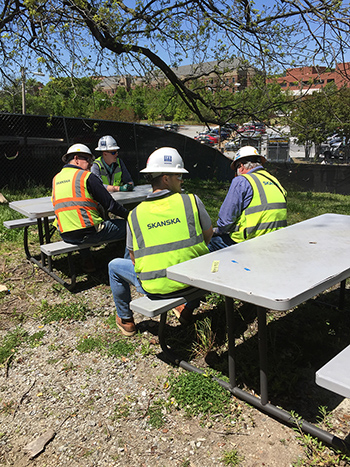
Construction lunch tables, salvaged from a project for Children’s Healthcare of Atlanta, are located adjacent to the construction trailer. While this isn’t one of the seven salvaged materials, the repurposing of these tables certainly fits the spirit of the team effort to maximize salvaged materials use and reduce waste.
The project team has been working with the Lifecycle Building Center in Atlanta, which has been facilitating the use of salvaged materials on this project. This community-based organization has a warehouse that directly assists the general public by identifying and implementing best practice green building-related concepts. Since 2011 it has diverted more than 3.8 million pounds of building materials from landfills and saved the community more than $2.4 million through deep discounts on material purchases, avoided disposal costs and the donation of free building materials to over 155 nonprofit organizations, community groups and faith-based organizations.
Funded through a private grant from The Kendeda Fund, The Kendeda Building for Innovative Sustainable Design at Georgia Tech is expected to become a Living Building Challenge 3.1 certified facility – the built environment's most rigorous and ambitious performance standard. The project’s design and build partners include architects Lord Aeck Sargent in collaboration with The Miller Hull Partnership, construction manager Skanska and design team consultants: Newcomb & Boyd, PAE Consulting Engineers, Uzun + Case, Biohabitats, Andropogon and Long Engineering.
Want to learn more? The team is leading site tours on Thursdays at 3 pm. Sign up here.
Comments
A Living Building Project Journey, Part-15
Construction Updates from the Site 1
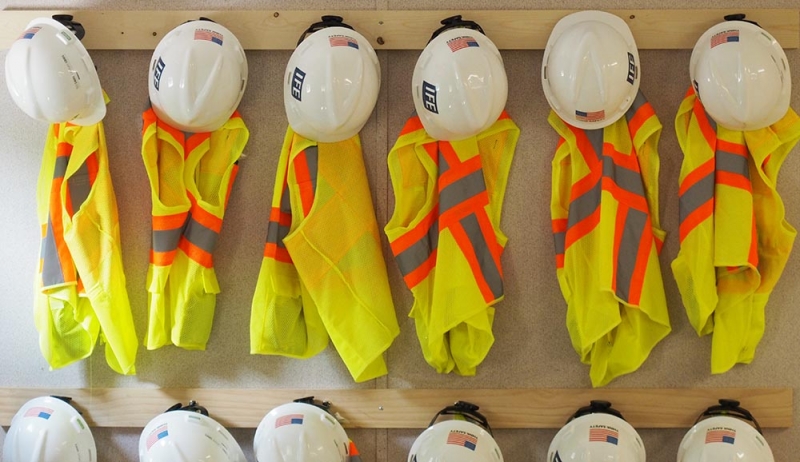
Live Camera
Since active construction began in March 2018, a publicly-accessible live camera has taken a picture of the Kendeda Building for Innovative Sustainable Design construction site every few minutes, accessible at https://app.oxblue.com/open/skanska/livingbldggatech
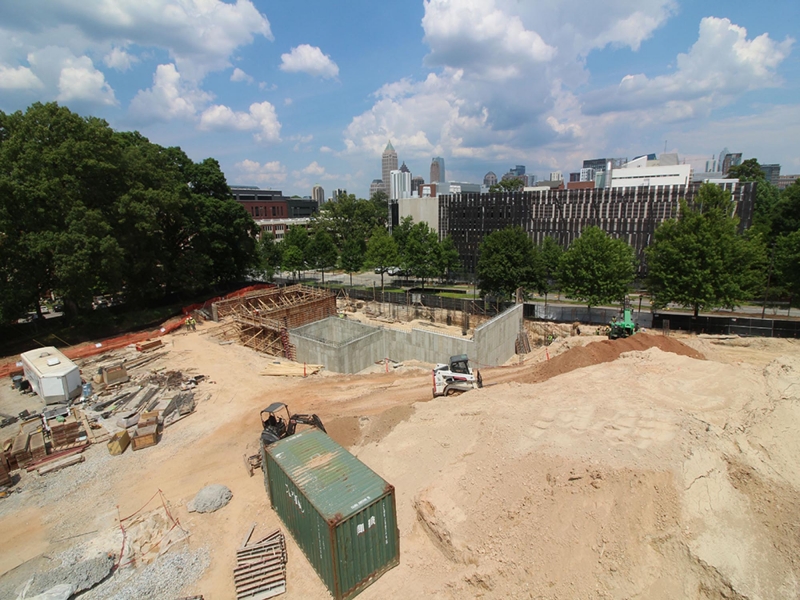
Figure 1. An image of the site from the camera at 3:05 pm on May 10, 2018.
Users can follow the progress using features such as a visual timeline, splitting or overlaying images from different dates and times, etc. The camera has a built-in weather sensor to track temperature, cloud cover, heat index, visibility, pressure, wind speed, dew point, and relative humidity. Weather data measured so far is available for download in a spreadsheet format; this can be useful for researchers because the microclimate of a specific location sometimes varies from common sources of weather data, such as airports.
Net Positive Waste
The Net Positive Waste Imperative under the Materials Petal of the Living Building Challenge (LBC) provides guidance to the project team on reducing or eliminating the production of waste during design, construction, operation, and end-of-life phases of the project. There are two components to this Imperative:
- Use of at least one salvaged material per 5382 ft² of the project (seven on this project)
- Creation and execution of a ‘Material Conservation Management Plan’ that explains how the project optimizes materials during all the phases mentioned above.
The project team developed a Material Conservation Management Plan during the design phases that is now being implemented for the construction portion.
With respect to the waste reduction or elimination efforts, the segregated material types, and their percentages by weight, being diverted from landfill during construction can be summarized as:
- Metal – 99%
- Paper and Cardboard – 99%
- Soil and biomass – 100%
- Rigid foam, carpet, and insulation – 95%
- All others (combined weight average) – 90%
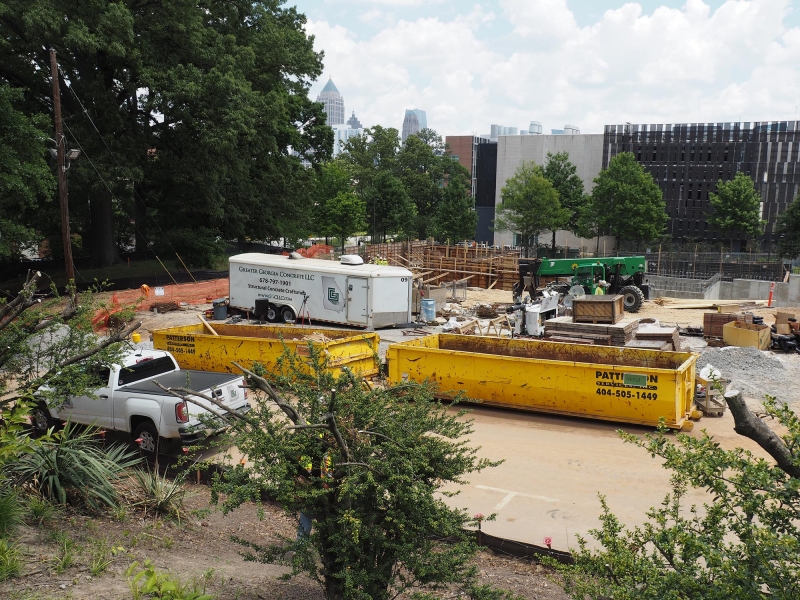
Figure 2. Construction waste dumpsters on site for wood (left) and metal (right). The third dumpster for collecting plastic bottles, paper and cardboard is outside the view of this photograph to the right.
Approximately 443 tons of asphalt has been recycled to date. All salvageable material is either being incorporated into the project in a new manner or being donated to the local Lifecycle Building Center for their retail salvage operation.
Additionally, the Skanska team is compiling a list of expected waste streams from each trade involved in the construction project and is working to identify key materials that will need to be 100 percent recycled to achieve the 90 percent recycle figure for the “All Others” target. The 90 percent goal is complicated by the fact that there are two local co-mingling options that will report a recycling rate of approximately 70 percent at a portfolio level without providing a breakdown specific to our project. One of the key identified materials across multiple future trades are plastics. The next recycling container will be all plastics, and the team has identified a general plastics recycling center to receive those materials.
There is also a small amount of compost scraps from lunch and things like coffee grounds. The Skanska team visited Georgia Tech’s West Campus Village Dining Commons, which has agreed to allow the small amount of scraps from the project to be deposited in their existing compost bins.
Material Vetting for Red List Ingredients During Construction
Compliance with the Materials Red List requirements (vetting and advocacy pertaining to the 22 red-listed materials/chemicals) has carried over from the design phases into the construction phase. We discussed the project team’s efforts to design around these Red Listed chemicals in our blog post from November 2016.
During construction, the Construction Management team is checking all materials supplied to the site for the following three questions:
- Has this material/product been fully vetted for Red List compliance?
- Has this material/product been submitted and approved for specification compliance? (the specifications provide guidance on a recommended process to address substitution requests from subcontractors, etc.)
- Have we confirmed that this material/product does not contain any other items required for installation that were not previously identified or reviewed for Red List compliance?
The answer would have to be ‘yes’ or ‘n/a’ for all three questions for the material or product to pass this filter. Though we try to identify all materials in advance, the team is finding materials and addressing them to the Red List concerns. In two instances relevant to the third question above, an unforeseen component required further vetting:
- We established a Red List compliance for a water stop (that goes between foundation footings and walls or between floor slabs and walls), but overlooked the company’s primer, which is applied prior to the water stop. We set the material aside in storage and began to quickly address the process of reviewing the product. After a full day of team effort, we had the due diligence we needed to submit a compliance effort for the primer. Because ingredient disclosure in the Safety Data Sheets amounted to less than 100%, we requested a letter from the supplier attesting that the product does not include materials on the Red List and stating the percentage of any proprietary ingredient being withheld.
- Similarly, in reviewing the underground chilled water pipe, we uncovered a mastic coating that is a common product associated with the pipe insulation. This product had little or no disclosure and the due diligence effort of requesting information from the manufacturer and reviewing it could have become an extended one. Fortunately, our project system does not require this mastic, so we eliminated the mastic from the piping installation.
Erosion and Sediment Control
Erosion and Sediment Control is not an LBC requirement but is a local regulation and an environmentally responsible construction practice. This project uses several best management practices (BMPs) to help reduce erosion of the site’s topsoil and sedimentation of streams and buffers from site runoff.
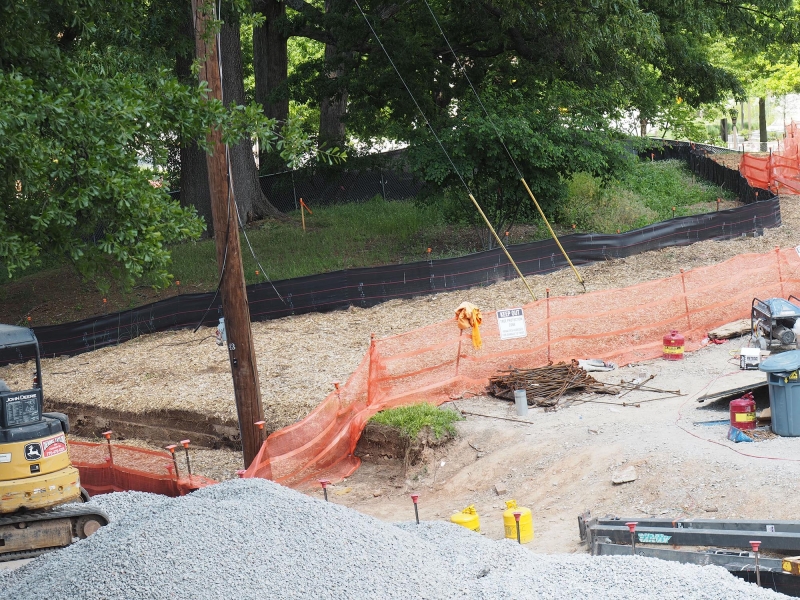
Figure 3. The black silt fence to the back of the picture is supported by metal stakes. In front of the fence is mulch generated from magnolia trees that were removed from the site prior to the beginning of construction.
FSC Wood on The Site
All non-salvaged wood used on the project is subject to Forest Stewardship Council (FSC) certification requirements, per the Responsible Industry imperative of LBC’s Material Petal.
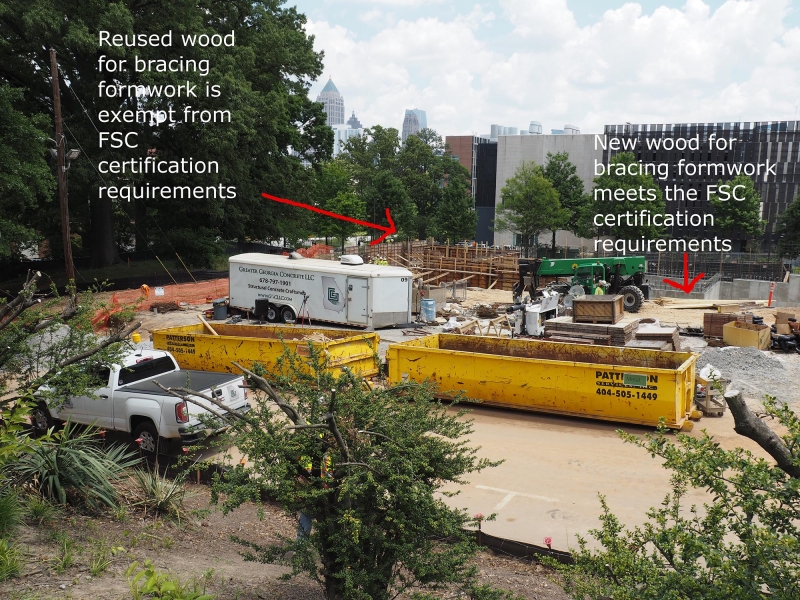
Figure 4. Salvaged wood vs. FSC wood on site
Funded through a private grant from The Kendeda Fund, The Kendeda Building for Innovative Sustainable Design at Georgia Tech is expected to become a Living Building Challenge 3.1 certified facility – the built environment's most rigorous and ambitious performance standard. The project’s design and build partners include architects Lord Aeck Sargent in collaboration with The Miller Hull Partnership, construction manager Skanska and design team consultants: Newcomb & Boyd, PAE Consulting Engineers, Uzun + Case, Biohabitats, Andropogon and Long Engineering.
Want to learn more? The team is leading site tours on Thursdays at 3 pm. Sign up here.
Comments
LAS at Living Future
Members of our sustainable team will be in attendence and among presenters – we hope to see you there.
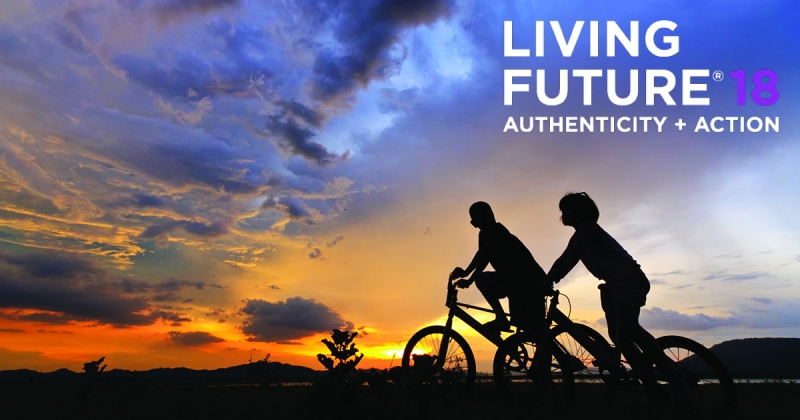
The 12th annual Living Future unConference, the leading event for regenerative design, will be held next month in Portland. Hosted by the International Living Futures Institute, the organization behind the Living Building Challenge, the unConference provides a forum for leading minds in the green building movement to make strides for a healthy future for all. This year’s theme is “Authenticity & Action” and Lord Aeck Sargent’s sustainability leaders Jim Nicolow, FAIA, LEED Fellow, and Joshua Gassman, RA, LEED AP BD+C are excited to once again be invited to present.
Director of Sustainability Jim Nicolow will be presenting in a session titled, “Taking Action to Advance Social Equity in the Workplace” (Conference Track: Organizational Best Practices, May 3rd at 3:45 p.m., Oregon Convention Center Room B117-B119).
Businesses are embracing the need for improvements to existing equity, diversity and inclusion programs. The challenge has been to advance these important issues in a robust, systematic and holistic fashion. Corporate social responsibility frameworks such as B Corp and Global Reporting Initiative (GRI) allow for a snapshot in time assessment of environmental and social performance but do not offer a clear roadmap for continuous improvement across a wide range of equity indicators. Leading businesses in the design, engineering, consulting, contracting and manufacturing sectors have adopted the JUST Program as a management tool to improve diversity at all levels of the organization, build a more inclusive corporate culture and enhance employee engagement efforts.
Jim will join a panel discussion with representatives from Bioconstrucción y Energía Alternativa, BurroHappold Engineering, BCCI Construction, and the Integral Group to discuss specific actions they have taken to advance social equity polices, programs and practices in their organizations. Lord Aeck Sargent earned our inaugural JUST label in February 2017, among the first 20 architecture firms in the world to do so, and we’re excited about the opportunity to share our process and learn from others as we prepare for our biannual renewal of the label in 2019.
Sustainable Design Director Joshua Gassman will be presenting in a session titled, “Repurposing Salvaged Materials” (Conference Track: Healthy Materials, May 4th at 1:30 p.m., Oregon Convention Center Room A107-A109).
Understanding the need to reduce the impact on our waste stream from construction demolition, the session will explore the supply chain of waste, opportunities and challenges to salvaging materials, and value gained from repurposed materials. Presented in collaboration with our construction partner on the Kendeda Building for Innovative Sustainable Design at Georgia Tech, Jimmy Mitchel from Skanska USA Building, the goals of this session are to demonstrate authentic examples of repurposed materials and to have a discussion around the challenges of creating a reuse economy, energized with a mixture of perspectives from the design, construction, artist, NGO, and owner communities.
Joshua will also participate in the "Human Health and Materials Summit" (May 2nd from 1 to 5 p.m., Oregon Convention Center Room C123-C124). The leadership summit, facilitated by Nadav Malin, President and CEO of Building Green, will go beyond typical conversations on health in the built environment to explore material health at multiple scales. The goal is to get everyone in the room to work together toward transforming the materials economy together.
We hope you can join us in Portland next month for Living Future 18. But if not, look for a subsequent post afterward where Jim and Joshua share their experiences and takeaways from this year’s conference.
Comments
A Living Building Project Journey, Part-14
The Story of a Window on a Deep Green Building
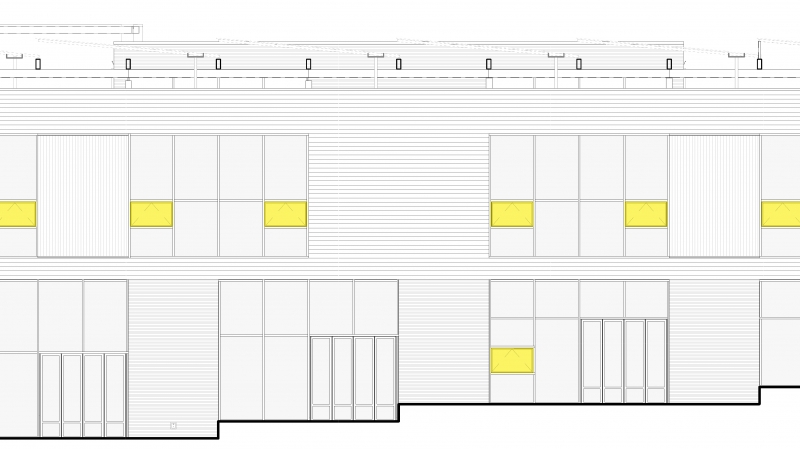
The word “window” originates from the Old Norse ‘vindauga,’ literally meaning an eye for wind. Modern windows serve many purposes; if operable, they connect us to the outdoors in the Old Norse meaning, while keeping us comfortable and secure. While their contribution to energy performance often gets the most scrutiny from architects and engineers, their impact on indoor environmental quality (ventilation, daylight, views, thermal comfort, occupant control, etc.) often has a much more tangible impact on a building’s occupants.
In a piece on how to avoid getting sick when you travel that aired on last month’s Marketplace Morning Report, frequent traveler Mark Orlowski of the Sustainable Endowments Institute specifically highlights the importance of operable windows:
“For me, first of all, air quality is key. I really try to avoid staying at any hotels that don’t have windows that open. Unfortunately many new hotels are being built where, literally, you can’t open the window.”
You can listen to the full story here (beginning at 4:12) for more interesting details but you get the point: if it doesn’t allow the wind to enter, is it even a window?
Furthermore, a recent study (COGfx) by Harvard T.H. Chan School of Public Health found that, lower volatile organic compound (VOC) levels coupled with enhanced ventilation, led to significant improvement in cognitive function of occupants in green buildings (where enhanced ventilation is defined as VOC levels below 50 μg/m3 and ventilation rates of at least 40 cfm outdoor air per person). Operable windows can provide the most direct, occupant-controlled means for increasing ventilation rates.
Recognizing the importance of windows, the Living Building Challenge’s (LBC) ‘Civilized Environment’ imperative under the ‘Health + Happiness’ Petal prescribes minimum requirements for windows, including:
- Each space needs at least one window wall with at least 10% glazing (At the building level, the Kendeda Building’s window-to-tall ratio (WWR) is currently tracking at 40.7%. WWR is the ratio of the area of all the windows to the gross area of all the walls including windows).
- All staffed workstations to be located within 30 feet of an operable window.
Operable windows must be strategically placed throughout a building’s facades to meet LBC’s intent and requirements.
The idea of designing for operable windows itself may seem straightforward, but the details can quickly get complicated when addressing who controls what and when. Several priorities, such as connection to the outside, energy performance, glare control, pollen filtration, avoiding condensation, maintaining building security, providing daylight illumination, and the like can compete with or clash with one another and the importance of finding an optimal solution that balances these and other considerations is a critical part of green building design. Let us delve deeper into some such challenges encountered on the Kendeda Building for Innovative Sustainable Design.
Natural ventilation vs. forces of nature
Atlanta set a record high pollen count of 9,369 particles of pollen per cubic meter of air in March of 2012 (1,000 or more is considered ‘very high’). An April 2017 study by the project’s mechanical engineers showed that without any pollen filtration, natural ventilation potential existed for a meager 300 hours per year. The addition of pollen filtration, which was carefully investigated but ultimately not incorporated, increased the natural ventilation potential to 1,000 hours per year. This analysis is addressed in more detail in a mid-2017 article for High Performing Buildings magazine.
Given such limited potential, indoor environmental quality trumps energy savings as a primary rationale for including operable windows on this project.
Automated window operability vs. user control
Several operational modes were defined for the automated operation of the building’s operable windows.
Occupied mode: By default, on this project, window operation is automated based on weather conditions reported by a local weather station. In cooling mode, when outside air temperature is lower than the cooling set point by two or more degrees (an adjustable setting), and the pollen count is below an acceptable threshold, operable windows will automatically open. If either temperature or pollen count become unfavorable, the windows will automatically close. A “manual” override by an occupant is allowed, and lasts for a period of 90 minutes (an adjustable setting) before the operable windows revert back to the automated mode. This override applies both to an automatically opened window being manually shut, or an automatically closed window being manually opened.
Unoccupied and Morning Warm Up modes: All automatic windows remain closed.
Night flush mode: Diurnal swings can cause lower outside air temperatures in the night, compared to the daytime temperatures. When such favorable diurnal swings do occur, which may not be every day, it is possible to use that free outside cooling to condition the building during unoccupied setback hours. For example, let us say that the outside air is at 60° F and interior setback requirement is for 84° F. Say the interior is at 86° F and needs to be cooled down to 84° F, a controlled quantity of the outside air can provide the free cooling without the use of air conditioning. This is how the process is designed to work with The Kendeda Building: during cooling seasons, if outside air temperature in the next 24 hours (an adjustable setting) is predicted to exceed 75° F (an adjustable setting), and the internal temperature is greater than the night flush setpoint, all operable windows will be automatically opened and the mechanical ventilation (HVAC) deactivated (this upward air temperature criteria prevents usage of colder outside air that has potential for unwanted condensation). When outside conditions become unfavorable, such as high humidity causing the potential for condensation or forecast of wider temperature swings, all operable windows will automatically close.
Daylight potential vs. bird collision deterrence
Later in the design phases, bird collision deterrence became a priority for the project. In staying within Audubon Society’s recommended maximum dimension of 2-inches by 4-inches for any glazing pattern to prevent bird strikes, a 20% silk screen frit pattern of dots on the center pane of the triple glazed windows was investigated. This brought the visible light transmittance (VLT) of a typical window unit down from 48% to 40%, still decent for a triple pane glazing with the solar control requirements being considered.
We conducted daylight simulations to test the impact of the chosen frit pattern on the workplane daylight performance of a typical class lab space, assessing both a ‘single point in time’ during a year and Spatial Daylight Autonomy (sDA) that covers the entire year.
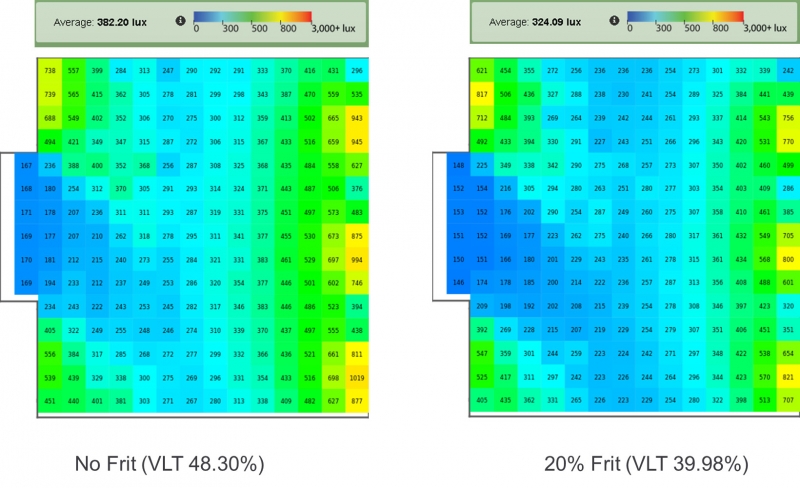
Figure 1. On March 21 at noon, under clear sky conditions, the frit pattern reduced average workplane illuminance from 35 footcandles to 30 footcandles.
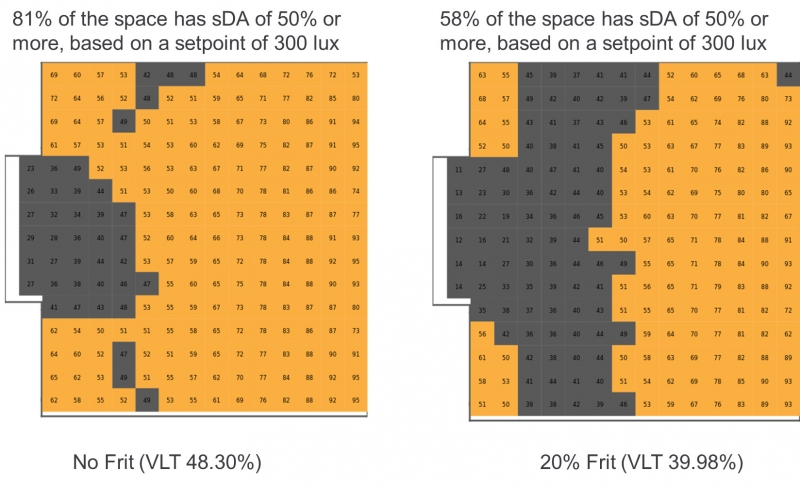
Figure 2. The silk screen pattern reduced the workplane’s sDA from 81% to 58%.
Results showed that the frit pattern lowered the daylight performance from “excellent” to “very good,” but this is a great tradeoff to improve bird protection while reducing daylight performance by a small amount. Informed by this study, bird collision deterrence is now being considered only in select portions of the project where the risk for bird collisions is anticipated to be the highest.
Views vs. solar control
Reduction of cooling load through control of solar radiation before it hits the windows is a crucial strategy for cost-effectively achieving net positive energy in a hot, humid climate (the LBC requires production of 5% more energy than consumed on an annual basis). The porch does this passively for most of the west façade (see post titled part-12 from October 2017). The PV canopy overhang to the south has been designed to offer similar passive protection. Windows on the east and west facades, which do not benefit from passive protection by the building structure, will employ motorized, exterior automated blinds. These blinds are designed to deploy when the following three conditions are satisfied:
- The floor is in full cooling mode
- The space temperature setpoint is not satisfied
- The outside radiation sensor senses solar radiation of more than 800 Watts/square-foot (an adjustable setting)
A wall switch for manual override allows occupants to retract deployed blinds or deploy retracted blinds. The manual override in either case will be programmed for 90 minutes (an adjustable setting).
As this discussion illustrates, windows serve many roles in high performing buildings. Careful design and analysis is required in order to balance these often competing roles and optimize both building performance and occupant experience.
Thanks to Whitney Ashley of Lord Aeck Sargent for Graphics Assistance.
Funded through a private grant from The Kendeda Fund, The Kendeda Building for Innovative Sustainable Design at Georgia Tech is expected to become a Living Building Challenge 3.1 certified facility – the built environment's most rigorous and ambitious performance standard. The project’s design and build partners include architects Lord Aeck Sargent in collaboration with The Miller Hull Partnership, construction manager Skanska and design team consultants: Newcomb & Boyd, PAE Consulting Engineers, Uzun + Case, Biohabitats, Andropogon and Long Engineering.
Comments
domestiCITY [an affordable atlanta] Competition
LAS team one of two top finalists selected for Phase II of the City of Atlanta’s First Affordable Housing Design Competition
![domestiCITY [an affordable atlanta] Competition](/assets/images/Charette.jpg)
LAS Selected As Competition Finalists
Over the course of several weeks at the end of 2017, a multidisciplinary design team from Lord Aeck Sargent’s Atlanta office, with help from local experts in market analysis and affordable housing development, submitted for the City of Atlanta’s first ever affordable housing design competition: domestiCITY.
Sponsored by the City of Atlanta Department of City Planning, Enterprise Community Partners and Assist Community Design Center, the domestiCITY competition is structured as “a two-phase design competition that will explore best practices and innovative strategies for the planning, design, construction and operation of affordable and sustainable developments in increasingly urbanized areas.” The competition site consists of 7.1 acres of mostly developed land: Santa Fe Villas with fully-occupied supportive housing and the abandoned Town & Country Courts.
Phase I of the competition saw a flurry of interest with 189 registrants across 15 countries represented. Ultimately, 20 proposals were submitted and considered by the December 2017 deadline. In early January 2018, an independent jury panel of design leaders, affordable housing experts and community representatives selected six teams to receive a $20,000 cash prize. Two of these teams would receive an additional $30,000 and the opportunity to further develop their program, design and financial plan in Phase II. Proposals were judged across four primary categories: architectural innovation, architectural programming, economic feasibility and project replicability.
The top two finalists selected by the competition jury to proceed onto Phase II are:
- Utile (Boston)
- Lord Aeck Sargent (Atlanta)
Among the other teams recognized for their submissions are: Sadyr Khabukhayev (Kazakhstan) “Architectural Innovation” Award, David Baker Architects (San Francisco), Siyi He & Yixin Ren (Rhode Island School of Design) and MPN Partners (London/Vietnam).
“The finalists selected are a representation of just how visionary affordable housing should be. DomestiCITY is the first of many initiatives to find new ways to design and build affordable housing on a broad scale in Atlanta but also across the country and internationally through pioneering designs. Affordable housing is a universal challenge and it’s time that we approach it with beautiful design in mind.” – Tim Keane, Commissioner of the Department of City Planning
Collaborative Process
Through multiple design charrettes, pin-ups and iterations informed by market realities, the LAS team put together a proposal for a unique housing solution that would be both innovative, in terms of architectural and green infrastructure strategies, and replicable, because of its modular approach and financial feasibility. This solution was largely driven by the use of Cross-Laminated Timber (CLT): an innovative, engineered timber product that has schedule time and cost savings, low embedded energy (renewable material) and the opportunity to create local jobs for Georgia’s strong lumber industry. The use of CLT as our primary construction technology helps to reduce the overall project budget, allowing us to create greater affordability for the supportive and workforce housing and job creation opportunities in our proposal.
Project Goals
As Atlanta finds itself at a crossroads of rethinking “affordable” housing and designing the future growth of the city, our proposal intends to achieve the following project goals:
- To create an inclusive, resilient and equitable mixed-use “village” that supports and empowers both its current and future residents through quality, mixed-income housing using “missing middle” typologies (LIVE);
- To build local partnerships and on-site job training as well as employment opportunities through the use of innovative new construction methods (WORK);
- To provide community amenities and services (THRIVE);
- To emphasize learning skills and educational opportunities (LEARN);
- To integrate sustainable systems and innovative building practices that can be replicated elsewhere (SUSTAIN);
- To respect and acknowledge the history of the site through the adaptive use of several historic structures as part of the site’s redevelopment.
“Visionary” Design
Our Phase I competition boards were submitted along with a 20-page narrative book. Click the image below to access boards.
Phase II of domestiCITY will entail a more detailed pro forma, further design development and proposed methodology for community outreach and engagement among other requirements. Phase II will conclude in March 2018 followed by a public exhibition to showcase all the recognized design submissions.
For more information on the competition or the submissions, visit the competition site.
Click here City of Atlanta’s official press release.
Comments
Video: Looking Back to Look Forward
The Kendeda Building For Innovative Sustainable Design – A Living Building
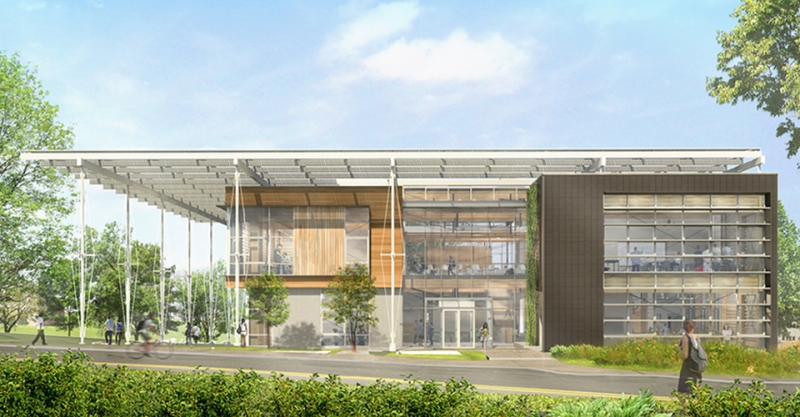
Georgia Tech created this video, which highlights comments from members of the project team as they share their perspectives of the project – from challenges to overcome and elements included to reach project goals, to design direction and abstract aspirations of the project’s place in the community, on campus and in construction history. If you’ve ever pondered over this project and wondered, “What were they thinking?,” this is your chance to find out.
The Kendeda Building For Innovative Sustainable Design – A Living Building
Comments
A Living Building Project Journey, Part-13
Looking Back at the Design Phases
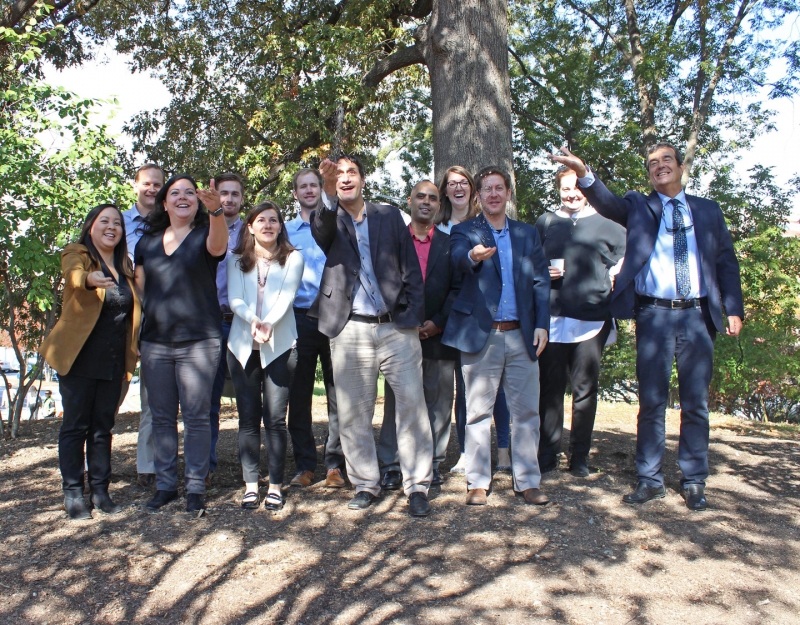
The 37,000-square-foot flexible sustainable research and education building recently completed design and the official construction launch was held on November 2, 2017. The project team is looking forward to the ramping up of construction activities in early 2018, with substantial completion planned for 2019.
Reconciling the building’s program, budget, and requirements of the Living Building Challenge certification has been no easy task. As we conclude the design phase, we have asked design team members representing several key disciplines (Architecture, MEP, Landscape, Water Systems and Construction Management) to look back at the design process and reflect upon the following two questions from their perspective:
- Which one factor has worked the most in the project’s favor?
- What was the biggest challenge that needed to be overcome?
Survey respondents were requested to keep their response to each question limited to two sentences. We hope the responses, tabulated below, provide a retrospective glimpse into the kinds of favorable factors and challenges that were perceived by the design team members on this unique project.
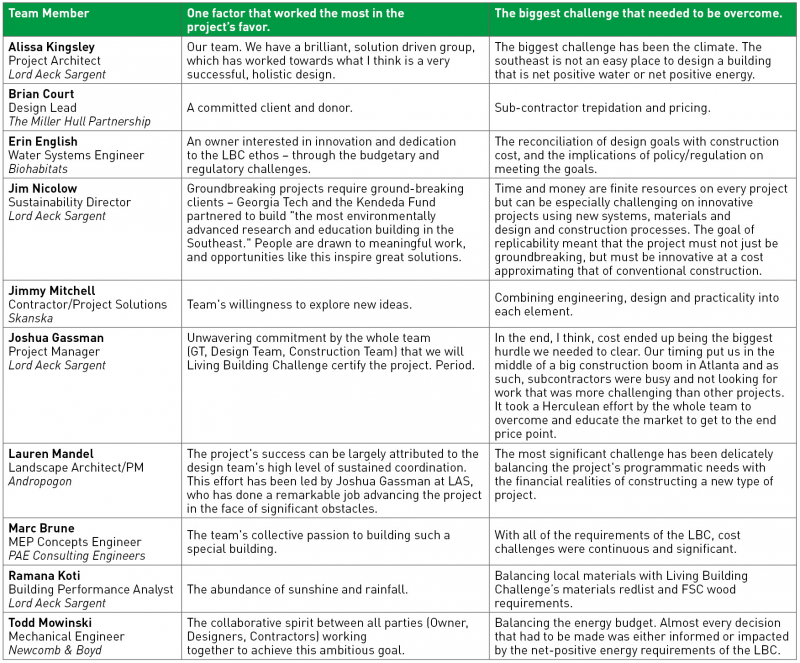
We will continue to report on the opportunities and challenges encountered throughout construction and the one-year post-occupancy performance period necessary for the Living Building Challenge certification. What has your experience been? Have any questions or comments for the design team? Do let us know in the comments section below.
Funded through a private grant from The Kendeda Fund, The Kendeda Building for Innovative Sustainable Design at Georgia Tech is expected to become a Living Building Challenge 3.1 certified facility – the built environment's most rigorous and ambitious performance standard. The project’s design and build partners include architects Lord Aeck Sargent in collaboration with The Miller Hull Partnership, construction manager Skanska and design team consultants: Newcomb & Boyd, PAE Consulting Engineers, Uzun + Case, Biohabitats, Andropogon and Long Engineering.
Comments
How to design sustainability into an architectural practice
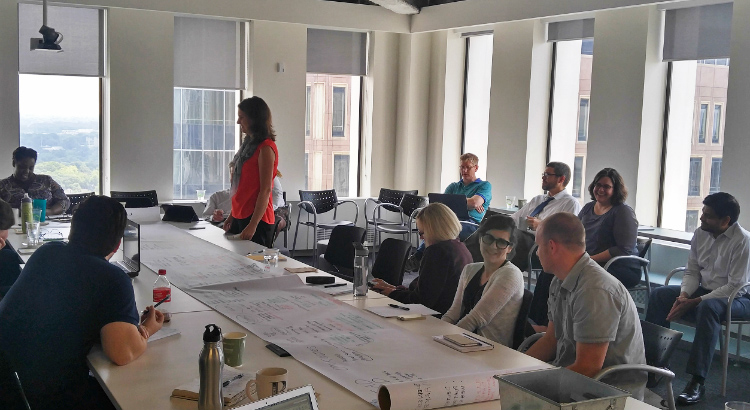
In most cases, it’s clients who drive the ambitions of deep-green buildings. But how can architectural firms lay the groundwork for more projects that push the boundaries of sustainability?
In an August article evocatively titled, “Why We Let Ourselves Do Mediocre Work,” BuildingGreen’s Tristan Roberts challenges architects who want to do exceptional, challenging sustainability work. Don’t wait for “the unicorn client,” he argues. In the absence of an owner with a strong vision of sustainability, the onus is on the architect (or the consultant) to define the possibilities.
Even when the design team takes the initiative to pursue more sustainable architecture, the focus is often narrowly on project delivery. Project delivery is no doubt a critical layer, but its capacity to bring about real change is limited when employed simply as a tide that can lift all boats. Technological silver bullets related to the practice of architecture (simulation software and such) are similarly limiting: While powerful, energy modeling alone won’t create a commitment to a net zero building.
Over the past 18 months, I’ve been a member of a sustainability strategic planning team at my firm, which has been working to develop and implement actions to more effectively and consistently deliver sustainable design across all offices and practice areas — even in the absence of a unicorn client!
We began our planning process with the help of a sustainability consultant, who conducted a “gap analysis” to identify shortcomings in organizational policies, procedures and culture that are hindering the desired outcomes. I outlined that effort in a blog post last year. Our soon-to-be-rolled-out 2018 Sustainability Strategic Plan is heavily informed by the gaps identified in that initial effort.
While the specific gaps and the resulting plan might be unique to our organization, “firm culture” seems to have universal relevance. It has the ability to influence virtually all aspects of operations. Let us look at some areas that have emerged as important ingredients of firm culture, with the end goal of developing a minimum sustainability standard for all projects.
Leadership vision and policy
If you pose questions to your firm’s leadership about revenue projections and market area growth, you’re bound to get concrete answers. Now, consider asking similarly strategic questions about sustainability:
- What values are guiding our firm’s approach to sustainability, especially when the client is not asking for it?
- What are our firm-level goals for sustainable design accomplishments in the next five or 10 years?
- How much of our project fee typically is or should be dedicated to building performance analysis?
- How does sustainability figure into our hiring and staff performance review processes?
- What is the criteria for our partnering with other architects and mechanical-electrical-plumbing consultants?
The answers, or lack thereof, will provide important insights. Although they shouldn’t be too difficult to answer, especially for firms that have signed on to the Architecture 2030 Challenge or the AIA 2030 Commitment, they tend to be.
Mid-level and junior staff, even those who consider themselves sustainability champions, look up to the leadership for an overarching vision that can motivate them and guide their actions. Crystalizing such guidance in writing is even better.
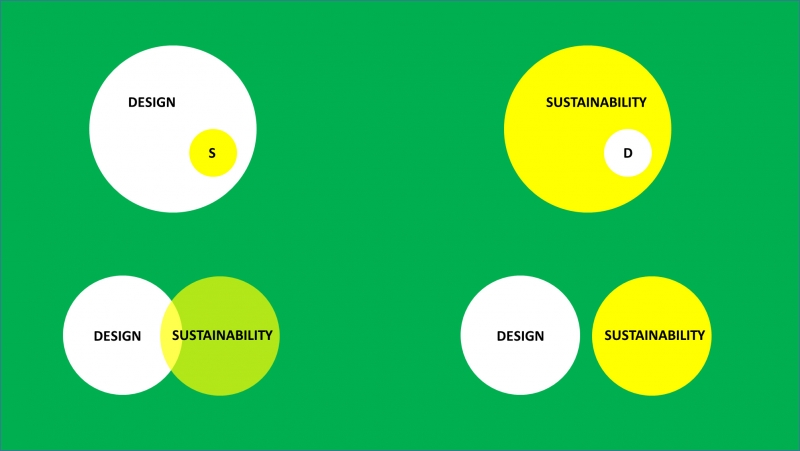
FIGURE 1. What’s the relationship between sustainability and design in your mind? Is sustainability a subset of design, or design a subset of sustainability? Are they overlapping equals? Or are they two disparate issues?
Project delivery roadmap
Projects move through predictable, standardized phases ensconced in industry-standard practices and contract law (programming, schematic design, design development, etc.). We applied the gap analysis to our standard project delivery approach to create a “project delivery roadmap” of the typical design delivery process, and to identify specific opportunities and milestones to better integrate sustainable design. That exercise raised interesting questions. Among them:
- What should a project’s sustainability goals be, and how should they be documented and tracked?
- What variables should be assessed at what phases of the project?
- How will different project team members be integrated?
- Who is accountable for the project’s overall sustainability success?
- How will decisions be tracked and communicated?
Transparency and accountability
Transparency is a tool for knowledge dissemination and improved accountability. It enables the sharing of performance data and of lessons learned across different project types and locations. To visualize this, consider the following:
- What sustainability variables tracked across projects should be common knowledge?
- Are there consequences, within reason, to not being transparent or being transparent but falling short?
- Is accountability centralized or distributed? How does it work in either case?
- How can transparency be leveraged to improve performance?
Active learning
Our education, formal and otherwise, is a foundation to our actions. Even then, investing in passive learning can yield little concrete action. If staff members of a firm had to make an elevator pitch to a client about the firm’s sustainability services, how similar or different would their various pitches be, and how effective?
Active learning seeks to engage the audience better by tailoring information to the audience’s interests, by making new information less intimidating and by incentivizing participation. A plan for active learning might include:
- Baseline vocabulary
- Need-based formal training
- Modes of engagement that would make internal learning less passive
- Reinforcing of a coherent firm culture to promote engagement in shared purpose
Conclusion
The goal of better focus on sustainability is to do better design. Achieving lasting change can be a challenge in any environment, let alone the often risk-averse field of architectural practice.
For me, innovation, insight from numbers, and a project sustainability story arc are powerful motivators that can be employed in combating inertia and creating a firm culture conducive to great, sustainable design. Here is some recent suggested reading from other online sources on this topic:
- How to Be a Sustainability Champion in Challenging Times (Rocky Mountain Institute)
- Why We Let Ourselves Do Mediocre Work (BuildingGreen)
- Know Thy Client: 9 Un-Green Strategies for Delivering Better Buildings (BuildingGreen)
What do you think? Are there issues you consider important that I left out? It would be great to hear your feedback in comments below.
This post originally appeared in the Living Building Chronicle.
Comments
A Living Building Project Journey, Part-12
Net Positive Energy 2: Building Performance Analysis
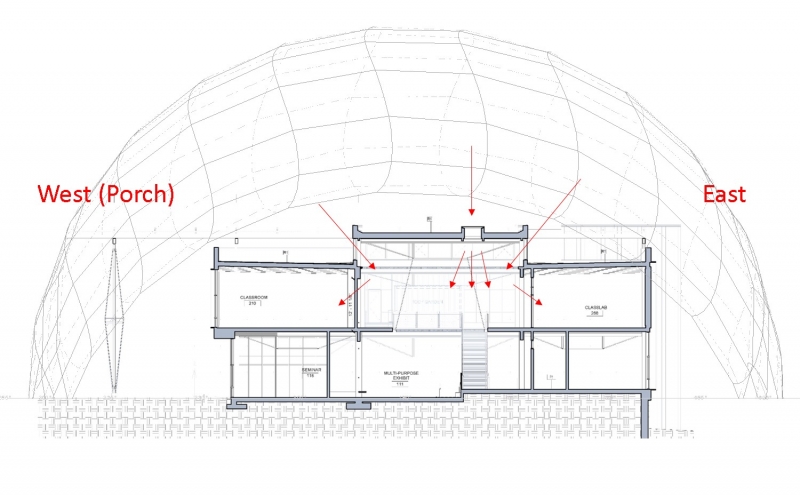
In our February post titled "A Living Building Project Journey Part-6, Net Positive Energy", we outlined the process being used to design a project that produces at least 105% of the energy it consumes on an annual basis. We discussed the intentionality and rigor behind the decision-making process, the energy conservation measures under consideration, and some modeling results.
In late September, the design team presented the project at the 2017 ASHRAE Building Performance Analysis conference under the title, ‘Net-Positive Energy Performance in the Southeast through an Integrative Design Process’. The conference focused on the role of building performance analysis in design, operation, and policymaking. There was great emphasis on asking the right questions to most effectively inform analysis, choosing the right simulation tools and techniques for the job at hand, and graphically presenting the results to aid decision making. A session on lessons learned from ZNE (Zero Net Energy) projects focused not only on the best process to validate ZNE projects, but also on how ZNE success is 50% design intent and 50% monitoring-based operation.
This post builds on February’s Net Positive Energy post by sharing select design questions evaluated through building performance analysis since then as compiled for our technical presentation at the ASHRAE conference.
Q1. Given the depth of the porch, do the windows of the 2nd floor west-facing classrooms under the porch need exterior operable blinds that aid in solar load reduction?
Solar geometry analysis was conducted in Revit to assess the extent of afternoon direct solar gains on the 2nd floor glazing seasonally.
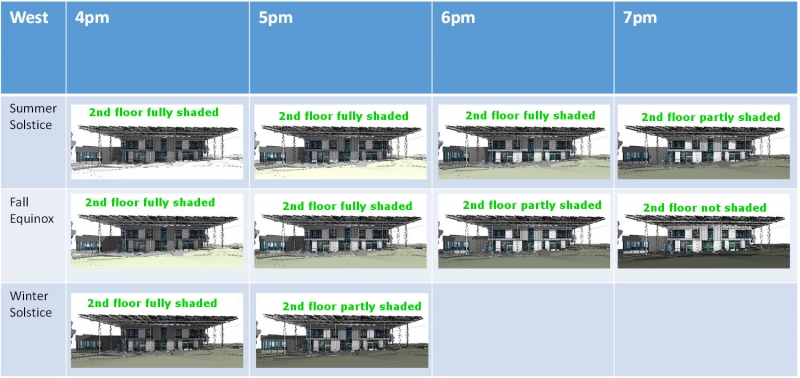
FIGURE 1. Shading analysis in Revit. (Image courtesy of Lord Aeck Sargent in collaboration with Miller Hull)
Based on the shading analysis, it was determined that the 2nd floor experiences direct solar gain only very late in the shoulder seasons, with full exposure not occurring until approximately 7:00pm and immediately before sunset in the winter.
Comfort analysis was also conducted to assess the efficacy of operable shades in the 2nd floor, west-facing classrooms. Specifically, the team used IES Virtual Environment to determine whether the space setpoint of 78 degrees was exceeded with or without shades.
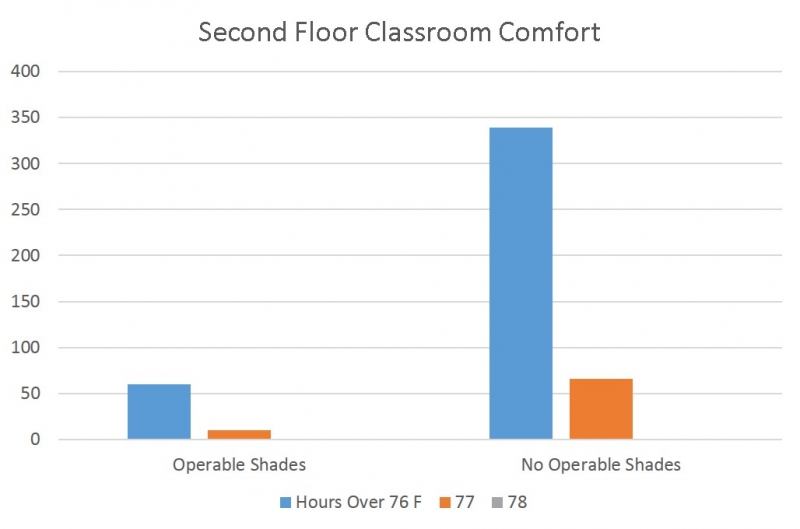
FIGURE 2. Comfort analysis showing the number of hours exceeding 78F (space setpoint) in the space remain unchanged. (Image courtesy of PAE Engineers and Newcomb & Boyd)
This analysis led to the decision not to provide operable blinds on the exterior for the 2nd floor west-facing windows under the porch. The team made a similar decision for south-facing classroom and atrium windows without localized overhangs, again owing to the shading provided by the PV canopy overhang. This resulted in first cost savings for the project by eliminating unneeded shades that would have otherwise been included had their efficacy not been directly assessed.
Q2. Given the raised atrium roof configuration with clerestory windows, how much does the atrium’s daylight illumination benefit from retaining the three skylights currently planned?
Analysis was conducted using IES Virtual Environment to assess the adequacy of atrium daylight with and without the prismatic skylights.
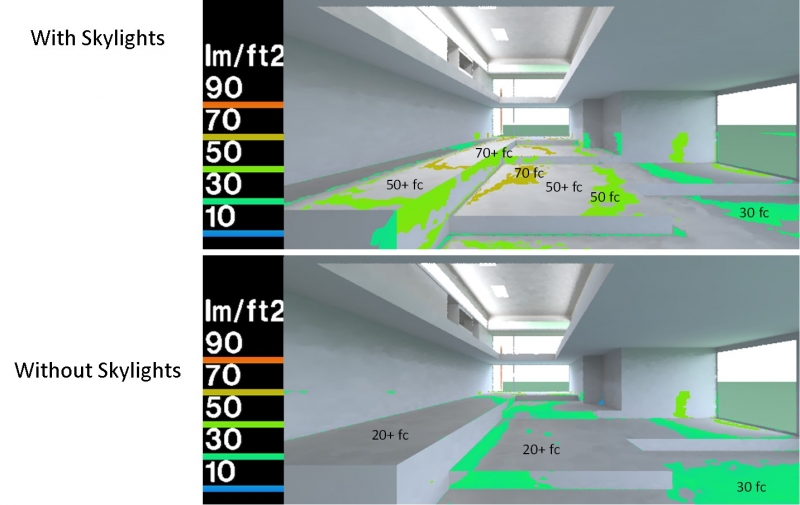
FIGURE 3. Daylight simulation results of 'With Skylights' and 'Without Skylights' scenarios. (Image courtesy of Lord Aeck Sargent in collaboration with Miller Hull)
The results shown above are for a single point in time simulation for September 21 at noon under sunny sky conditions. The three 5’x10’ prismatic skylights, representing only 5 percent of the atrium roof area, significantly improved the quality and quantity of daylight in the atrium. Based on the analysis, it was determined that the estimated $6,950 first cost premium for the skylights represented good value, so they remained in the design.
Q3. What is the energy impact of providing coffee onsite?
The team evaluated the energy associated with providing varying types of on-site coffee service. The acronym EUI stands for the metric “Energy Use Intensity,” measured in kBtu/sf/year. EUI is analogous to the MPG rating of a car. Espresso coffee had the highest demand at 0.7 kBTU/sf/year, whereas cold brew coffee had the lowest impact at 0.25 kBTU/sf/year. Based on that analysis, the hot water coffee option, with an intermediate EUI impact, is planned to provide a desired amenity at a moderate energy demand.
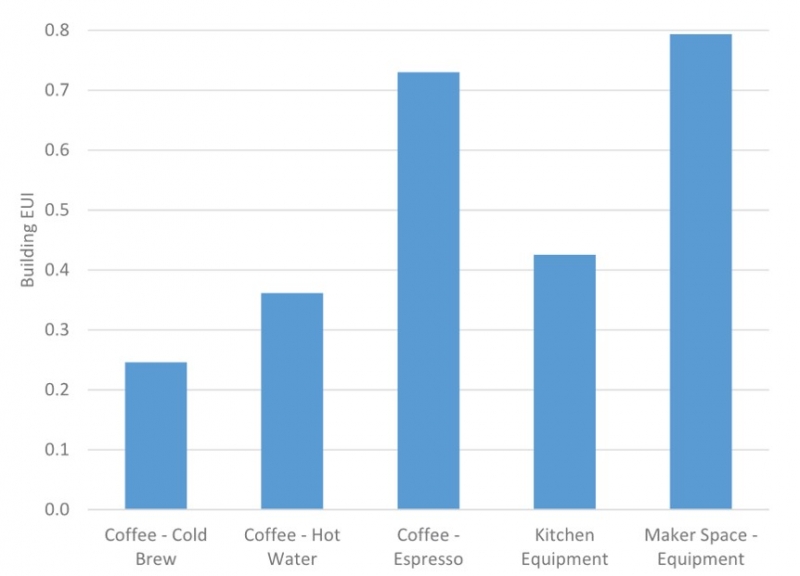
FIGURE 4. EUI penalty of three different coffee options. Additional end uses included for context. (Image courtesy of PAE Engineers and Newcomb & Boyd)
You can read more on the topic of energy and coffee in a blog post by one of our project partners.
Q4. What is the EUI impact of operating some portions of the project continuously (24x7), compared to the more conventional building operation hours (70 hours per week) previously under consideration?
The team evaluated the impact of changing to continuous operations/occupancy for labs and offices using IES Virtual Environment.
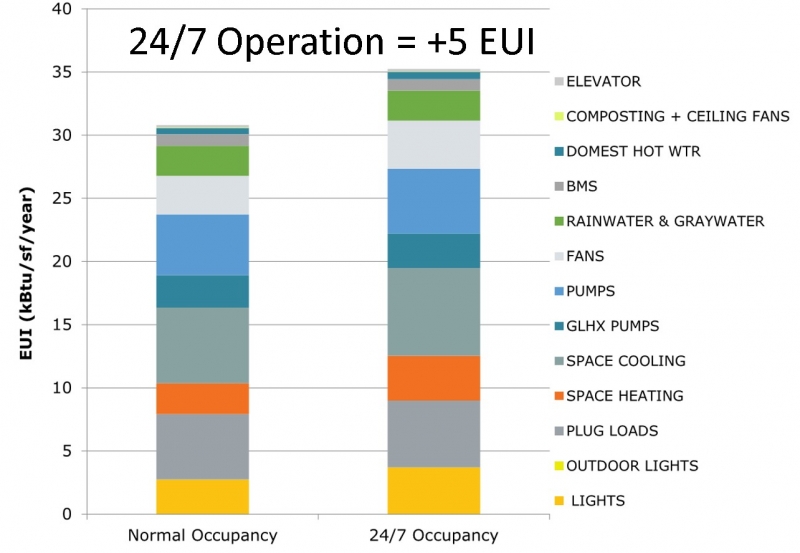
FIGURE 5. Simulation results for the impact of continuous operations for portions of the project. (Image courtesy of PAE Engineers and Newcomb & Boyd)
Simulation results indicate an increase of 5 EUI units for 24x7 operation of some portions of the project. The increase can be attributed primarily to higher usage of lighting and HVAC as illustrated above.
Conclusion
At the conclusion of Design Development, the predicted EUI of the project is at approximately 35 kBtu/sf/year. Onsite photovoltaics (PV) will provide 105% of this energy budget, consistent with the Living Building Challenge’s Net Positive Energy requirement. An additional 15% safety factor has been included to account for unknowns and provide additional operational flexibility, with the PV system projected to produce approximately 425,000 kWh annually.
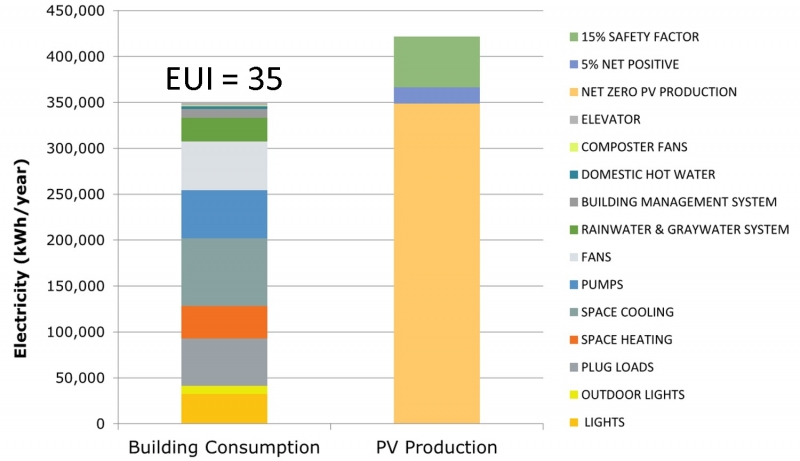
FIGURE 6. Currently projected energy consumption and renewables production. (Image courtesy of PAE Engineers and Newcomb & Boyd)
Funded through a private grant from The Kendeda Fund, Living Building at Georgia Tech is expected to become a Living Building Challenge 3.1 certified facility – the built environment's most rigorous and ambitious performance standard. The project’s design and build partners include architects Lord Aeck Sargent in collaboration with The Miller Hull Partnership, construction manager Skanska and design team consultants: Newcomb & Boyd, PAE Consulting Engineers, Uzun + Case, Biohabitats, Andropogon and Long Engineering.
Comments
A Living Building Project Journey, Part-11
The Role of Research
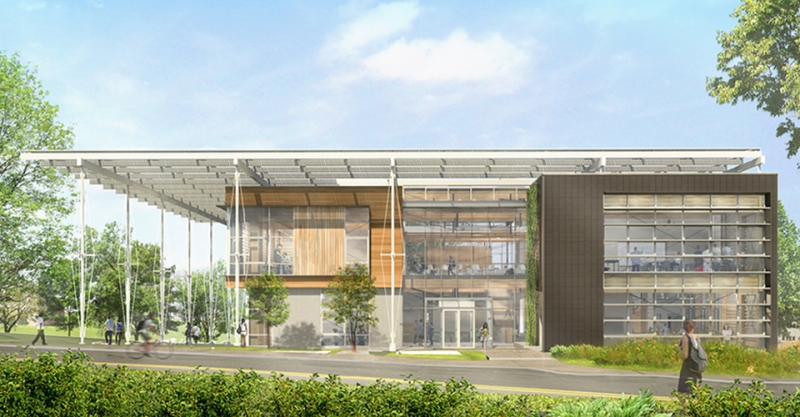
As building performance has grown in importance, the incorporation of quantitative analysis and research in architectural practice is gaining increased traction. A typical project delivery process might occasionally dabble with research in a limited fashion to answer particular design questions, but research is yet to have a formal place and role in most practices. Even when research does occur, researchers rarely document the methodology and reasoning for the benefit of people outside the project team. Depending on your perspective, concerns such as project budget, project schedule, and client requirements, could be either drivers or challenges.
A logical and philosophical question to ask would be: “What is the distinction between research and design?” According to Linda Groat and David Wang of Architectural Research Methods:
"Design and research constitute neither polar opposites nor equivalent domains of activity. Rather, the relationship between the two is far more nuanced, complementary, and robust."
While there might be an academic bias to this statement, there is no doubt that targeted research has the potential to improve the quality of design, even for practitioners.
Research on the Georgia Tech Living Building project has either already spanned, or will span, across all Petal areas: Place, Water, Energy, Health + Happiness, Materials, Equity, and Beauty. We will explore the role of research on this project using three examples.
Site and the Building
The team studied the history of the site from 1928 to 2016, examining changes in use, development, and topography.
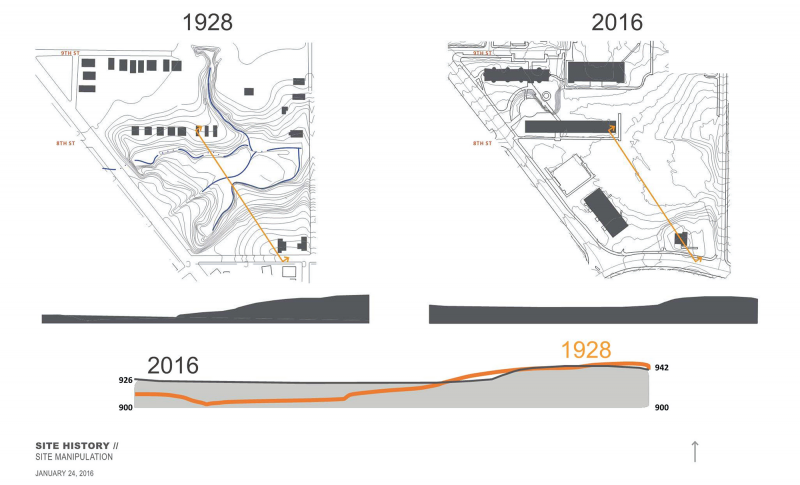
Developing an understanding of the site has helped inform several critical areas:
- A site hydrology design that mimics the Piedmont forest in the way it absorbs and releases water. This strategy is integral to the net-positive water performance of the project.
- An approach to landscape design that, while engaging the community, complements the larger vision for the Eco-Commons context and is culturally and environmentally responsive.
- An understanding of the locations of undisturbed soils on site, which is critical for effective natural wastewater treatment design
The initial design schemes, Porch and Bridge Trot, resulted from research into vernacular architectural precedents in the Southeast, were considered to understand traditional architectural responses to the region’s climate in the era before artificial lighting and mechanical cooling.
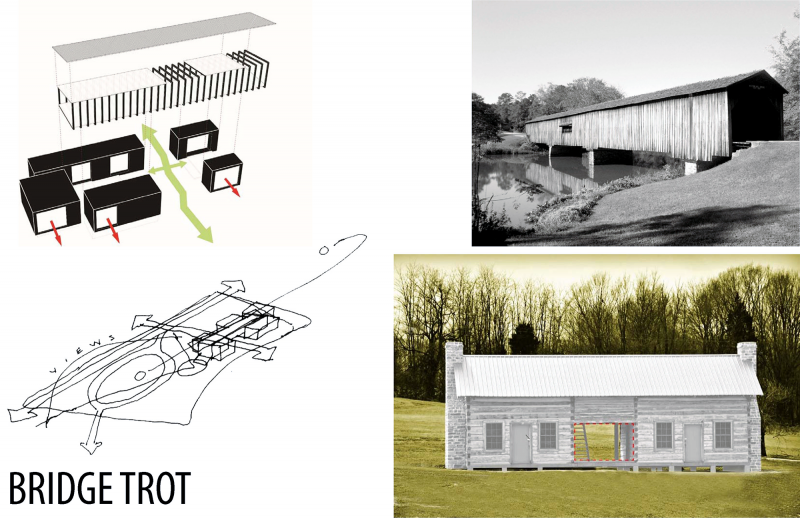
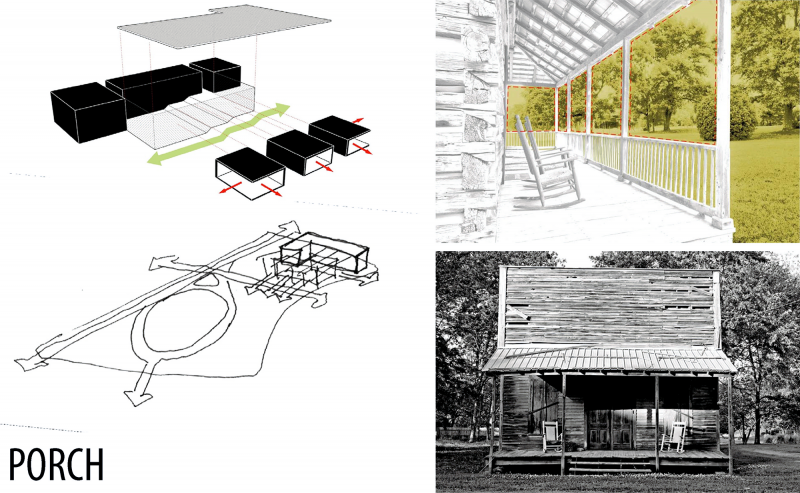
Material Vetting
The requirements of the Materials Petal has necessitated the most laborious focus of research on the project to date.
Since the Materials Working Group’s kickoff in August 2016, the group and the design team have vetted dozens of building materials and products. The most challenging criteria has been to avoid the 22 red listed chemicals and their 800 or so variants. Considerable research went into choosing and employing the web-based software tool ‘Portico’, a cutting edge and one-of-a-kind program being pioneered by Google and Healthy Building Network. The project team’s use of the tool should add a plethora of new products to its database and inform future development in other ways.
The team has scoured local projects for their potential for salvaged materials. Granite from the Georgia Archives building and timber from a local church, tower and downed trees are just some of the salvaged materials the team is tracking to incorporate creatively into the project’s design.
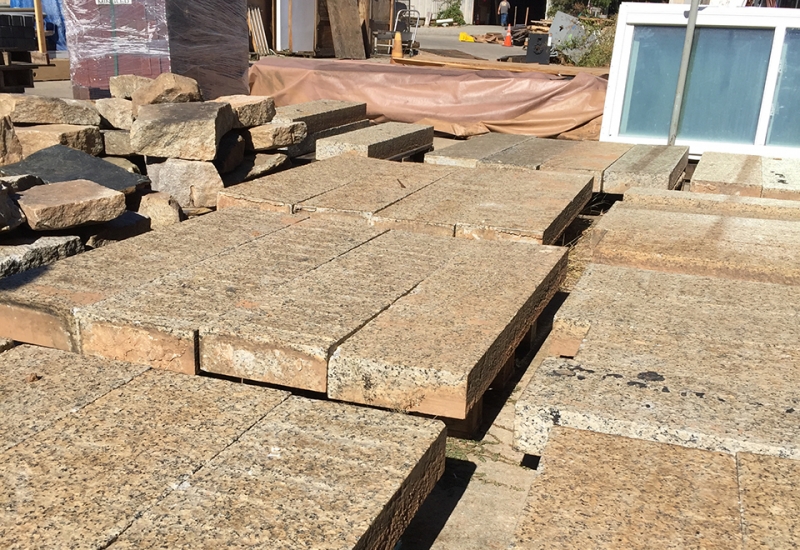
FIGURE 1. Granite curbs salvaged from the Georgia Archives Building. Image by Jimmy Mitchell.
All wood on the project, excluding salvaged wood and intentional harvest of on-site timber, must meet the Forest Stewardship Council’s (FSC) 100% labeling standards. The owner and the design team started the project with the goal of specifying as much wood from Georgia as possible. Early in the process, the project team compiled a detailed list of all potential wood-based products on the project. Initial market research included web research, emails and phone calls. Based on the potential wood product list, research conducted by the Construction Manager and the designers, in collaboration with FSC staff, revealed that most of Georgia-based FSC-certified wood was being used to produce pulp for paper and cup stock. There was little to no potential for dimensional lumber or other conventional wood building products. Although this was not surprising, the research served the purpose of due diligence and met the LBC’s intended benefit of advocacy.
Post Occupancy Evaluation
For successful Living Building Challenge (LBC) certification, the project must demonstrate net positive energy and net positive water performance over a performance period of 12 months with full operational occupancy. The performance period begins at substantial completion (anticipated in 2019) and success is based on collected data during the performance period. The project team expects the comparison of predicted and metered performances and the adjustments, if any, necessary to demonstrate net positive performance to provide a rich source of research data for both practitioners and academia.
Conclusion
These three examples provide a sense of the ongoing and future research conducted for the Georgia Tech Living Building project. Biophilia (Health & Happiness Petal), art (Beauty Petal), and social justice (Equity Petal) are some of the other noteworthy areas. Green Building Certification requirements continue to emphasize research and retrospection, extending their roles well beyond the design phases of a project.
Funded through a private grant from The Kendeda Fund, the Living Building at Georgia Tech is expected to become a Living Building Challenge 3.1 certified facility – the built environment's most rigorous and ambitious performance standard. The project’s design and build partners include architects Lord Aeck Sargent in collaboration with The Miller Hull Partnership, construction manager Skanska and design team consultants: Newcomb & Boyd, PAE Consulting Engineers, Uzun + Case, Biohabitats, Andropogon and Long Engineering.
Comments
Learning Through Doing, Recognizing Student Work
2017 Architizer A+ Award-Winning “Guga S’Thebe Children’s Theatre”
Learning Through Doing, Recognizing Student Work:
2017 Architizer A+ Award-Winning “Guga S’Thebe Children’s Theatre”
Many college degree programs require students to work in their field, whether through practical courses or internships, before they graduate. Architecture is no different, but the possible paths to fulfilling that requirement are seemingly endless. Whitney Ashley, an Intern Architect in Lord Aeck Sargent’s Science & Technology practice area, shares her hands-on experience gained working on a design-build project while earning her Master of Science in Architecture from the Georgia Institute of Technology in 2015.
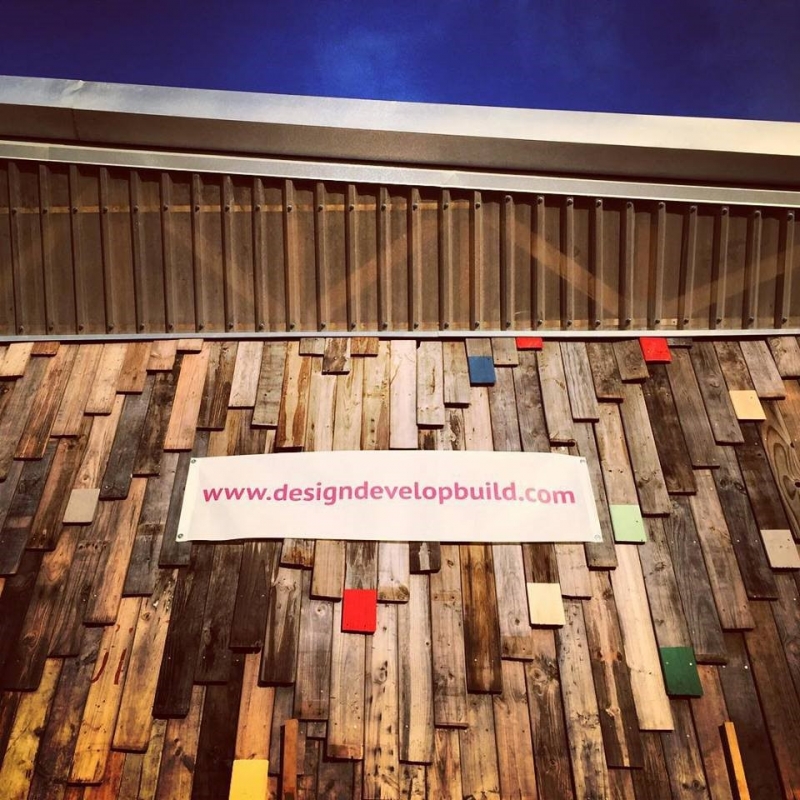
Whitney’s Story
I was part of the award-winning Guga S’Thebe Children’s Theatre, located in Cape Town, South Africa, while earning my Masters of Science in Architecture, with a concentration in Digital Design and Fabrication. The project, which was recognized in the Cultural-Hall/Theater category, involved a team of architecture students from Georgia Tech, the Peter Behrens School of Arts in Dusseldorf, Germany and RWTH Aachen University in Aachen, Germany.
The Children’s Theatre provides a place for music, play, learning, and creativity for the children where it is a part of an existing facility called Guga S’Thebe located in the Township of Langa. It is a place for the people of Langa to exhibit their art, culture and heritage. This building, which attracts tourists from all over the world, held this exchange program for the visiting students. My group joined the theatre project in its third and final year of construction.
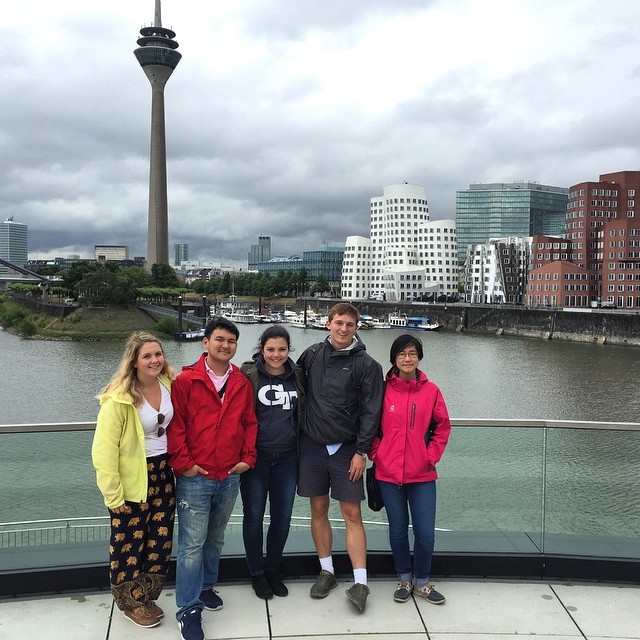
Our study abroad program began with the Georgia Tech students attending the German universities for a month. While there, we were taught different fabrication methods by creating various design-build projects for the theatre, such as tables, chairs and planters. The exercises included utilizing recycled materials such as used pallets, which students disassembled and repurposed to provide building materials for each project. This exposed us to hands-on design, fabrication and construction.
Our instructors also challenged us to create a digital proposal, using Rhino and Grasshopper, for a canopy structure over the existing outdoor amphitheater space at Guga S’Thebe. We knew that Digital Design and Fabrication were both essential skills we needed to master in order to be prepared before arriving in South Africa.
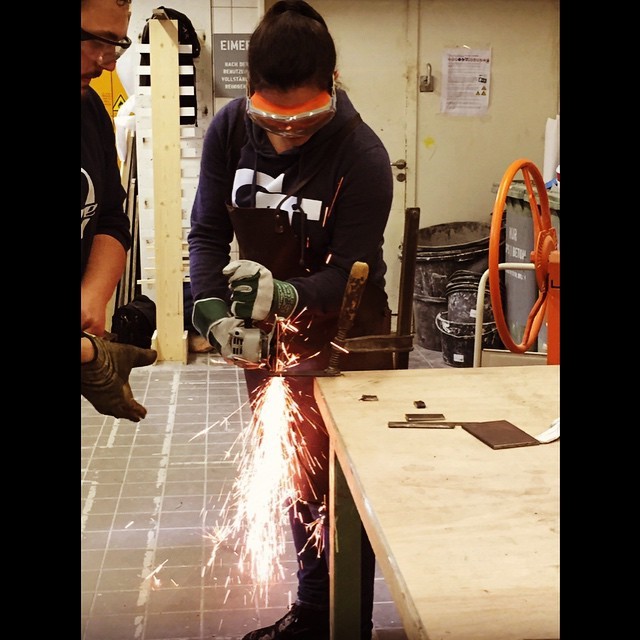
The American and German students soon arrived in Cape Town where we were quickly acclimated into a new culture. Our tasks included focusing on finishing the facade, landscape design and acoustic panels in the recording studio; and interior finishes in the kitchen, balconies and main space. The construction project included both students and residents of the Township of Langa. This created opportunities for a rich dialogue between the local people and the students. The project enabled students to learn about construction while also being exposed to new cultures and experiences.
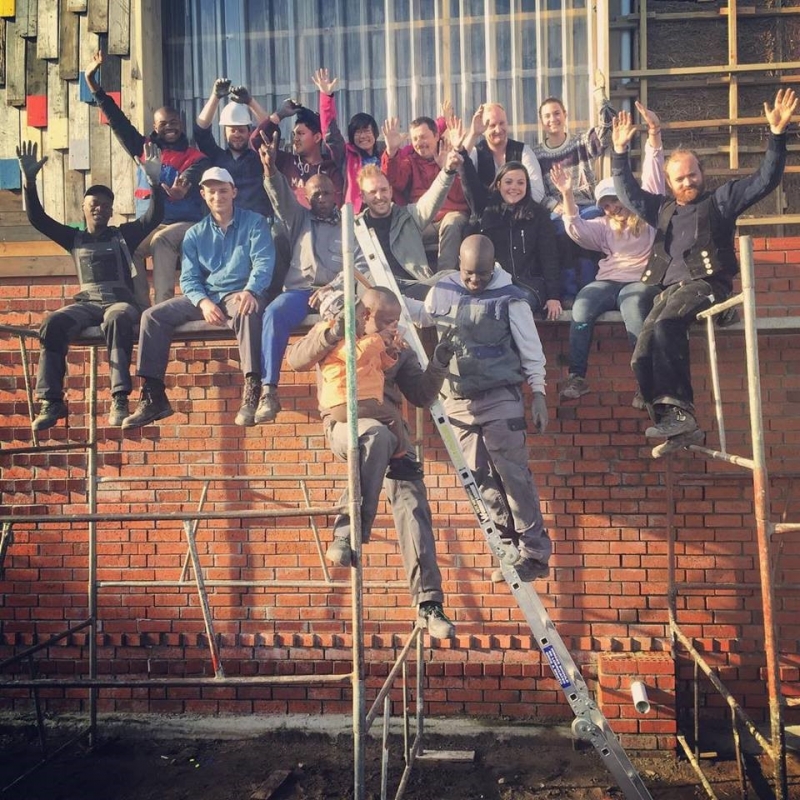
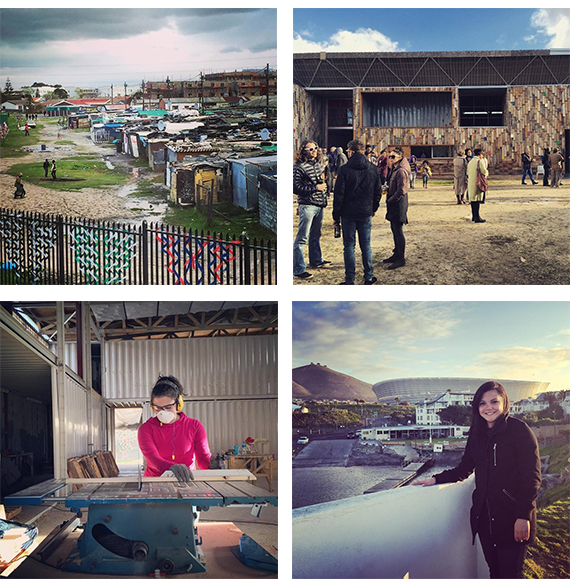
The built architecture at Guga S’Thebe is unique and culturally reflective. The building’s main structure and volume is derived from re-used shipping containers, which define an internal space for the theater. The materials in the project are recycled, reused or naturally renewable local from the community.
The Design-build project has helped me understand how to develop a design that includes using renewable and local resourced materials while bringing it to actualization. The exposure of living in two countries has enabled me to experience new cultures. In the end, the goal was to bring everyone together to complete a project that has a major impact on the Township of Langa. The most rewarding aspect was to be a part of a project that uses and develops my knowledge to create an environment that gives the children of Langa an opportunity to develop their skills and education in the arts.
The project was led by Design.Develop.Build. in collaboration with:
- Peter Behrens School of Architecture
- RWTH Aachen University
- Georgia Institute of Technology
- AIT-ArchitekturSalon
- CS Studio
- UCT Cape Town
- City of Cape Town
- Guga s‘Thebe - Arts and Cultural Centre, Langa
- Imagine structure GmbH
- Habitat for Humanity, UCT
- Detmold University of Applied Sciences
- Imagine structure GmbH
- S. Imail Consulting Electrical Enigneers
- Solution Station
- Transsolar Energietechnik GmbH
- Build Collective
- MiTek
- Peutz Akustik
- Carl Lutzeler
- Heribert Weegen
Learn more about the project at https://architizer.com/projects/guga-sthebe-childrens-theatre/
Comments
A Living Building Project Journey, Part-10
Water Balance, Part 2: Ecological Water Flows
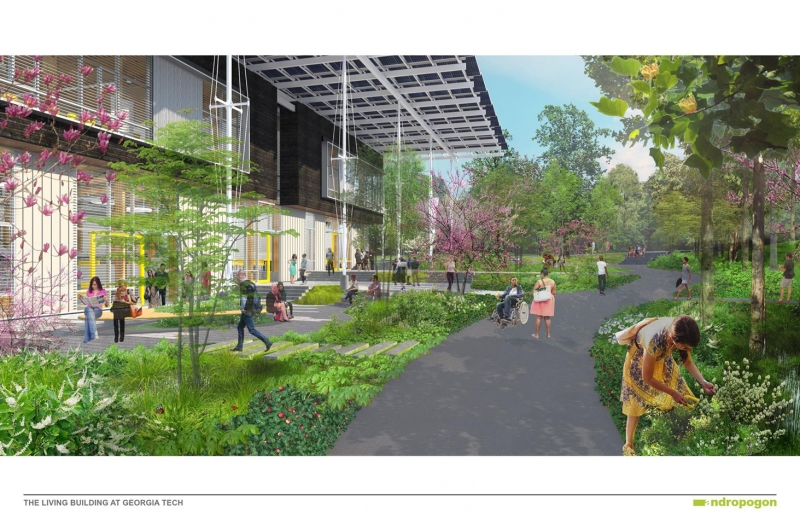
The Living Building Challenge’s (LBC) Net Positive Water imperative stipulates that a project’s “water use and release must work in harmony with the natural water flows of the site and its surroundings.” For the Living Building at Georgia Tech, this means mimicking the Piedmont forest in the way it absorbs and releases water. By integrating building and site hydrology, and leveraging stormwater as a resource, the Living Building aims to achieve net-positive water. The project’s stormwater design focuses on the fundamental driver of gravity and its interaction with rainwater systems. Rainwater management is a two-tiered approach that targets volume and rate, while prioritizing low-impact systems that maximize useable footprint, water storage and scalability. The project’s earlier design phase focused on rainwater management of volumes, whereas the current design development phase expands these tasks to target the LBC’s challenging groundwater recharge goals. To learn more about the overall water balance, see our post from January.
The LBC’s Water Petal performance category requires that the Living Building produces more water than it consumes on an annual basis. Communication and coordination across all design disciplines ensured that Water petal goals could be met, while incorporating ideas from other petals increased the comprehensiveness and sustainability of the Living Building design. This coordination effort was mostly driven by the site design, which satisfies the LBC’s Place Petal requirement of providing accessibility along the site’s natural topography to promote Equity. Creative approaches were balanced to provide efficiently designed, high-performance systems that rely upon natural processes.
The project site moderately slopes from south to north, with the building and adjacent Porch plaza designed to follow this natural topography by terracing, or stepping down, at appropriate elevations. This geometry accommodates cascading Porch areas that support substantial volume storage underneath permeable pavers. Unlike a traditional stormwater management approach that concentrates water storage in a single area, this method of managing rainwater in dispersed locations along a sloped site, through dynamic interactions, requires careful use of gravity as a tool for equalization.
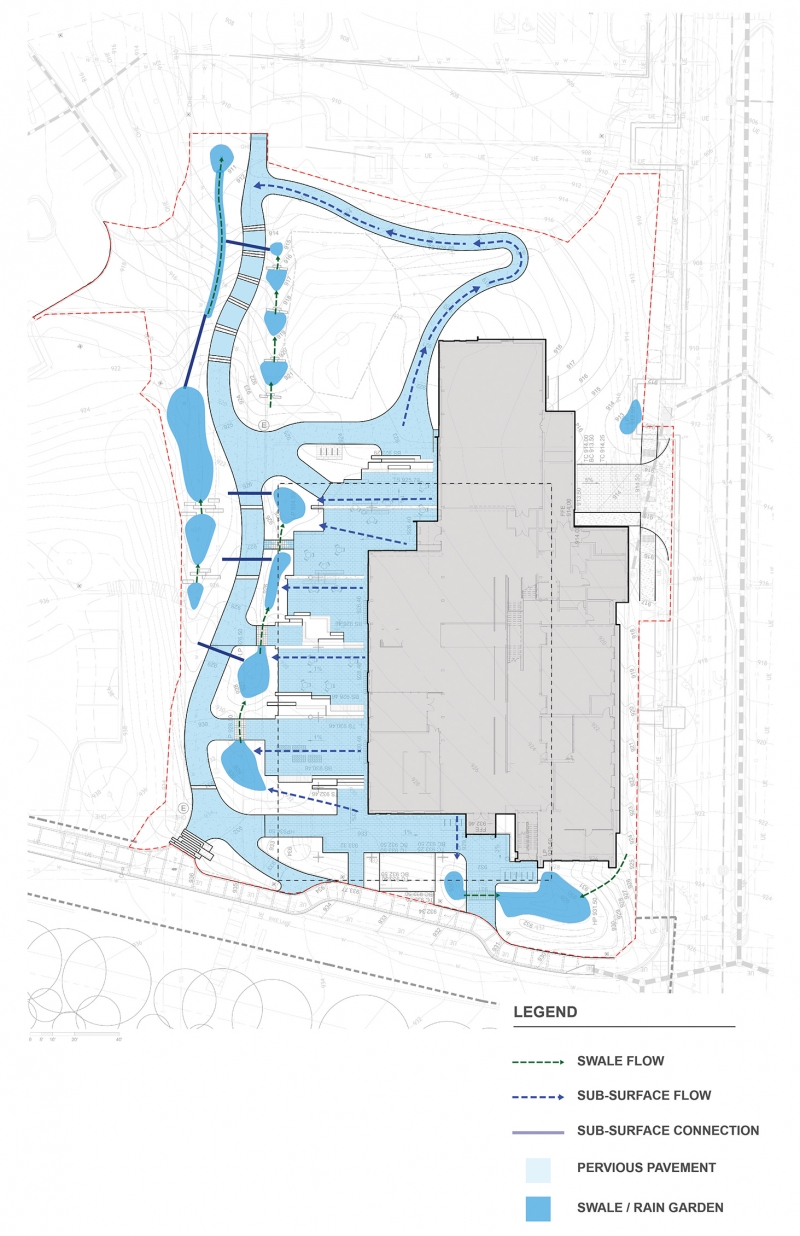
FIGURE 1. Site water flows. Image courtesy of Andropogon.
The final approach involves strategically linking these small subgrade storage sections with surface swales at similar elevations to achieve multiple functions: storage, conveyance, infiltration and overflow, while allowing flexibility in storage not dependent on structural components to ensure efficiency. Strategic placement of grates over these overflow areas allow the educational opportunity of visualizing the interaction of these terraces with a functional approach in line with the intent of the Beauty Petal.
While these terraced management areas allow substantial volume storage, they are designed to treat the majority of the flows attributed to building overflow and the runoff from upstream sections of the terraced system. The majority of the site that connects the project to the campus are at an elevation and a slope that prevent continual interactions with the larger storage system. However, due to the efficiency and scalability of the larger storage system and its ability to treat the major sources of volume, the natural slope and hillside can be maintained along the walkways and landscape while allowing a creative approach to treat the smaller volumes attributed to these areas.
Permeable concrete sidewalks allow rainwater to infiltrate through walkways to be treated and conveyed within the gravel base underneath. This system is a low impact technique for preventing runoff and requiring piped conveyance to a treatment system while infiltrating smaller local volumes. The footprint of this system is meant to follow the natural existing slopes, which requires underground, “stepped” gravel beds in sloped sections. In the flatter sections, reclaimed granite curbs salvaged from the Georgia Archives Building will visually highlight the locations of these infiltration sections, while also functionally separating of the gravel base elevations to maximize water storage. In steeper sections, underground “dams” enable necessary storage volumes while allowing un-piped, sub-grade overflow to move downslope.
Collectively, these strategies could reduce Georgia Tech stormwater runoff and municipal water usage, recharge the aquifer and extend the Living Building’s Water Petal’s goals beyond the project site and certification requirements.
Funded through a private grant from The Kendeda Fund, the Living Building at Georgia Tech is expected to become a Living Building Challenge 3.1 certified facility – the built environment's most rigorous and ambitious performance standard. The project’s design and build partners include architects Lord Aeck Sargent in collaboration with The Miller Hull Partnership, construction manager Skanska and design team consultants: Newcomb & Boyd, PAE Consulting Engineers, Uzun + Case, Biohabitats, Andropogon and Long Engineering.
Comments
A Living Building Project Journey, Part-9
Living Building Challenge – Designing Under the Influence
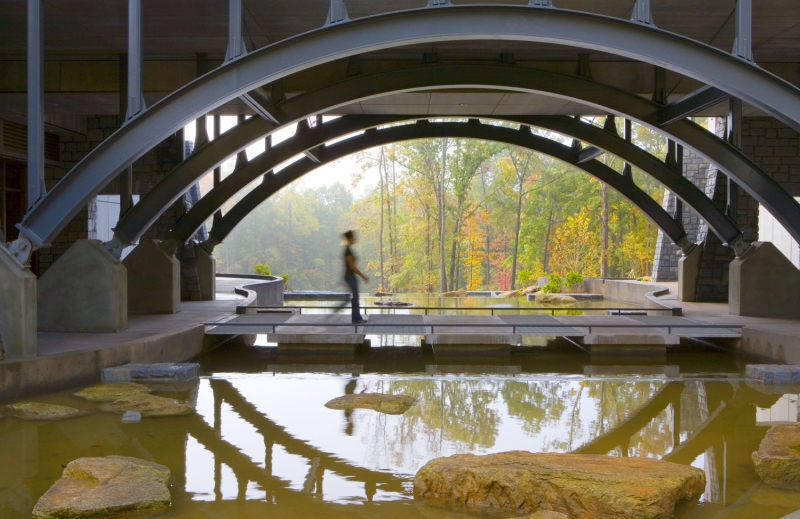
In his book, ‘Architecture and Ritual: How Buildings Shape Society’, the late architectural historian Peter Blundell Jones explores a hypothesis that architecture and ritual are closely related. He posits that the interaction between people and their habitat is much more complex than ‘form follows function’. In attempting to define architecture after challenging existing definitions, he points to the narrowness that results from relying purely on material and technical points of view. A more meaningful definition, he argues, would also include the social, spiritual, and cultural aspects.
The Living Building Challenge (LBC) certification, in its own way, explores a more complete definition of architecture. While acknowledging their importance, it transcends the material and technical aspects, and compiles the issues it considers relevant into an all-or-nothing framework. Consider this statement from the introductory text of the standard’s guidance document:
During a March 2017 presentation at Georgia Tech, LBC’s founder and chairman of the board of the International Living Future Institute, Jason F. McLennan, focused on similar themes. For projects not pursuing the LBC certification, he encouraged the design teams to ask themselves, at a minimum, the following three questions related to ‘Regenerative Design Practice’:
- Does our design create more abundant conditions for life and the diversity of life? (Ecotone question)
- Does our design honor the spirit and potential of this place? (Biophilia question)
- What would other species do to inform this design? (Biomimicry question)
In February 2017, Lord Aeck Sargent (LAS) conducted an interesting compare-and-contrast thought experiment. At an internal, firm-wide presentation on the progress of the Living Building at Georgia Tech, attending staff were asked to list three ideas that demonstrated what sustainable design meant to them before the presentation. They were asked to perform the same task after the presentation. We wanted to determine if discussing and exploring LBC ideas would have an impact on their responses. Of the 40 or so responses, 58% of the ‘after’ responses differed from their corresponding ‘before’ responses. Here is a summary of the findings:
- The term regenerative occurred once in the before responses and six times in the after responses.
- The term beautiful occurred once in the before responses but four times in the after responses.
- The term durable (or variants) occurred 12 times in the before responses but only four times in the after responses.
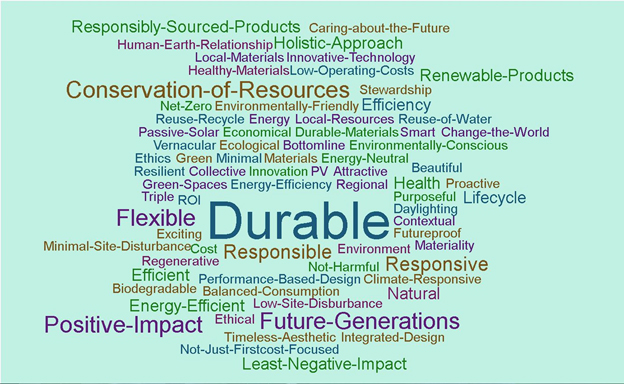
FIGURE 1. A word map of the ‘before’ survey responses. Font size indicative of the frequency of a term’s occurrence.
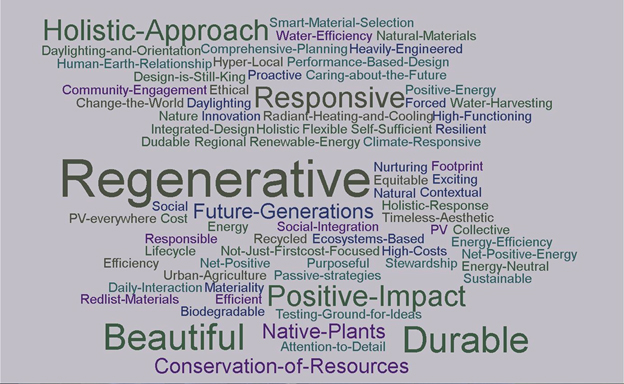
FIGURE 2. A word map of the ‘after’ survey responses. Font size indicative of the frequency of a term’s occurrence.
As LAS has undertaken its latest sustainability strategic planning effort for 2017, in concert with a firm-wide dialogue to establish Core Design Values of responsive design, the term ‘regenerative’ has figured prominently in the discourse.
Consistent with Jason’s admonition to consider regenerative design for all projects, we are attempting to establish minimum sustainable design criteria, improved design team resources, and enhanced accountability for the routine incorporation of sustainability considerations, not just for ‘deep green’ demonstration projects that have sustainability as a key program driver, but for all design efforts undertaken at LAS.
In addition to Ramana and Jim, Joshua Gassman, RA, LEED AP BD+C, Alissa Kingsley, LEED AP, and Whitney Ashley contributed to this post.
Funded through a private grant from The Kendeda Fund, the Living Building at Georgia Tech is expected to become a Living Building Challenge 3.1 certified facility – the built environment's most rigorous and ambitious performance standard. The project’s design and build partners include architects Lord Aeck Sargent in collaboration with The Miller Hull Partnership, construction manager Skanska and design team consultants: Newcomb & Boyd, PAE Consulting Engineers, Uzun + Case, Biohabitats, Andropogon and Long Engineering.
Comments
A Living Building Project Journey, Part-8
The Ripple Effect: Recent Partner Activity
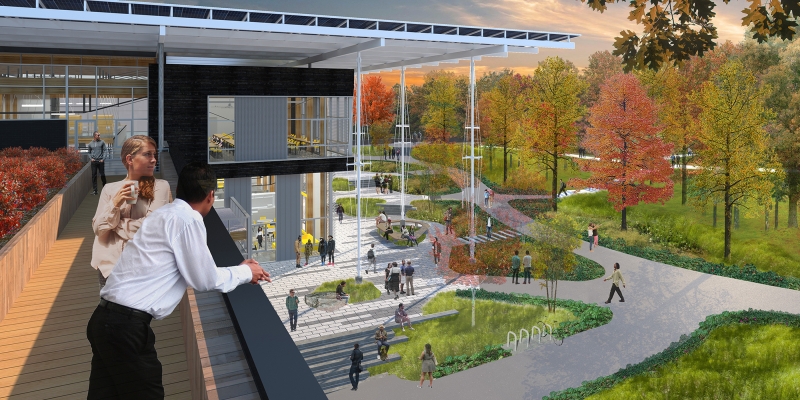
As we begin to develop and resolve the finer details during the design development phase of the Georgia Tech Living Building project, our project team and process are constantly brimming with ideas and activity. The goal of the Living Building at Georgia Tech has been not just to create the most environmentally advanced education and research building ever constructed in the Southeast, but for the project to be a catalyst for sustainability in the region. This post highlights some of the activities of project partners to promote sustainability beyond the campus of Georgia Tech.
It’s never just about the building
Dennis Creech, a fund advisor and a member of the leverage team at The Kendeda Fund, eloquently sums up some finer points about the Living Building Challenge (LBC) certification in a recent interview.
There are a lot of words we use to describe a building standard that goes beyond doing less harm and aspires to actually improve the environment — restorative, regenerative. That ambition is one part of the Living Building Challenge that’s very admirable.
But, in my mind, there’s something else just as significant: It’s holistic. It’s not just about the environment in isolation, without considering its connection to people. I think the Living Building Challenge recognizes that to be restorative to the planet, it has to address the needs of people.
Read the full interview on Kendeda’s Living Building Chronicle.
Miller Hull Seattle Studio Now Living Building Challenge Petal Certified
Miller Hull, the design partner of LAS on the Georgia Tech Living Building project, recently achieved Petal Certification under the Living Building Challenge. They transformed 14,000 sf of their own office space in the historic Polson Building in Pioneer Square, Seattle, to meet and exceed the requirements of Place, Health & Happiness, Materials, Equity and Beauty Petals. Meeting the requirements of at least three petals with one of them being Energy, Water, or Materials is necessary for pursuing Petal Certification.
Read more about their strategies and metrics on Miller Hull’s website.
Net-positive in Atlanta’s heat
Our MEP design partner, PAE Consulting Engineers, rightly points out the challenges posed by Atlanta’s weather and the iterative modeling process being employed to design a net-positive energy building.
For Georgia Tech, designing to net-positive energy demands significant planning and design team coordination. To accomplish this, designers first prioritized cooling- and heating-load reduction options to minimize the energy needed and allow passive operation for longer periods of time.
Read the full article by Marc Brune and David Mead on Daily Journal of Commerce’s website.
Advocacy for human powered living
Promotion of wellness is a recurring theme for the LBC. The “Human Powered Living” imperative that falls under the plan’s ‘Place’ section calls for a design that promotes physical activity though biking, walking, and stair usage instead of reliance on cars and elevators for mobility. One other requirement under the same Imperative is the “advocacy in the community to facilitate the uptake of human-powered transportation.”
Georgia Tech is a natural fit for this advocacy requirement. By virtue of the creation of a Bicycle Master Plan and infrastructure improvements such as new bike lanes, additional bicycle storage, and quick repair stations, Georgia Tech’s commitment to human powered living predates its conception of the Living Building project. Tech’s plan and growth goals are integral to City of Atlanta’s Cycle Atlanta Phase I and II plans.
Read more about Georgia Tech’s Bicycle Master Plan and related efforts on its website.
Advocacy for building product transparency
As design teams in the Southeast ratchet up their materials research and vetting processes, the supply side has to reciprocate with transparency and the right tools to help with decision making. The local sustainability non-profit Southface Energy Institute has formed an industry council to bring all the stakeholders together.
Read more about Southface’s industry council initiative here.
Funded through a private grant from The Kendeda Fund, the Living Building at Georgia Tech is expected to become a Living Building Challenge 3.1 certified facility – the built environment's most rigorous and ambitious performance standard. The project’s design and build partners include architects Lord Aeck Sargent in collaboration with The Miller Hull Partnership, construction manager Skanska and design team consultants: Newcomb & Boyd, PAE Consulting Engineers, Uzun + Case, Biohabitats, Andropogon and Long Engineering.
Comments
A Living Building Project Journey, Part-7
Urban Agriculture
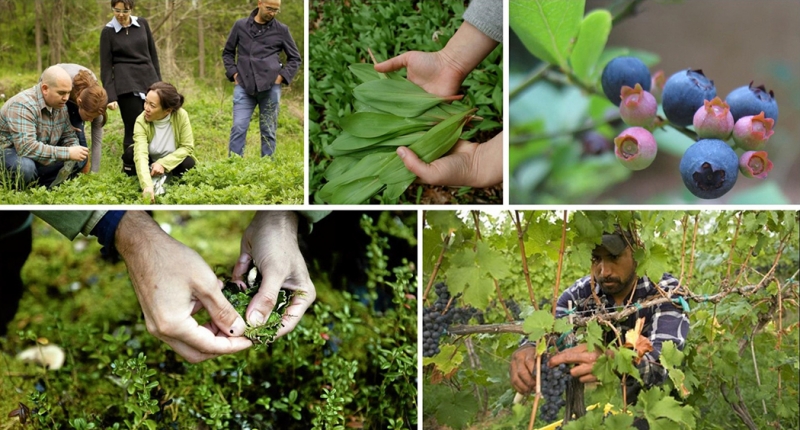
“A more resilient food system has more distributed food production, with greater availability of locally grown and locally processed foods,” argues Alex Wilson of the Resilient Design Institute.
A similar philosophy drives the Living Building Challenge’s (LBC) Urban Agriculture Imperative, one of the tenets of the rating system’s Place Petal. Under LBC v3.1, this imperative requires that projects dedicate a pre-determined percentage of the project site – ranging from 1 to 50% – to food production. The lower the project’s building density, known as the floor-to-area ratio (FAR), the higher the urban agriculture square footage requirement. Even single-family homes pursuing certification are subject to demonstrating the capacity to store at least a two-week supply of food. Given the Living Building at Georgia Tech’s anticipated FAR, 20% of the Project Area, or approximately 12,600 square feet, will be dedicated to fostering a healthy, accessible food system.
Local food access is particularly relevant to residents of Atlanta, a city that is no stranger to food insecurity. According to a 2015 Atlanta Journal Constitution investigation, just two years ago Atlanta contained 35 food deserts, which are locations where residents live more than one mile from a supermarket or other reliable source of fresh, nutritious produce, generally due to a lack of grocery stores, farmer’s markets and other healthy food providers. The U.S. Department of Agriculture’s Economic Research Service found that from 2013 to 2015, approximately 14.5% of Georgians were food insecure, which is greater than the national average of 13.7%
Early in the design process, Georgia Tech formed an urban agriculture subcommittee to work with the team’s landscape architects from Andropogon Associates. This collaboration has been helpful in ensuring that the Living Building project’s urban agriculture strategy remains relevant to the school’s objectives, challenging geographic setting and cultural context. Additionally, Georgia Tech is one of 15 universities nationwide certified as a Bee Campus USA, and the school supports an interdisciplinary undergraduate research and education program called The Georgia Tech Urban Honey Bee Project.
To vet the urban agriculture options that are possible within LBC’s parameters, Andropogon conducted a detailed study of different approaches such as intensive agriculture, permaculture, aquaponics, rooftop agriculture and a forage-driven edible landscape.
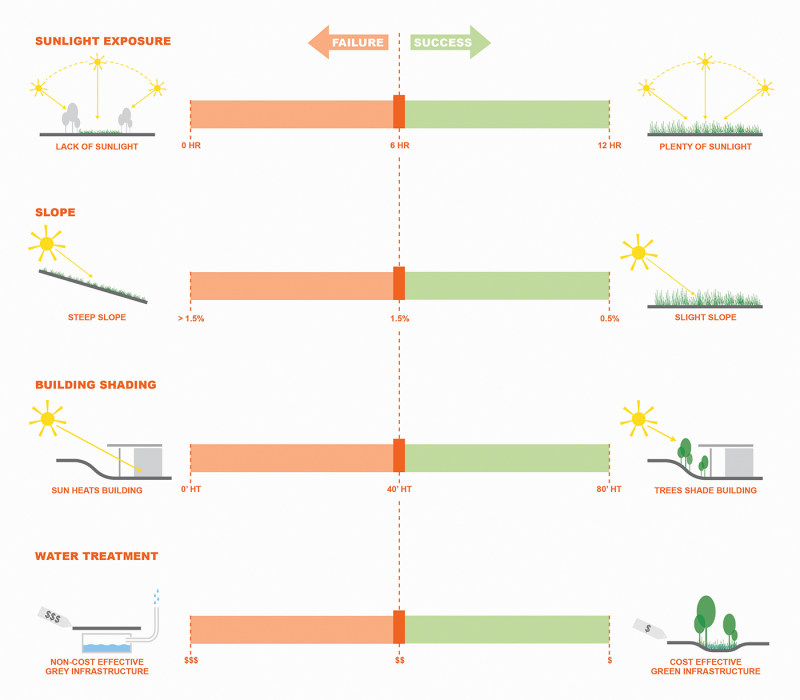
FIGURE 1. Performance thresholds for the success of intensive agriculture and interconnected project features. Image courtesy of Andropogon.
Intensive agriculture includes forms of production, such as row farming and raised-bed gardening, which typically requires high levels of inputs (e.g. water, sunlight, nutrients, labor) and produce abundant edible yields. Most crops that are suitable for this production type require irrigation; well-drained, loamy soil; a gentle slope that encourages infiltration; and at least six hours of direct sunlight per day. Intensive agriculture offers countless health and pedagogical benefits when deployed under appropriate conditions.
The Living Building at Georgia Tech landscape must navigate competing performance demands for rainwater management, passive building cooling, tree protection, healthy ecology and urban agriculture, while providing adequate space for human occupancy and year-round seasonal character. When combined, these conditions present significant challenges to implementing a successful, intensive urban agriculture program on the ground plane. As a result, the project will include the following components:
Rooftop “Farm”
The sunniest, flattest, most secure area within the project site is the roof. The Living Building at Georgia Tech‘s 2,895-square-foot rooftop farm will consist of a honeybee apiary, pollinator garden and blueberry orchard. These elements will satisfy a portion of the LBC’s urban agriculture area requirement while simultaneously offering valuable curriculum and research opportunities; reconnecting students, faculty and visitors with their food system; modeling sustainable, productive infrastructure; demonstrating medicinal uses for plants; supporting pollinators and pollinator habitat conservation awareness; managing stormwater; and helping mitigate the urban heat island effect.
Edible Vine Wall
Additional urban agriculture area will be achieved through two edible vine walls, totaling 1,470-vertical-square feet. The vines will be planted in at-grade planting beds and will grow up guy wires to occupy portions of the auditorium’s west façade and southern stairwell’s south façade. The auditorium vine wall will provide a green backdrop and shading for the interior space, through a large glass curtain wall. The native vine’s edible grapes will require specialized harvesting and can be eaten whole or processed. Georgia-native passion fruit vines will also be considered to supplement the native grape vines.
Pollinator Nectar Source
As a complementary amenity, at least 2,862 square feet of Tulip Tree (Liriodendron tulipifera) canopy, which supports spring flowers that provide southern honeybee foragers with a critical early season nectar source, will be planted. Serviceberry (Amelanchier arborea) and Fothergilla (Fothergilla spp.) will also support bee populations, but these plants will be mixed into the understory.
Edible Landscape
The bulk of the urban agriculture area requirement will be met with a 5,350-square-foot shade-to-partial shade edible ground landscape. Understory trees, shrubs and groundcovers that produce edibles, coupled with interpretive signage, will encourage students, staff and visitors to pick and eat tree fruit and berries from January through December. This landscape will provide nutrition through seasonal edibles, while working seamlessly with the landscape’s adjacent proposed mesic woodland and seepage wetland zones to manage stormwater runoff from the site’s pavement. Additionally, this type of production requires far less sunlight and maintenance than intensive agriculture and can thrive within a sloped, shaded landscape.
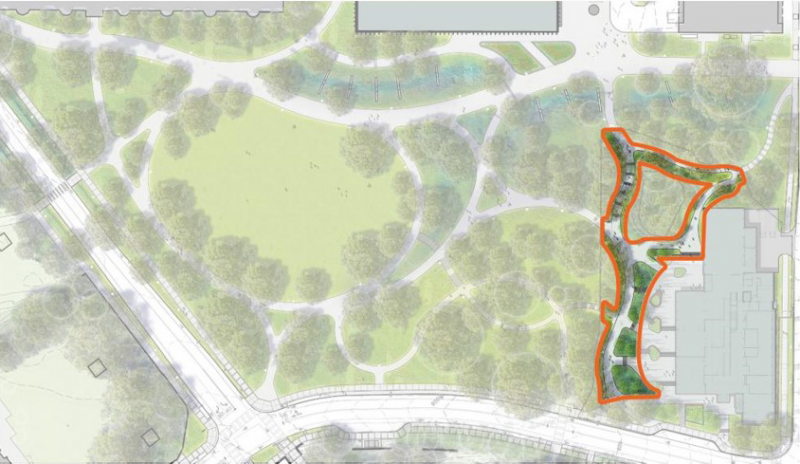
FIGURE 2. Extent of the proposed Edible Landscape. Image courtesy of Andropogon.
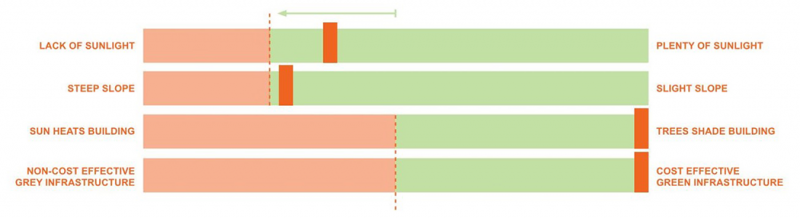
FIGURE 3. Performance indicators for the foraging-driven Edible Landscape. Image courtesy of Andropogon.
The design and client team agrees that the Edible Landscape offers a sound solution to the LBC’s urban agricultural challenge due to the strategy’s ability to:
- Tolerate shade
- Tolerate slope
- Fit within the site boundary (no scale jumping required)
- Shade the Living Building from strong afternoon sun
- Contribute to rainwater management
- Thrive without permanent irrigation
- Produce edibles year-round for people and wildlife
- Meet the project’s budget
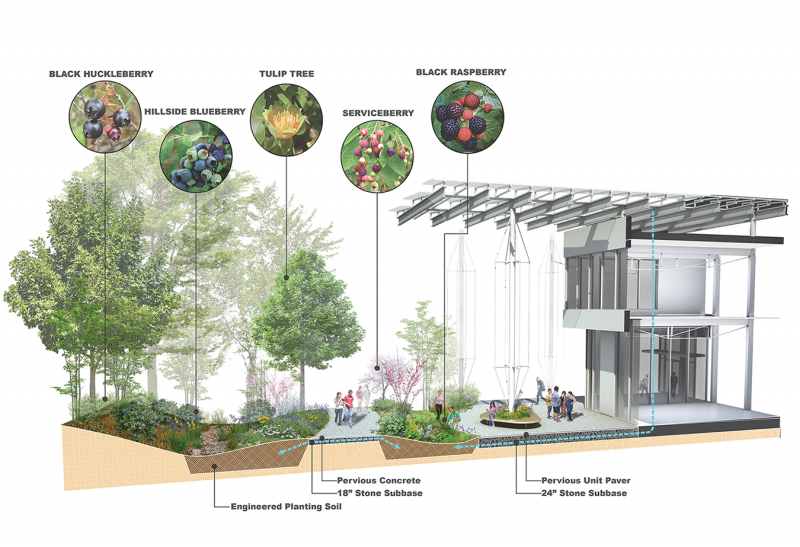
FIGURE 4. Site Section, courtesy of Andropogon.
The Living Building at Georgia Tech’s urban agriculture strategy is part of a larger, site-wide planting approach that provides social benefits (e.g. shade, food, beauty) and ecological services (stormwater management, carbon sequestration, wildlife habitat, pollinator foraging) while taking cues from the region’s local ecology. These characteristics are expected to extend into the adjacent Eco-Commons site, which is in an earlier phase of design.
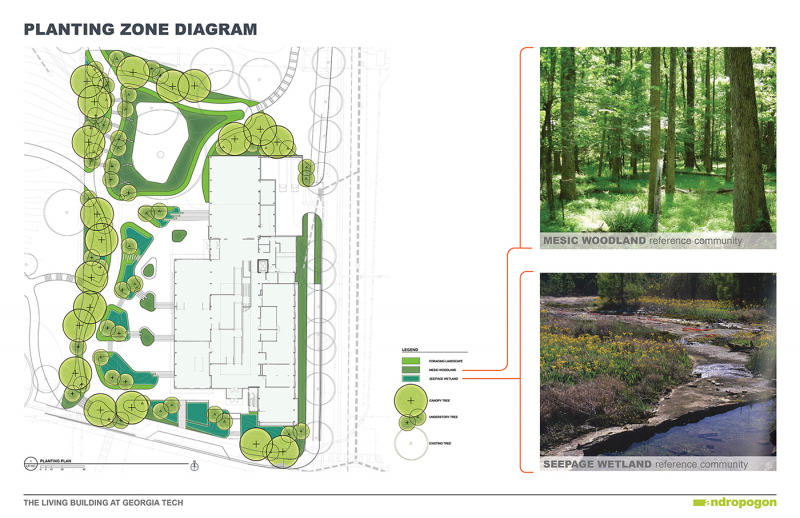
FIGURE 5. Planting zone diagram, courtesy of Andropogon.
Funded through a private grant from The Kendeda Fund, the Living Building at Georgia Tech is expected to become a Living Building Challenge 3.1 certified facility – the built environment's most rigorous and ambitious performance standard. The project’s design and build partners include architects Lord Aeck Sargent in collaboration with The Miller Hull Partnership, construction manager Skanska and design team consultants: Newcomb & Boyd, PAE Consulting Engineers, Uzun + Case, Biohabitats, Andropogon and Long Engineering.
By Ramana Koti, BEMP, LEED AP BD+C, and Andropogon Associates’ José Almiñana, PLA, FASLA, LEED AP, Emily McCoy, PLA, ASLA, and Lauren Mandel, PLA, ASLA
Comments
A Living Building Project Journey, Part-6
Net Positive Energy
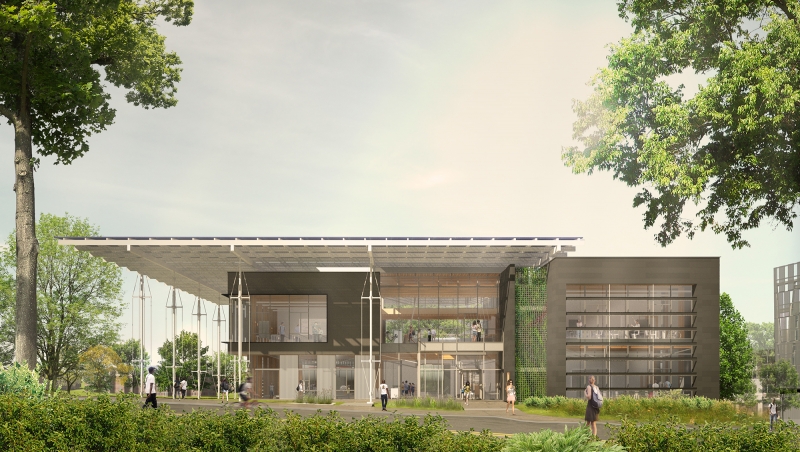
The project is being designed to be “net positive,” producing at least 105% of the energy it consumes, on an annual basis. Successful Living Building Challenge certification requires achievement of the Net Positive Energy Imperative. To accomplish this most cost effectively, design strategies are prioritized with attention first to climate-appropriate passive design, then energy conservation measures (ECMs) and finally onsite renewable energy. ECMs typically yield operational energy savings, but for projects reliant on onsite renewable energy, ECMs serve to reduce the size of the renewable energy system required, thereby offering first cost savings.
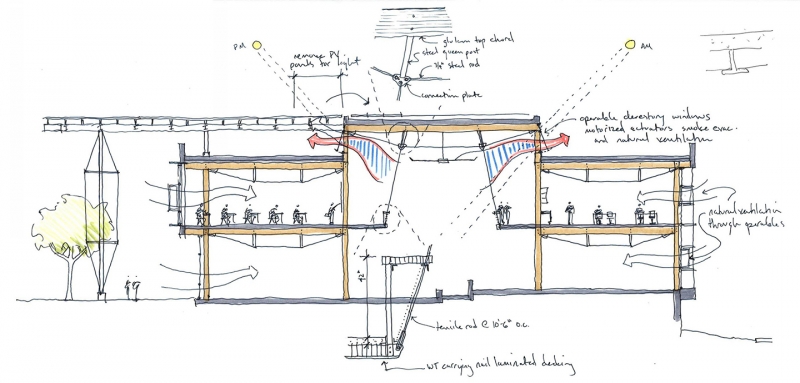
FIGURE 1. A Schematic Section along E-W axis looking at North (Image courtesy: The Miller Hull Partnership)
The amount of intentionality and rigor required in the energy design of a project with a fixed energy budget is remarkable. Decisions about operations have become as important as decisions about design. Factors such as operating hours, thermostat setpoints, plug loads, etc.—items that could otherwise seem trivial—assume enormous importance when the energy budget is constrained and all power must be generated locally. To illustrate this, here are some example energy issues that will continue to be analyzed:
- Can the upper limit of relative humidity (RH%) in some student center spaces be raised?
- Can the project accommodate the energy demands of a programmatically desirable coffee cart?
- How much energy will onsite water treatment strategies, necessary to meet Net Positive Water, require?
- How many laptops, tablets and phones are likely to be charged at convenience outlets on a typical day?
Maximized year-round harvesting of daylighting, natural ventilation during shoulder seasons, and control of unwanted solar gains, including architectural shading devices as well as strategically placed trees, are a few of the core passive design strategies.
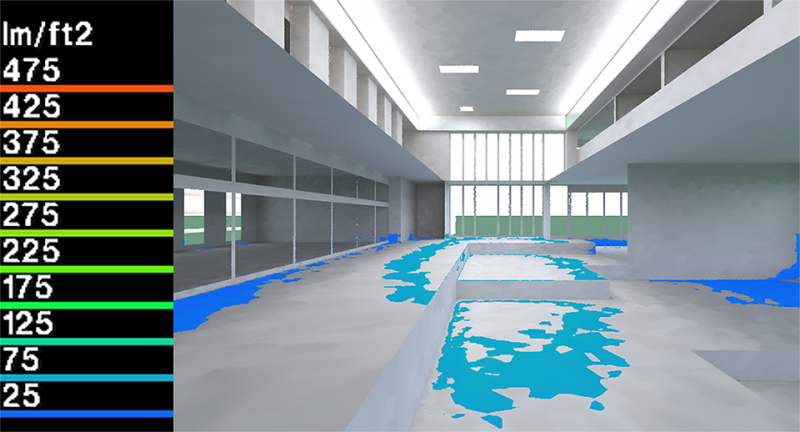
FIGURE 2. An example daylight simulation showing 75 footcandles of daylight on the atrium floor at noon on September 21. (Looking south)
Some of the ECMs under consideration include:
- Triple pane glazing to improve both energy performance and occupant comfort
- Exterior operable venetian shades for solar control and daylight optimization
- Expanded thermal comfort ranges utilizing ASHRAE 55 with an expanded range in some spaces, aided by ceiling fans
- A high efficiency geothermal HVAC system
Design alternatives are evaluated iteratively using energy and heating/cooling loads models managed by PAE Consulting Engineers, the project’s MEP designers, and through daylighting analysis performed by Lord Aeck Sargent and The Miller Hull Partnership.
The project’s current predicted Energy Use Intensity (pEUI) is presently around 28 kBtu/sf/year. About 17,000 square feet of solar photovoltaic (PV) panels will be required to meet the predicted demand. The PV array will multitask by producing energy, collect rainwater and providing shade for the south and west facades.
A net positive energy building requires significant planning and design team coordination to produce a structure capable of meeting the certification requirements. While occupant behavior is always a challenging variable to pin down for predictive modeling, Georgia Tech is currently studying other Living Building Challenge models to better understand how occupant behavior will affect the design, operation and maintenance of the Living Building at Georgia Tech.

FIGURE 3. pEUI being evaluated for different possible ECMs (Image courtesy: PAE Consulting Engineers)
Funded through a private grant from The Kendeda Fund, the Living Building at Georgia Tech is expected to become a Living Building Challenge 3.1 certified facility – the built environment's most rigorous and ambitious performance standard. The project’s design and build partners include architects Lord Aeck Sargent in collaboration with The Miller Hull Partnership, construction manager Skanska and design team consultants: Newcomb & Boyd, PAE Consulting Engineers, Uzun + Case, Biohabitats, Andropogon and Long Engineering.
Comments
But are you JUST?
LAS Earns Its JUST Label
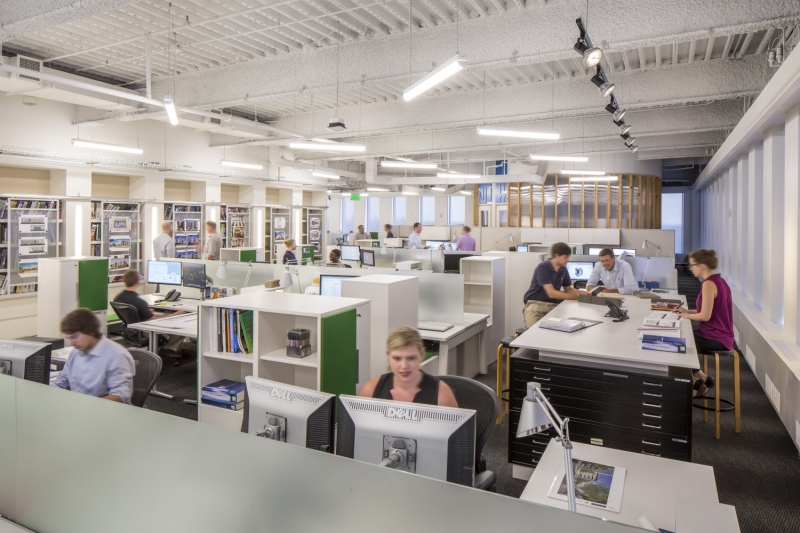
The Living Building Challenge (LBC) doesn’t just compel designers to design resilient, sustainable buildings, it also now gives attention to the workplaces where living buildings are designed, requiring firms to look in the mirror and assess the degree to which they are “JUST.”
While the Place, Water, Energy, Health + Happiness, Materials, and Beauty Petals relate primarily to the built environment, the Imperatives of the Equity Petal seek to support “a just, equitable world.” Its requirements include the creation of human-scaled places, universal access to nature, charitable contributions and, as of Version 3 of the LBC, a JUST Organizations Imperative. This Imperative requires that at least one of the project team members have a JUST Label for their organization.
Undertaken as part of our work on the Living Building at Georgia Tech, Lord Aeck Sargent earned its JUST Label on February 3, making the firm among the first 20 architecture firms in the world to achieve a JUST Label.
The program supports voluntary disclosure of business policies and practices as a vehicle for positive social change.
“Similar to the Living Building Challenge’s Declare program, the JUST program serves as a ‘nutrition label’ for socially just and equitable organizations.” – Just. User Manual
Firms must report performance on 22 “Indicators” organized by topics of Diversity, Equity, Safety, Worker Benefit, Local Benefit and Stewardship. A firm’s policies and performance—scored at a zero-, one-, two-, or three-star level for each Indicator—are publicly disclosed on the JUST website. An organization cannot fail to obtain a JUST Label if the process is completed, though they might not like the results: transparent disclosure of performance provides the impetus for positive change.
Lord Aeck Sargent began by forming a JUST Label task force with representatives from business operations, human resources, firm leadership and the design team. A tracking spreadsheet was created and each of the 22 Indicators assigned to a task force member. A preliminary ‘gap analysis’ was conducted to review and assess current policies and likely performance against the JUST label policy and performance criteria. Where policies did not exist, they were drafted and adopted.
In our case, the need to create policies/statements for nine indicators was identified (Union Friendly, Hazardous Chemicals, Worker Happiness, Local Control, Local Sourcing, Responsible Investing, Positive Products, Charitable Giving and Transparency).
Once the requisite policies were identified, or drafted and approved where necessary, they were uploaded to the JUST web portal and the corresponding performance data was collected and uploaded as well, where required.
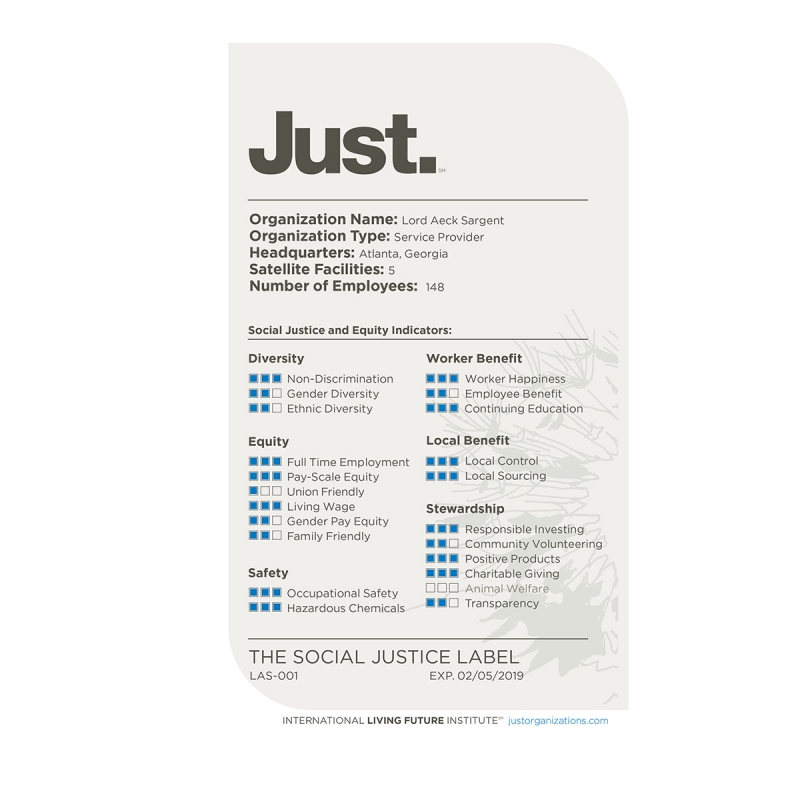
Taking just under a year from start to finish, the JUST Label process provoked passionate, in-depth discussions about the mission of the firm in the context of social equity and justice. The Worker Happiness Indicator required a two-question staff survey assessing job satisfaction and likeliness to recommend Lord Aeck Sargent as a good place to work, on a scale of one-to-ten. We expanded the survey to include a field for comments on each question and found the comments provided great insights into what we do well, such as creating a positive, balanced firm culture and supporting professional development; as well as some areas with room for improvement, such as articulating a clear vision and providing resources for project managers, which we’ll attempt to address in the coming year.
I believe that Lord Aeck Sargent is a better firm for having pursued and achieved a JUST Label, and I look forward to leveraging the program, with its two-year recertification cycle, as a tool for ongoing improvement as we focus on further opportunities to improve our lower-scoring Indicators.
Comments
A Living Building Project Journey, Part-5
Water Balance
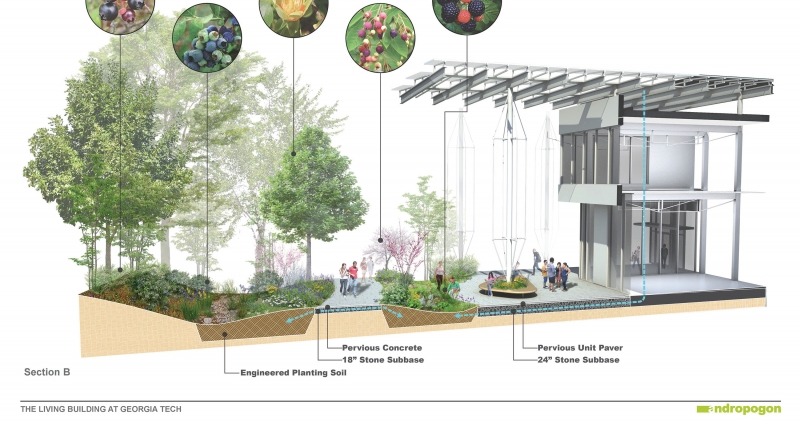
During the Schematic Design phase*, ‘Petal’ workshops were organized to highlight the design and operational implications of each of the seven Petals under the Living Building Challenge (LBC), one Petal at a time. This post will summarize the discussion from the Water Petal workshop, held in November 2016 and led by Biohabitats Inc., which is designing the building’s systems to capture, treat and recycle water.
In brief, the ‘Net Positive Water’ Imperative under the Water Petal requires that the project collect 100 percent of its water from a combination of captured precipitation and recycled project water. The building must also treat or process its own waste. In other words, the project becomes its own water utility without any reliance on municipal sources, a closed loop system without conventional “supply” and “waste.”
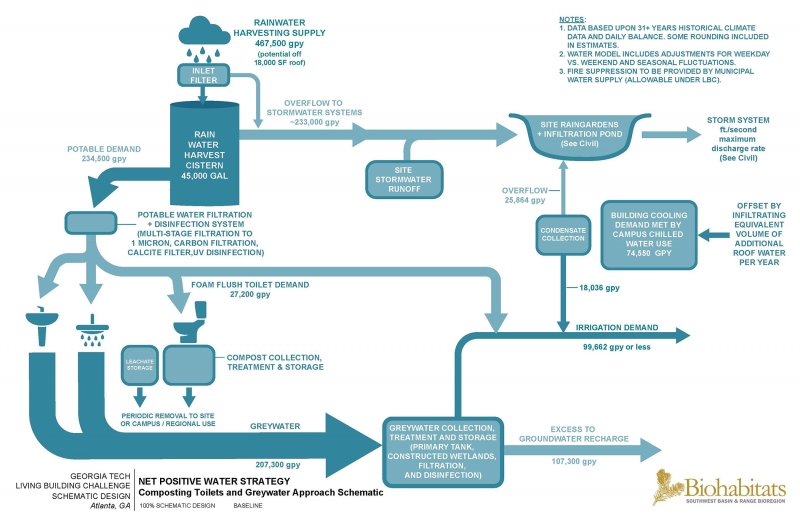
Net Positive Water Strategy
Atlanta receives a generous amount of rainfall that has averaged 50 inches annually between 1981 and 2010. However, a recent prolonged drought and rising sewer bills have made water a regionally critical issue. Having very limited available groundwater, Atlanta relies on rivers, streams and reservoirs for its municipal water supply. The City is relatively close to the headwaters of these rivers and streams, which limits the ability to withdraw water sustainability; as a result water is often highlighted as the resource that will constrain growth in the region. Rapid urbanization, coupled with a combined sewer system serving the downtown core, has also resulted in serious stormwater treatment challenges. These regional concerns, coupled with LBC’s Water Petal requirements, demanded a holistic approach to the project’s water balance. The strategy, outlined in the process diagram above, includes a few key elements that allow the building to be self-sufficient when it comes to water.
- Treated rainwater, collected from the building roof, stored in a cistern and purified, will be the potable source of water for the building, providing water for drinking fountains, bathroom sinks and showers.
- Composting toilets will greatly reduce the amount of water required for toilets while also eliminating the need to treat the ‘blackwater’ produced by conventional toilets. The compost products are useful soil amendments.
- Greywater (waste water from sinks and showers) from the bathrooms will be treated using constructed wetlands and then recycled to be used for irrigation or groundwater recharge, mimicking the natural hydrological cycle.
- Stormwater runoff from the site will infiltrate in raingardens and ponds, enhancing the landscaping while preventing overburdening of the municipal system.
Except for one initial fill of cisterns, no municipal water usage is allowed under LBC requirements. A sensitivity analysis that took LBC requirements and the possibility of prolonged droughts into account resulted in a conservative cistern sizing of 45,000 gallons for a 43,000 sf building. Two parallel filtration, disinfection and pump systems for rainwater treatment will provide redundancy to ensure that water is always available.
One of the most interesting points addressed during the Water Petal workshop was the energy intensity of water treatment, which is often overlooked in discussion of building energy efficiency measures and opportunities. It is currently estimated that less than 10% of the project’s overall energy consumption will be related to water treatment, mostly from powering pumps. This amounts to about 3 of the current modelled total EUI** of 27 for the building (EUI=kBtu/sf/year).
From an operational standpoint, it also emerged that a potential system breakdown or interruption necessary for system repairs only requires a temporary pause, and not a full reset for LBC’s 12-month performance period (The project needs to demonstrate net positive water usage over a 12-month performance period).
Some of the details for focus during the next design phase include:
- Water treatment without chemicals
- Testing frequency, costs and consequences of unfavorable results
- Detailed metering for net positive water usage demonstration
- Permitting for rainwater to potable water (only greywater reuse is currently permitted under Atlanta regulations)
* The initial design phase of a project, when the architect typically begins to develop and illustrate the project design, developing and documenting spatial relationships, scale and form
** Energy Use Intensity (EUI)
Funded through a private grant from The Kendeda Fund, the Living Building at Georgia Tech is expected to become a Living Building Challenge 3.1 certified facility – the built environment's most rigorous and ambitious performance standard. The project’s design and build partners include architects Lord Aeck Sargent in collaboration with The Miller Hull Partnership, construction manager Skanska and design team consultants: Newcomb & Boyd, PAE Consulting Engineers, Uzun + Case, Biohabitats, Andropogon and Long Engineering.
Comments
A Living Building Project Journey, Part-4
Design Panel Discussion
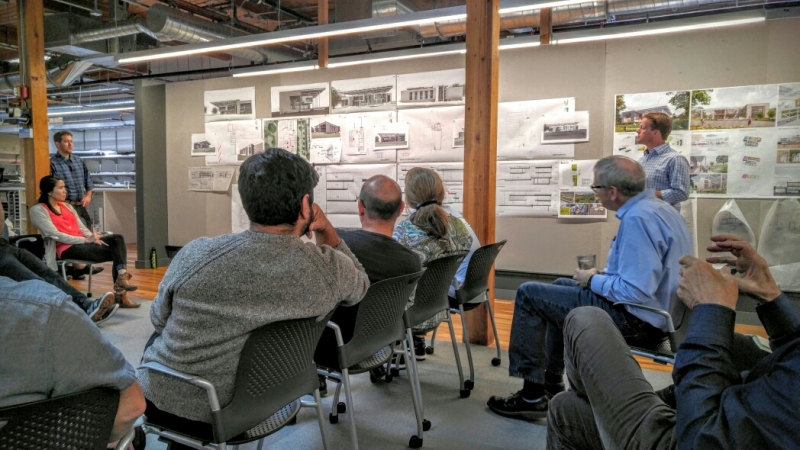
From the ‘Porch’ and ‘Bridge’ concepts developed during the Ideas Competition, the Porch concept was selected by Georgia Tech for further development due to the manner in which it directly engaged the surrounding Eco-Commons. This was not an easy decision given that the longer facades of the building had less desirable east and west solar orientation. The porch specifically faced west. The Schematic Design (SD) phase began with the development of the Porch concept and a key goal of tackling the challenging west-facing connection to the Eco-Commons.
Early in SD, design team members of all disciplines huddled together in Miller Hull’s Seattle office for a focused, interdisciplinary workshop that moved the design forward considerably in a few short (actually long) days. It was a collaborative process rooted in asking questions first and designing later. Iterative shading and daylight studies were employed to enable performance to inform formal considerations.
During an in-house ‘Design Panel’ forum, open to both the project team members of all disciplines as well as interested Miller Hull staff, a wide range of rich topics emerged encompassing formal, philosophical and environmental concerns. This post will highlight a few of the issues discussed in an attempt to capture the spirit of the event.
Is the building subservient to the solar power plant, or vice versa?
During the Ideas Competition, the photovoltaic (PV) array was subservient to the overall building form. But as an occupiable roof was identified as a programmatic goal, the PV array height was raised to provide a shaded occupiable zone on the roof. While programmatic and budgetary concerns may ultimately dictate another solution, the question of whether the building should be subservient to the PV array or if the PV array should be subservient to the overall building form generated energetic discussion.
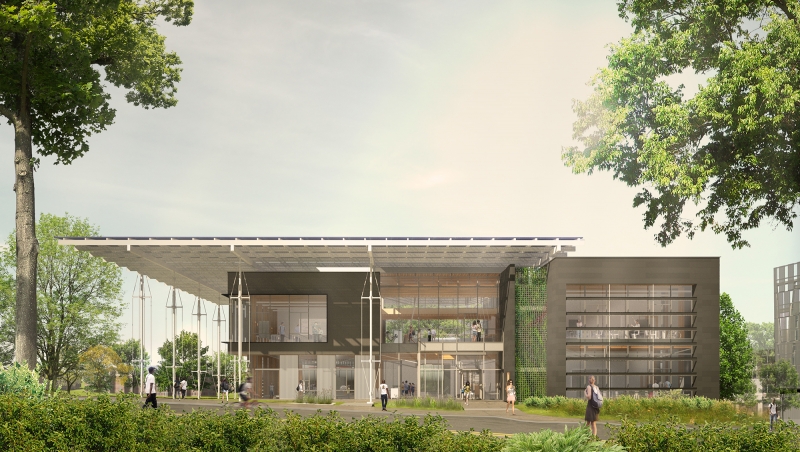
FIGURE 2. South façade.
Is the idea of a passive porch compatible with other active features?
The porch performs several functions. Besides providing prospect and refuge, one of the objectives is for the porch to passively temper the harsh western solar exposure. Of particular concern is the challenging low-angle late afternoon sun of summer and shoulder seasons. The variables at play include energy performance, thermal comfort, visual comfort and occupant control.
Philosophically, how compatible is the idea of a (passive) porch with a more active product like electrochromic (electric-tinting) or thermochromic (heat-tinting) glazing?
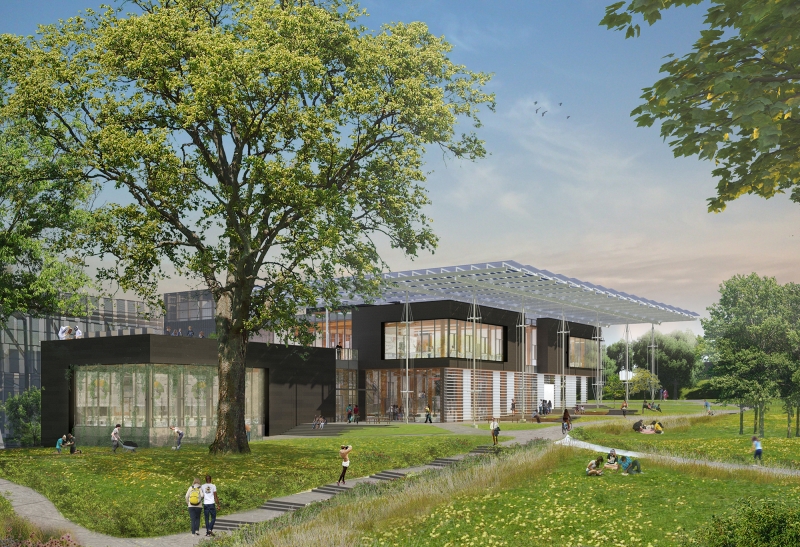
FIGURE 3. A view of the site and the west-facing porch.
Appearance: sophisticated or rustic?
There was some concern that the appearance of the building in some preliminary renderings was too artificial-intelligence or machine-like. A diametrically opposite masonry-based approach, where each block was handcrafted by local artists or craftsmen, was suggested as a more human/humane expression.
Whether windows should be multiple punched openings or comprised of large swaths of uninterrupted glazing was also discussed. The need to visualize spaces from both the inside and the outside was stressed.
Form follows function and design for loose fit
One suggestion was that the design of the auditorium space metaphorically and formally mimic a beehive or a wasp nest structure.
Given the ‘long life, loose fit’ approach, the challenges to designing for a program that could change in the future were also discussed.
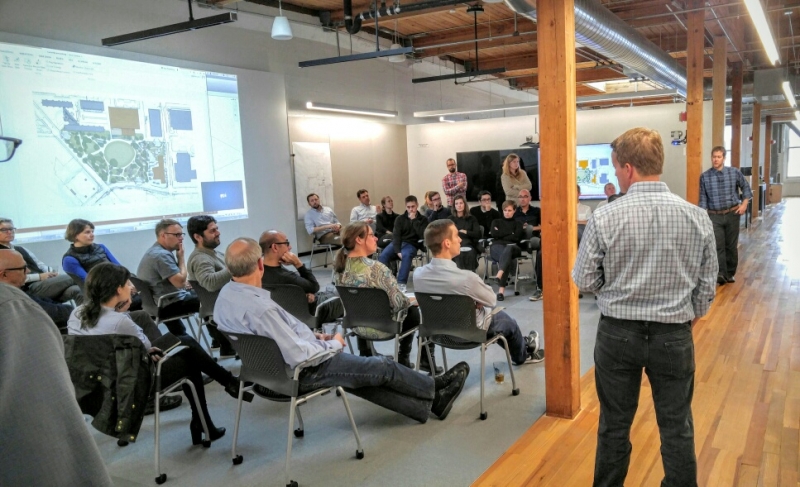
FIGURE 4. Design Panel in progress.
Note: All renderings are schematic explorations and are not meant to be photorealistic representations of the actual appearance of the project. This post neither reflects the entire discussion nor conveys the present status of the design fully. It is a snapshot meant to provide a flavor for the thinking behind the project. Due to the open nature of the Design Panel, it is also difficult to provide credit to individuals for their contributions to the discussion.
Funded through a private grant from The Kendeda Fund, the Living Building at Georgia Tech is expected to become a Living Building Challenge 3.1 certified facility – the built environment's most rigorous and ambitious performance standard. The project’s design and build partners include architects Lord Aeck Sargent in collaboration with The Miller Hull Partnership, construction manager Skanska and design team consultants: Newcomb & Boyd, PAE Consulting Engineers, Uzun + Case, Biohabitats, Andropogon and Long Engineering.
Comments
A Living Building Project Journey, Part-3
The Materials Working Group
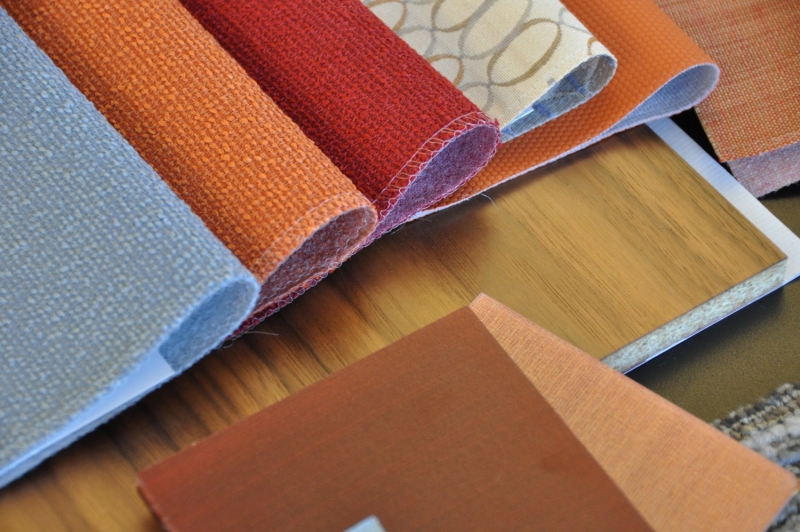
As this post is being written, the Living Building at Georgia Tech project has just entered the schematic design phase. Wood, steel, and concrete are currently under consideration for the structure system, and a hybrid approach cannot entirely be ruled out. For exterior cladding, cement board, stone veneer rain screen, terracotta rain screen, brick, and other materials are being evaluated.
It is worth reiterating that the Red List requirements under the Living Building ChallengeTM (LBC) Materials Petal make material/product specification as challenging, if not more, as achieving net-positive energy and net-positive water.
A Materials Working Group was formed to tackle the challenges of compliance with the Materials Petal and had its kickoff in August. Meeting monthly, the participants in this working group include representatives of the architectural firms, the construction manager, and the donor.
One of the first tasks was the review Georgia Tech’s Design Standards (“Yellow Book”) for the most-required materials and products and their alignment with the LBC Materials Petal’s Red List requirements. While the Yellow Book is very rigorous in mandating environmentally friendly choices, requirements for PVC piping, fluorescent lighting (mercury), and potentially problematic foam products are in conflict with the Red List. Sole-sourcing requirements will be investigated as the project progresses. This project is expected to play an important role in informing future development of the Yellow Book.
The primary focus so far has been on developing a process for vetting and documenting product selections based on Red List compliance. The following graphic, still evolving, illustrates the priorities for materials and products on the project, and the iterative vetting and research process that is utilized to achieve these priorities.
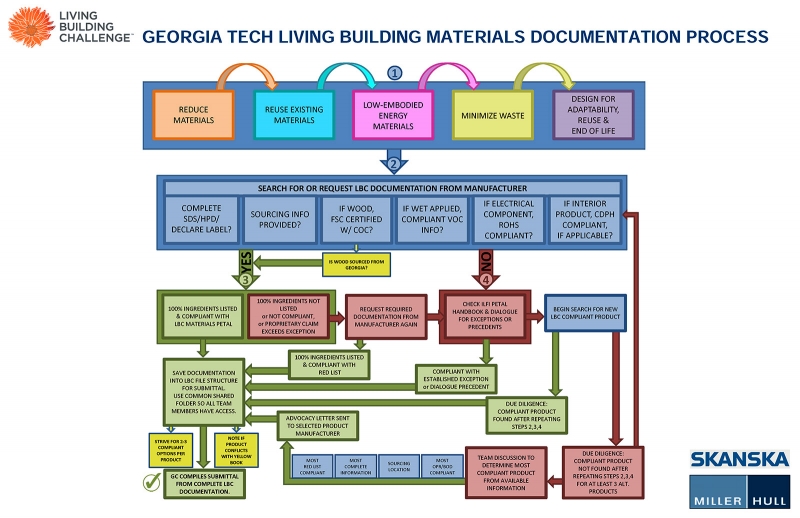
Two important steps of the process illustrated in the diagram are currently underway:
- From the universe of all available options, developing a shortlist of materials/products that have a high likelihood of being specified for projects of this type (institutional campus building), followed by ranking them in an order of relative compliance with project material priorities and the Red List.
- From the universe of all available manufacturers, compiling a shortlist of manufacturers for the Materials Working Group to interact with for their research and vetting process.
At this point, it is recognized that the project will contain wood for one or more of structure, casework, furniture, etc. And when it comes to LBC certification, all wood specified on the project has to be Forest Stewardship Council (FSC) certified. Given the challenges in Georgia to using green building rating systems that advocate FSC certified wood on state projects, the Materials Working Group is closely coordinating their efforts with Georgia Tech with the goal of developing viable options, including salvaged wood, and serving as a catalyst for increasing the availability of sustainably managed forest products in the state.
Several custom-designed spreadsheet and survey-based tools and resources are being used for the material vetting and selection process during the early design phases. Compliance documentation will shift to LBC-mandated formats at later stages. One of the most important outcomes of such an atypically collaborative process has been the use of shared public folders and files. The materials working group has so far successfully relied on Newforma and Google Drive to allow the diverse team (in terms of both geography and discipline) to all work out of the same files, keeping shared data current.
Future posts will have further updates on the progress made by the Materials Working Group. We’re hoping to report on the project’s Biophilic Design efforts in the next post.
Funded through a private grant from The Kendeda Fund, the Living Building at Georgia Tech is expected to become a Living Building Challenge 3.1 certified facility – the built environment's most rigorous and ambitious performance standard. The project’s design and build partners include architects Lord Aeck Sargent in collaboration with The Miller Hull Partnership, construction manager Skanska and design team consultants: Newcomb & Boyd, PAE Consulting Engineers, Uzun + Case, Biohabitats, Andropogon and Long Engineering.
Comments
A Living Building Project Journey, Part-2
Snippets from the Charrette
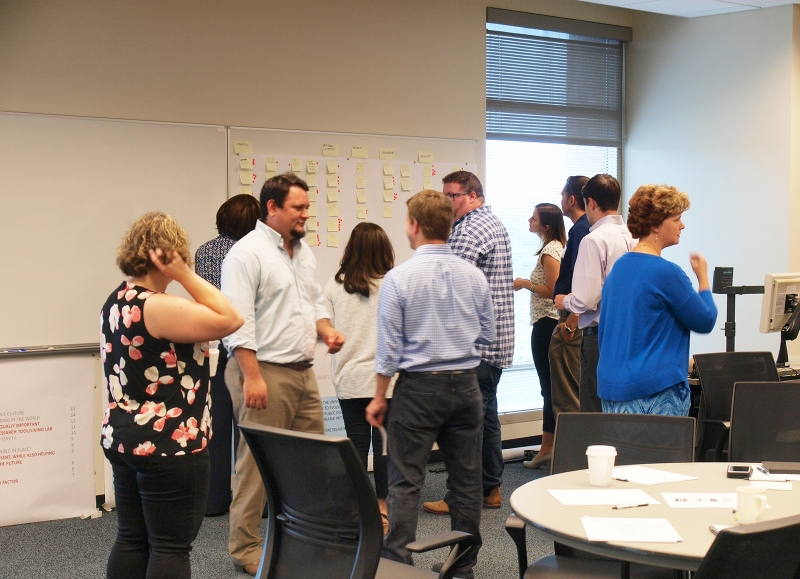
To say that the two-day long charrette was eventful would be an understatement. Broadly, the first day collected stakeholder feedback, while the second day turned the feedback into action items for the design process. From individual goal setting (which was subsequently voted on collectively to rank project priorities), to brainstorming of the top five ideas by interdisciplinary groups, no stone was left unturned. To cite one ambitious goal, one participant felt that the building’s appeal should lead to it being sought after for social events like weddings. To indicate one creative idea, a ‘Pokémon Go’ styled augmented-reality method was suggested for learning about the building after it was built, where every material would have a QR code that could be scanned and explored further. A sampling of some of the strong themes which emerged follows, not in any order of priority.
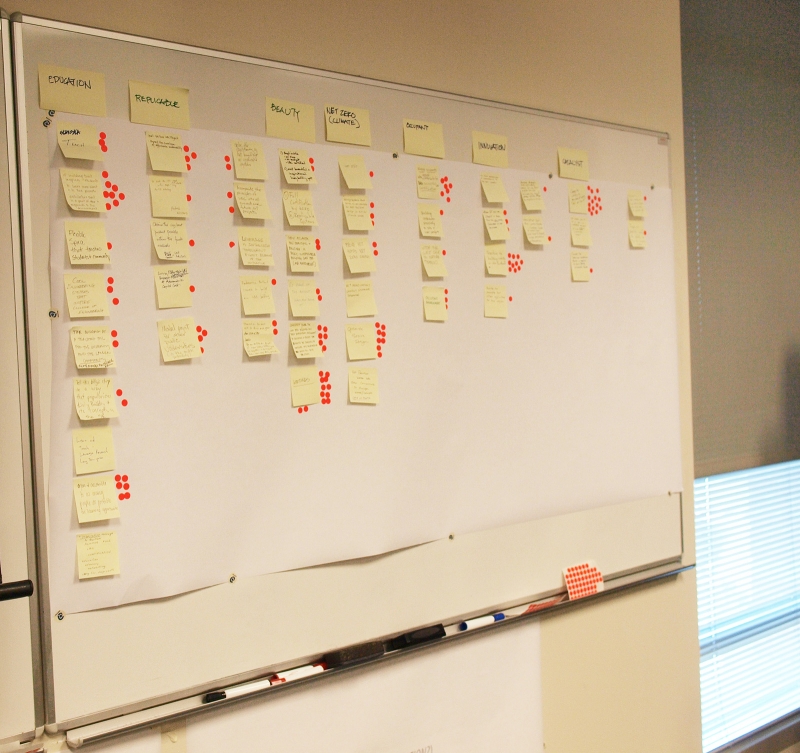
Goals, ranked and ready for use.
Urban Agriculture
Urban agriculture, an imperative under the Place Petal of the Living Building Challenge (LBC), evoked an unexpectedly strong response from a cross section of participants. The core of exploration of this topic hinged on soliciting an understanding of what Urban Agriculture truly meant for Georgia Tech (GT), in the context of both their immediate campus and surrounding metropolitan Atlanta. What is the right scale of such an intervention? Would there be an active champion? How would the building’s urban agriculture fit into the institution’s broader urban agriculture strategy now under development? It was suggested that given the existing need for local and healthy food, GT should lead the process of creating a market for urban agriculture. Here are some noteworthy strategies that were discussed:
- Goats on the roof
- Growing hops that would create a Living Building IPA brand
- Bringing peach trees back to Peachtree Street
- Bringing a farmer’s market into the building
- Use of composting toilet leachate to fertilize urban agriculture
- Determining the urban agriculture scope based on the available water budget
- Bio-centric vs. Anthropocentric agriculture (other species need food too)
The need for an urban agriculture subcommittee was recognized.
Site
The site will have to be a smaller portion of the broader adjacent planned Eco-Commons district. Defining the extents of the site started with a series of questions.
- What services does the site need to provide?
- Treat greywater, collect rainwater, house urban agriculture, house geothermal wells, etc.
- How does the LBC site interface with adjacent sites?
- How would the contractor use the site for staging and conveyance?
- How will the existing site topography accommodate universal design?
- What are the considerations for promotion of biodiversity of landscape and animals?
- Can an outdoor space for a gathering of 500 people be accommodated?
- How can biophilic aspects such as ‘prospect and refuge’ and ‘fear and awe’ be accomplished?
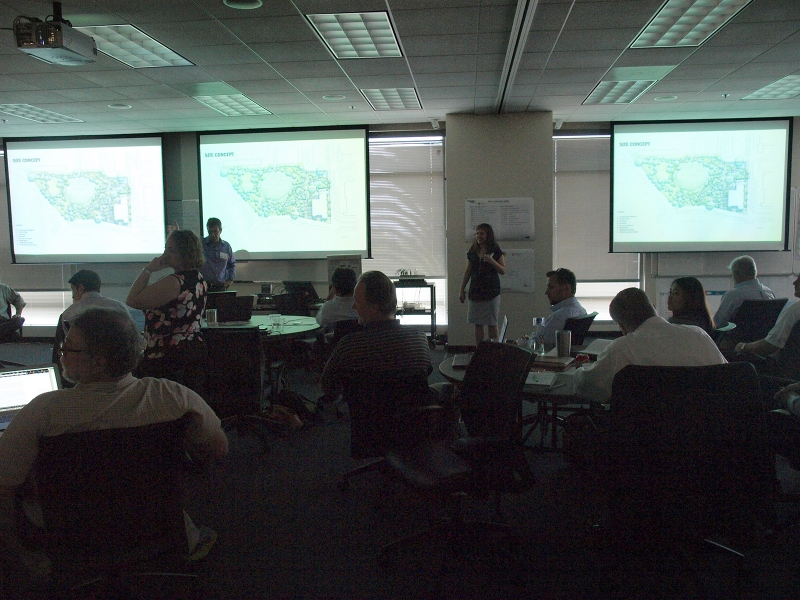
A discussion on the site.
The questions set off a process that will eventually lead to the determination of the LBC Site Boundary and a context for the building and the services it requires. One of the clearly stated objectives was to blur the line between the outside and the inside.
Materials
While Red List chemical avoidance lies at the heart of the LBC Materials strategy, other aspects such as procurement timeline, cost impacts, durability, etc., require careful planning. Based on collective previous LBC experience, it was anticipated that about 1,000 materials would have to be vetted, at a time expenditure of eight hours per material. To put that in perspective, if only one person spent 40 hours a week on material vetting, the complete exercise is roughly a four-year time commitment.
It is also expected that achieving the ‘Responsible Industry’ imperative under the Materials Petal will be a formidable challenge. The imperative requires that all wood on the project be Forest Stewardship Council (FSC) certified. On most other projects this would be a simple matter of writing up a tight specification but in Georgia, especially on state-funded projects, legislation forbids the use of green building rating systems that work against employment of locally produced timber which uses other less rigorous certification standards supported by the local forest products industry. There are nuances to the nature of funding and the political nature of the challenge, but they are detailed enough to merit their own future blog post.
Towards the end, a ‘materials working group’ was established comprising of people from the design and construction management teams. The materials working group intends to get an early start on materials research.
Architecture and Solar Control
Fenestration design that integrates aspects of solar control and daylighting will be key to achieving net positive energy and occupant satisfaction. Passive site features such as trees and sculptures that cut solar gain on the east and west-facing glazing figured heavily in participant feedback. Also recognized was the need for balancing such features with something akin to a screen on the façade of the building that occupants can control to more readily modulate their environment.
Biophilia
E O Wilson’s definition of Biophilia, the innate tendency of humans to focus on life and life like processes, was invoked. A one-hour discussion on Biophilia during the kickoff laid the groundwork for a future day long exploratory session, which is an LBC requirement. The eventual goal is to create a biophilic framework and plan for the design. The following priorities were identified for the approach to incorporating Biophilia:
- The need to take an evidence-based middle path between the extremities of being a ‘mindless cheerleader’ and a ‘Debbie Downer’
- The need for buildings to go beyond simply copying forms from nature to actually functioning like nature
Strategies such as a green wall that doubled as a greywater treatment system and building enclosures which functioned as selective membranes were identified.
Others
Each of the subtopics can be comprehensive enough to deserve a dedicated post but we will end with a summary list of those that did not figure in the detailed themes above.
- A comprehensive approach to water balance with the involvement of regulatory agencies
- First cost and operational cost implications of composting toilets and constructed wetlands for blackwater treatment
- Conversion of rainwater into potable water
- Onsite greywater treatment
- Rethinking of the traditional thermal comfort model to inform net positive energy design and broader GT policies
- A dashboard that goes beyond tracking energy and water performance and tracks other metrics such as health, happiness, and physical activity. The need for making the feedback more visceral for occupants was stressed.
- Programming with flexibility in mind
- Community engagement and leverage activities. Two examples:
- Georgia Tech Research Institute’s (GTRI) research on lowering the installation costs of Photovoltaics
- Center for Disease Control (CDC) and Emory’s feedback in creating a healthy environment
- Pedagogy
- Student involvement in materials research during design states
- Exploration of how and where students and building users will learn best
- Didactic role of the building
- An integrative approach delineating areas for CM and subcontractors to collaborate in the design process
- Lessons from other LBC projects
Funded through a private grant from The Kendeda Fund, the Living Building at Georgia Tech is expected to become a Living Building Challenge 3.1 certified facility – the built environment's most rigorous and ambitious performance standard. The project’s design and build partners include architects Lord Aeck Sargent in collaboration with The Miller Hull Partnership, construction manager Skanska and design team consultants: Newcomb & Boyd, PAE Consulting Engineers, Uzun + Case, Biohabitats, Andropogon and Long Engineering.
Comments
A Living Building Project Journey, Part 1
Setting the Stage
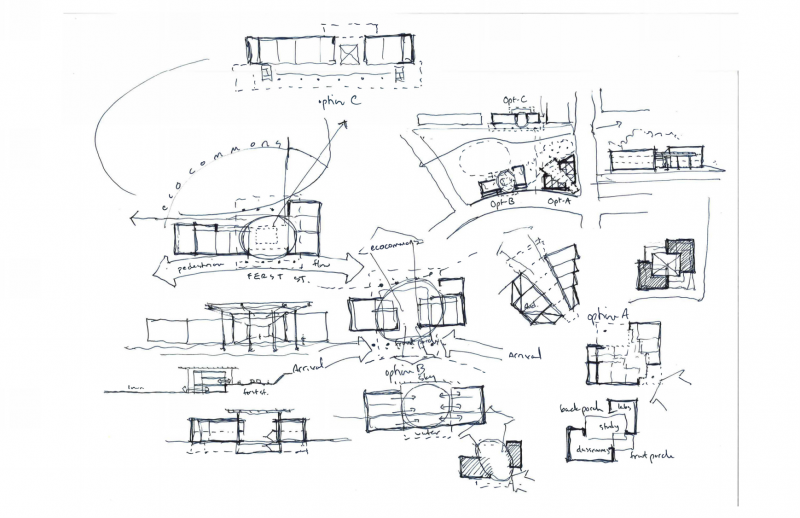
Introduction
After a multi-stage, national selection process which culminated in a two-month ideas competition lead by Georgia Tech, the Lord Aeck Sargent (LAS) / The Miller Hull Partnership (Miller Hull) team was selected to design the first Living Building Challenge (LBC) certified building in the southeast. This is LAS’s second LBC project on the boards and we expect this blog post to be a first in a series documenting the exciting journey.
There are several resources for an in-depth dive into the LBC framework with its Petals and Imperatives but it is worth noting here that the LBC, in the International Living Future Institute’s own words, “is a philosophy, certification, and advocacy tool for projects to move beyond merely being less bad and to become truly regenerative.” It seeks to build an enlightened team of designers, consultants, owners, operators, and occupants who are ever-cognizant of the impact of their decisions and actions leading up to the certification.
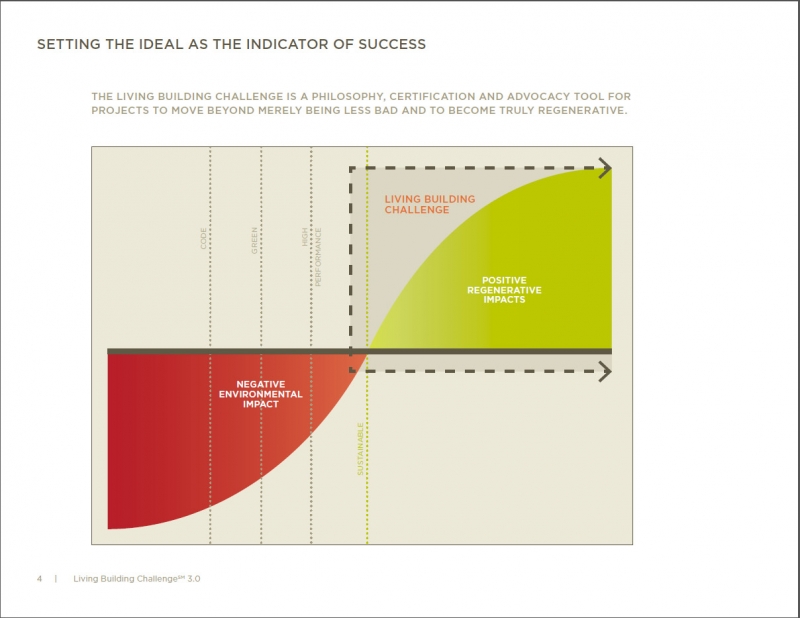
During the design process, no question or concern is too small when it comes to this all or nothing (almost) green building framework with its twenty imperatives. Some early questions and discussions have included:
- Is the most appropriate transect L3 or L4?
- Is a national design team with consultants on both coasts acceptable under the LBC travel distance limitations?
- Would the use of salvaged steel help with the embodied carbon footprint reduction?
- Are there exceptions to the ‘no combustion’ rule when it comes to laboratories?
Beyond detailed considerations of the various program requirements, some broad issues are emerging as high-impact areas. While it is tempting to make this post into a dissertation on the Living Building Challenge, we’ll focus on three issues which illustrate the process to date.
Integrative Design Process
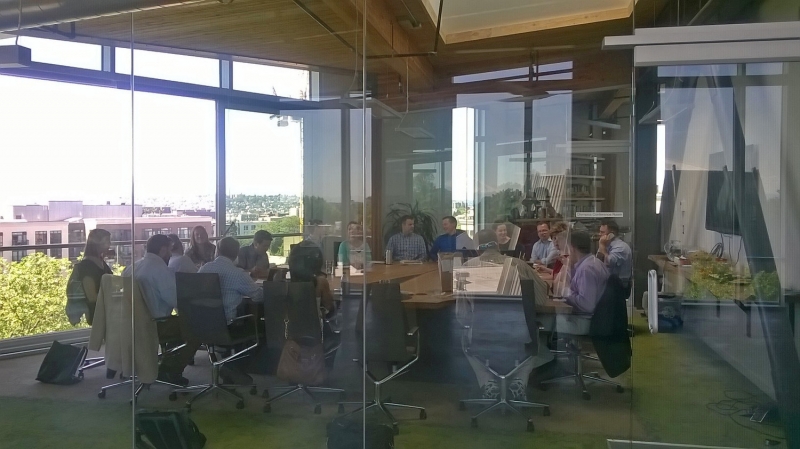
The LBC framework is a forcing function for an integrative design process. It is difficult to accomplish much without the left hand knowing what the right is doing. As we are planning a 2-day “super charrette” and an 8-hour Biophilia charrette, each of our bi-weekly team meetings since the beginning of the project has been a charrette in itself. This has had a transformative impact on the quality of the design process. For example, the quantity and quality of attention given to understanding the site before considering the building itself, and the focus on blurring that boundary, has been extremely exciting.
It’s Very Materialistic
Materials petal requirements, specifically the Red List imperative, will require a new design paradigm. The Red List, with 20+ materials or chemicals to be avoided, encompasses 777 or so chemical compounds once all the variations are taken into account. While there are resources available to marginally help with the Materials petal, we are preparing for:
- deep material research and vetting, and
- deep interaction with manufacturers for information that may not be readily available
Fortunately, there are cautionary tales to learn from: A consultant who is still writing Red List advocacy letters two years into occupancy; an architect who wasted hours looking for lead-free brass door hardware not realizing there was an exception; and a contractor who installed structural insulated panels before noticing the manufacturer had sent SFI-certified version of the product instead of the required FSC-certified.
JUST Certification
The LBC process touches not only design process, but also design team culture . At least one representative from the design team (Architect of Record, Landscape Architect of Record, MEP of Record, etc.) is required to achieve JUST certification. JUST certification aims to “help create a more just, equitable society through disclosure of the business practices of the major organizations” involved in the project. The 22 JUST Label Indicators range from objective measures such as gender diversity to more subjective measures like worker happiness.
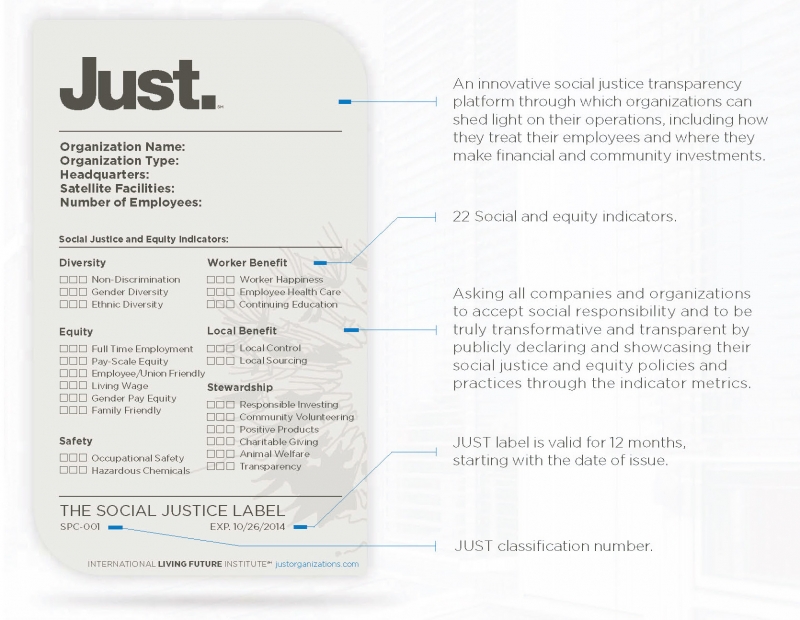
We have formed an internal working group, conducted a gap analysis of our existing policies, and are now developing new policies as needed. It would be an understatement to say that the process has sparked intense conversations.
Conclusion
We’ll continue to share our experience on this journey with future blog posts about this LBC journey. Please share your perceptions of and experiences with the LBC process? We look forward to reading them in the comments section.
Funded through a private grant from The Kendeda Fund, the Living Building at Georgia Tech is expected to become a Living Building Challenge 3.1 certified facility – the built environment's most rigorous and ambitious performance standard. The project’s design and build partners include architects Lord Aeck Sargent in collaboration with The Miller Hull Partnership, construction manager Skanska and design team consultants: Newcomb & Boyd, PAE Consulting Engineers, Uzun + Case, Biohabitats, Andropogon and Long Engineering.